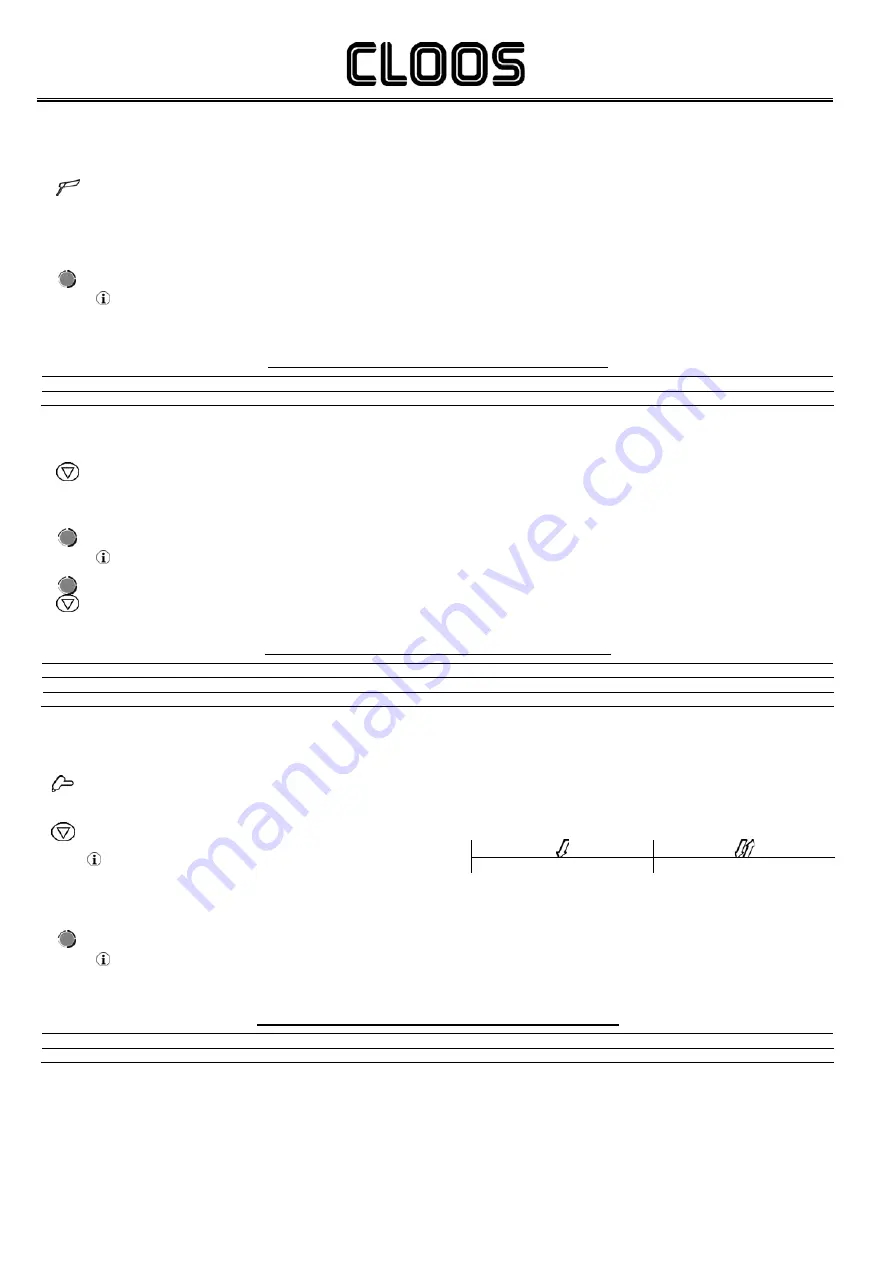
Cod.006.0001.1362
25/03/2013 v2.0
ENGLISH
Micro 300
16/32
10
WELDING SETTINGS
10.1
ELECTRODE WELDING (MMA)
SEL1
Set the selector to the symbol to select MMA welding mode
MMA The message appears on displays D2
10.1.1
MMA
P
ARAMETERS
S
ETTING
(1
ST
L
EVEL
)
E1
Using the encoder, edit the value of the selected setting
Tab. 5 Parameters of the 1st level Menu in MMA mode
80 The value relative to the selected setting appears on display D1
Tab. 5 Parameters of the 1st level Menu in MMA mode
PARAMETER MIN
DEFAULT
MAX
NOTES
-
MMA WELDING CURRENT
10A
80A
250A
10.1.2
MMA
P
ARAMETERS
S
ETTING
(2
ND
L
EVEL
)
S2
Hold down the button for 3 seconds to gain access to the 2nd level Menu
H.-S. The acronym relative to the setting to be edited is shown on display D1
50 The value relative to the selected setting appears on display D2
E1
Use the encoder to scroll the list of settings to edit
Tab. 6 Parameters of the 2nd level Menu in MMA mode
E2
Using the encoder, edit the value of the selected setting
Press any button to save the setting and quit the Menu
Tab. 6 Parameters of the 2nd level Menu in MMA mode
PARAMETER MIN
DEFAULT
MAX
NOTES
H.S.
HOT-START 0%
50%
100%
A.F.
ARC-FORCE 0%
30%
100%
10.2
DC TIG WELDING
SEL1
Set the selector to the symbol to select TIG welding mode
tIG The message appears on displays D2
S5
Press the button to select the torch trigger procedure
The following torch trigger procedures are available:
(2 STEPS)
(4 STEPS)
10.2.1
DC
TIG
MMA
P
ARAMETERS
S
ETTING
(1
ST
L
EVEL
)
E1
Using the encoder, edit the value of the selected setting
Tab. 7 1st level Menu parameters in continuous TIG mode
80 The value relative to the selected setting appears on display D1
Tab. 7 1st level Menu parameters in continuous TIG mode
PARAMETER MIN
DEFAULT
MAX
NOTES
-
TIG WELDING CURRENT
10A
80A
250A