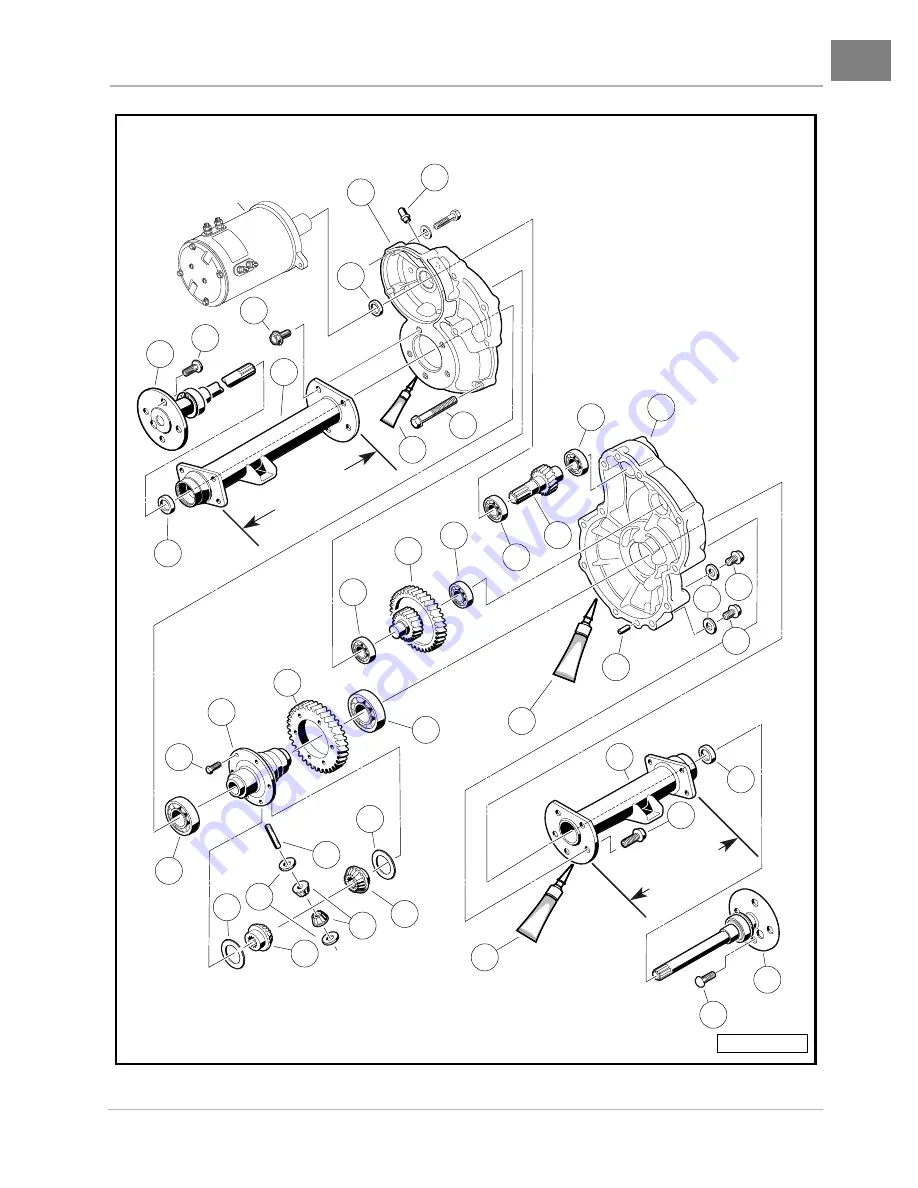
TRANSAXLE (TYPE G)
Axle Bearing and Shaft
2008-2011 IQ Plus Electric Vehicle Maintenance and Service Supplement
Page 17-3
17
Figure 17-5 Transaxle – Type G
1
3
14
15
REFERENCE
MOTOR
24
26
13
33
36
32
8
10
11
12
20
18
19
16
16
16
17
23
21
25
36
22
35
13
27
30
31
29
2
3
8
36
15
27
30
28
50.
4 cm
25.
3 cm
000223-002