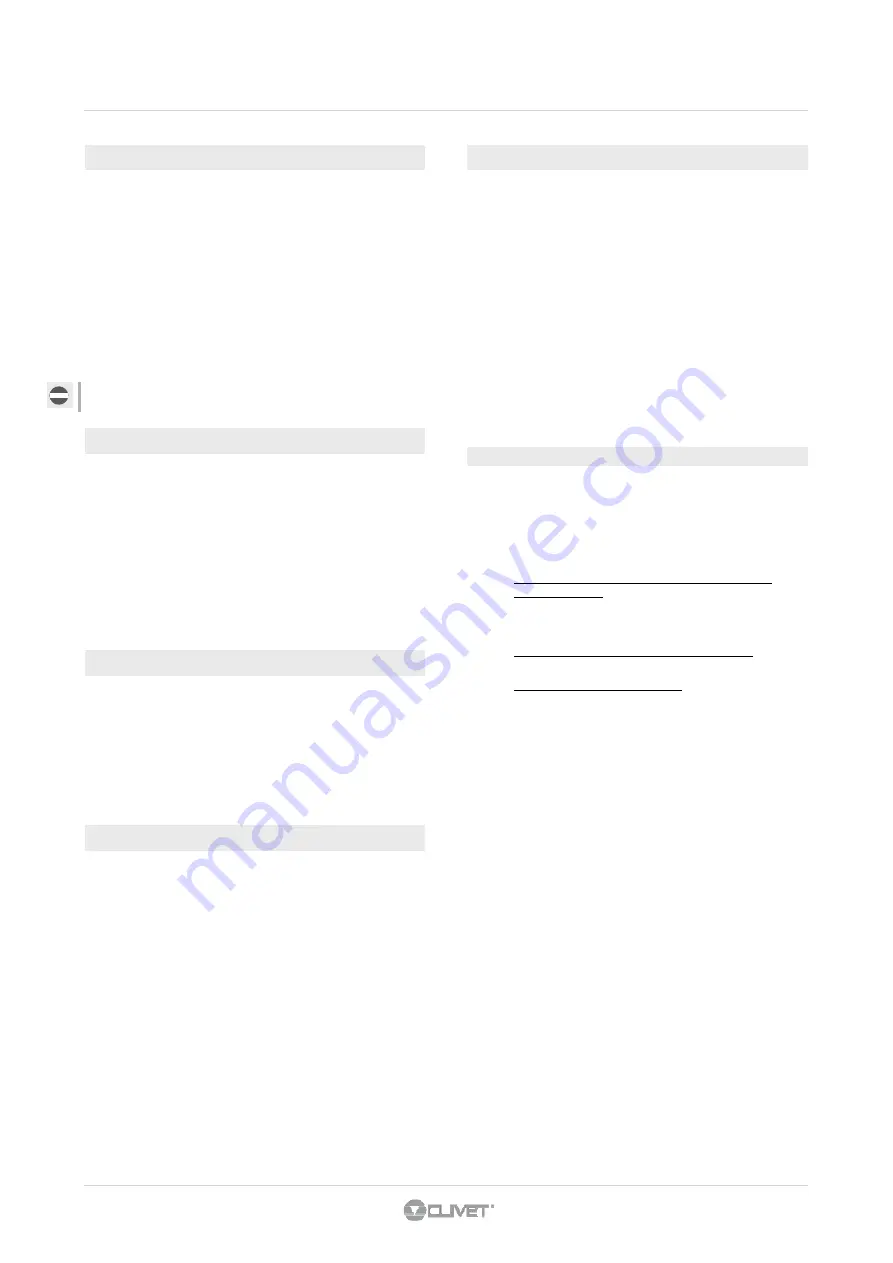
22
6 - START-UP
6.7 VOLTAGES
•
Check that the remote controls (ON-OFF etc) are
connected and, if necessary, enabled with the respective
parameters as indicated in the ELECTRICAL
CONNECTIONS section.
•
Check that probes and optional components are
connected and enabled with the respective parameters
(ELECTRICAL CONNECTIONS section and following
pages)
6.8 REMOTE CONTROLS
6.6 COMPRESSOR CRANKCASE RESISTANCES
Connect the oil resistances on the compressor crankcase at
least 8 hours before the compressor is to be starter :
•
at the first unit start-up
•
after each
prolonged period of inactivity
1. Supply the resistances switching off the unit isolator
switch.
2. To make sure that hte resistances are working, check the
power input .
3. At start-up the compressor crank-case temperature on the
lower side must be higher at least of 10°C than the outside
temperature.
Do not start the compressor with the crankcase oil below
operating temperature.
Check that the air and water temperatures are included in the
operating limits. Refer to “Control” section for the indications
on the control system.
Start-up the unit.
With operating unit, i.e. in stable conditions and next to the
operating ones, check:
•
supply voltage
•
total absorption of the unit
•
absorption of the single electric loads
6.10 START-UP REPORT
Identifying the operating objective conditions is useful to
control the unit over time.
With unit at steady state, i.e. in stable and close-to-work
conditions, identify the following data :
•
Total voltages and absorptions with unit at full load
•
Absorptions of the different electric loads (compressors,
fans, pumps etc)
•
Temperatures and flows of the different fluids (water, air)
both in input and in output from the unit
•
Temperature and pressures on the characteristic points of
the refrigerating circuit (compressor discharge, liquid,
intake)
The measurements must be kept and made available during
maintenance interventions.
6.11 CE 97/23 PED DIRECTIVE
6.9 OPERATING AT REDUCED LOAD
The units are equipped with partialization steps and they can,
therefore, operate with reduced loads.
However a constant and long operation with reduced
load with frequent stop and start-up of the compressor/s can
cause serious damages for the lack of oil return.
The above-described operating conditions must be
considered
OUT
of standards.
In the event of compressor break, due to the operating in the
above-mentioned conditions, the guarantee
WILL NOT BE
VALID
and Clivet spa declines any responsibility.
Check periodically the average operating times and the
frequency of the compressors starts: approximately the
minimum thermal load should be such as to need the
operating of a compressor for at least ten minutes.
If the average times are close to this limit, take the proper
corrective actions.
97/23 CE PED DIRECTIVE gives instructions for installers,
users and maintenance technicians as well. Refer to local
actuation norms
:
Briefly and as an example, see the following :
•
COMPULSORY VERIFICATION OF THE FIRST
INSTALLATION:
only for units assembled on the installer’s
building site (for ex. Condensing c direct
expansion unit)
•
CERTIFICATION OF SETTING IN SERVICE:
for all the units
•
PERIODICAL VERIFICATIONS:
to be executed with the frequency indicated by
the Manufacturer (see the MAINTENANCE
INSPECTIONS paragraph
Summary of Contents for WSH 100D
Page 9: ...9 4 WATER CONNECTIONS...
Page 12: ...12 WATER CONNECTIONS...
Page 14: ...14 5 ELECTRICAL CONNECTIONS 5 6 CONNECTIONS PERFORMER BY CUSTOMER...
Page 15: ...15 5 ELECTRICAL CONNECTIONS...
Page 16: ...16 5 ELECTRICAL CONNECTIONS...
Page 31: ...31 8 MAINTENANCE...
Page 46: ...46 NOTE...
Page 47: ...47...