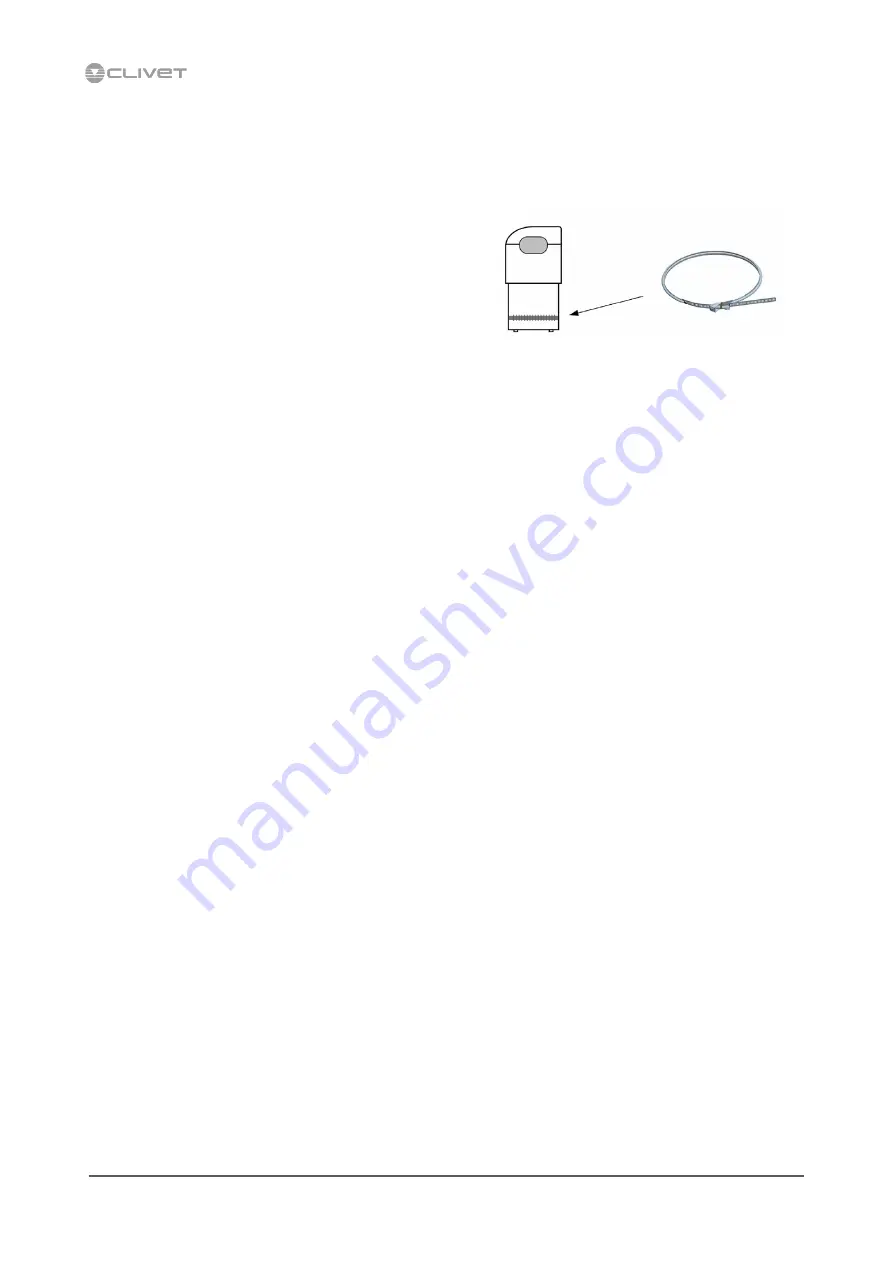
46
WSAN-XES 18.2-35.2
M0SM40N17-04
Unit booklet
It’s advisable to create a unit booklet to take notes of the
unit interventions.
In this way it will be easier to adequately note the various
interventions and aid any troubleshooting. Report on the
booklet:
date
intervention description
carried out measures etc.
Standby mode
if a long period of inactivity is foreseen::
turn off the power
avoid the risk of frost (empty the system or add glycol)
Turn off the power to avoid electrical risks or damages by
lightning strikes.
With lower temperatures keep heaters turned on in of the
electrical panel (option).
It’s recommended that the re-start after the stopping period
is performed by a qualified technician, especially after
seasonal stops or seasonal switching.
When restarting, refer to what is indicated in the “start-up”
section.
Schedule technical assistance in advance to avoid hitches
and to guarantee that the system can be used when
required.
System drain
1. empty the system
2. empty the exchanger, use all of the shut-off valves and
grub screws present
3. blow the exchanger with compressed air
4. dry the exchanger with hot air; for greater safety, fill
the exchanger with glycol solution
5. protect the exchanger from the air
6. take the drain caps off the pumps
Any anti-freeze liquid contained in the system should not
be discharged freely as it is a pollutant. It must be collected
and reused.
Before start-up, wash the system.
It is recommended to have a qualified technician start the
system after a period of inactivity, especially after seasonal
stops or for seasonal switch-over.
When starting, follow the instructions in the “start-up”
section.
Schedule technical assistance in advance to avoid hitches
and to guarantee that the system can be used when
required.
Compressor casing heater
Check:
closure
Operation
Summary of Contents for WSAN-XES 18.2
Page 7: ...7 WSAN XES 18 2 35 2 M0SM40N17 04 ...
Page 10: ...10 WSAN XES 18 2 35 2 M0SM40N17 04 Protection grilles Option PESM00007 PESM00008 ...
Page 18: ...18 WSAN XES 18 2 35 2 M0SM40N17 04 Connections by the Customer ...
Page 21: ...21 WSAN XES 18 2 35 2 M0SM40N17 04 UNITS IN MODULAR CONFIGURATION ...