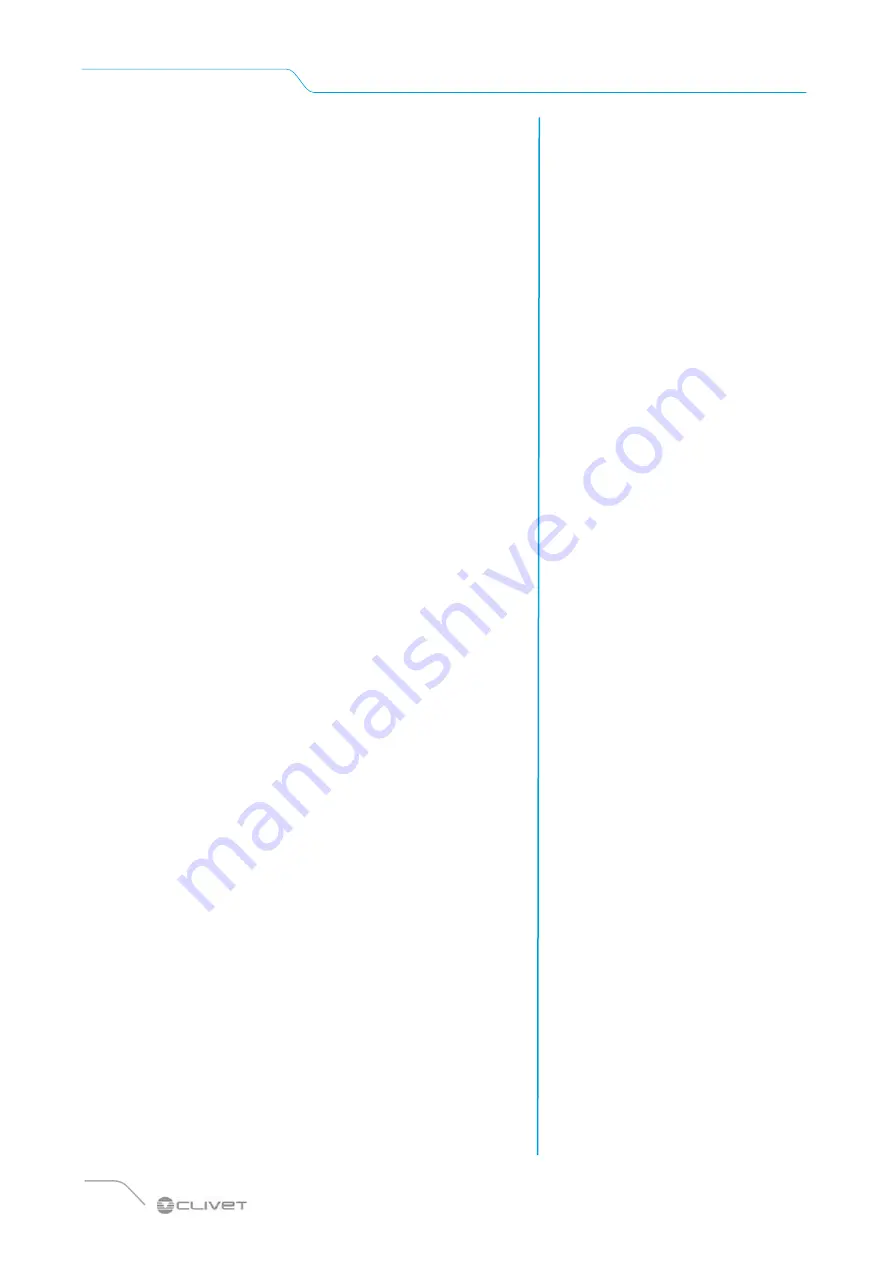
48
Compressor casing heater
Check:
x
closure
x
Operation
water side heat exchanger
The exchanger must to be able to provide the maximum thermal
exchange, therefore it is essential for the inner surfaces to be
clean of dirt and build-up.
Periodically check the difference between the temperature of the
supply water and the condensation temperature: if the difference
is greater than 8°C–10°C it is advisable to clean the exchanger.
The clearing must be effected:
x
with circulation opposite to the usual one
x
with a speed at least 1,5 times higher than the nominal one
x
with an appropriate product moderately acid (95% water +
5% phosphoric acid)
x
after the cleaning rinse with water to inhibit the action of any
residual product
Water filter
Check that no impurities prevent the correct passage of water.
Flow switch
x
controls the operations
x
remove incrustations from the palette
safety valve
The pressure relief valve must be replaced :
x
if it has intervened
x
if there is oxidation
x
based on the date of manufacture, in compliance with local
regulations.
circulation pumps
Check:
x
no leaks
x
Bearing status (anomalies are highlighted by abnormal noise
and vibration)
x
The closing of terminal covers and the correct positioning of
the cable glands.
Insulations
Check the condition of the insulations: if necessary, apply glue
and renew the seals.
8 MAINTENANCE
Summary of Contents for WDAT-iZ4
Page 1: ...R1234ze MANUAL FOR INSTALLATION USE AND MAINTENANCE WDAT iZ4 120 1 580 2 ...
Page 18: ...18 5 ELECTRICAL CONNECTIONS ...
Page 32: ...32 7 CONTROL ...
Page 33: ...33 7 CONTROL ...
Page 34: ...34 7 CONTROL ...
Page 35: ...35 7 CONTROL ...
Page 36: ...36 7 CONTROL ...
Page 37: ...37 7 CONTROL ...
Page 38: ...38 7 CONTROL ...
Page 39: ...39 7 CONTROL ...
Page 51: ...51 Compressor replacement 8 MAINTENANCE ...
Page 53: ...53 9 ANTIVIBRATION MOUNTS ...
Page 54: ...54 9 ANTIVIBRATION MOUNTS ...
Page 71: ......