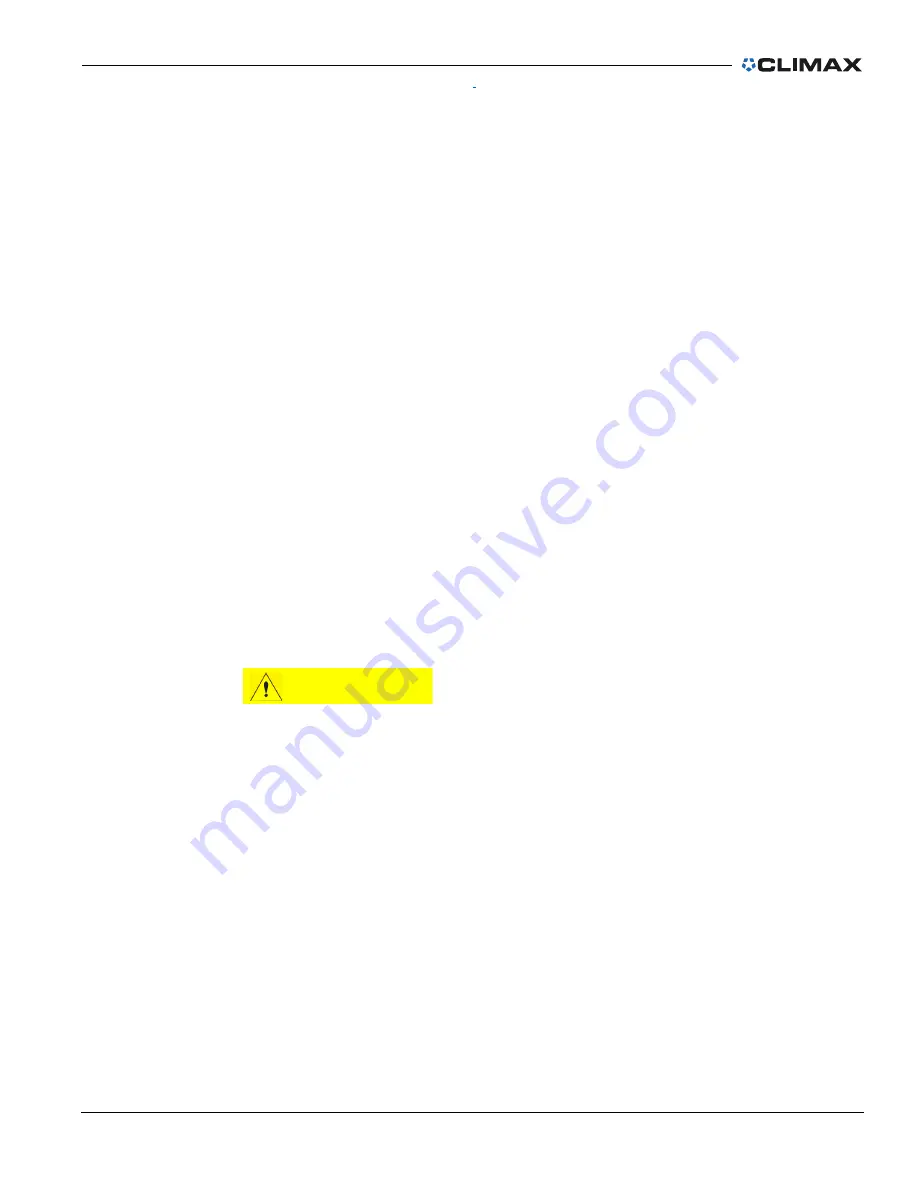
P/N 80679, Rev. 10
Page 43
T
IP
:
The surface mount circular mounting plate can be used as a template to
hold the four blocks in the correct orientation while attaching the blocks to
the workpiece.
Check that the blocks are secured to the mounting plate with approximately 0.2"
(5 mm) of adjustment range. Secure the blocks to the workpiece with the circular
mounting plate centered to the area to be machined, within the same true position [0.2"
(5mm)].
3.8.3
Centering and leveling the surface mount assembly
Do the following to center and level the surface mount assembly:
1. After securely attaching the machine to the flange, mount a dial indicator on
the turning arm.
2. Check that power to the machine drive is isolated and locked out.
3. Using the dial indicator, indicate the workpiece surface for level while
manually rotating the machine.
•
To manually rotate the pneumatic machine, insert a 10-mm hex wrench in
the hex opposite the motor or push on the end of the turning arm.
•
To manually rotate the hydraulic machine, use the cross-connection hose
supplied with the machine to connect the #1 and #2 port hoses. Insert a 10-
mm hex wrench in the hex opposite the motor or push on the end of the
turning arm.
CAUTION
If you used the 10-mm hex wrench, remove it from the hex opposite the
motor. Otherwise, damage to the machine may occur.
4. Adjust the level of the machine using the two M16 adjustment screws in each
quadrant of the mounting plate (Figure 3-25).
5. Reposition the dial indicator to check machine centering.
6. Center the machine using the M16 set screw in the edge of each block.
7. Repeat step 3 to step 6 until the machine is aligned.
8. Secure the M10 screws to lock the position of the surface mount.
Summary of Contents for FF6300
Page 2: ......
Page 4: ...Page B FF6300 Operating Manual CLIMAX GLOBAL LOCATIONS...
Page 5: ...P N 80679 Rev 10 Page C CE DOCUMENTATION...
Page 10: ...Page iv FF6300 Operating Manual This page intentionally left blank...
Page 14: ...Page viii FF6300 Operating Manual This page intentionally left blank...
Page 16: ...Page x FF6300 Operating Manual This page intentionally left blank...
Page 21: ...P N 80679 Rev 10 Page 5 This page intentionally left blank...
Page 28: ...Page 12 FF6300 Operating Manual This page intentionally left blank...
Page 31: ...P N 80679 Rev 10 Page 15 2 1 1 ID chuck assembly FIGURE 2 1 ID CHUCK ASSEMBLY...
Page 33: ...P N 80679 Rev 10 Page 17 2 1 3 OD mount assembly FIGURE 2 3 OD MOUNT ASSEMBLY...
Page 40: ...Page 24 FF6300 Operating Manual This page intentionally left blank...
Page 71: ...P N 80679 Rev 10 Page 55 FIGURE 3 44 BACKFACING ATTACHMENT DIMENSIONS...
Page 72: ...Page 56 FF6300 Operating Manual This page intentionally left blank...
Page 88: ...Page 72 FF6300 Operating Manual This page intentionally left blank...
Page 90: ...Page 74 FF6300 Operating Manual FIGURE 6 1 FF6300 IN CONTAINERS STEEL CONTAINER WOODEN CRATE...
Page 92: ...Page 76 FF6300 Operating Manual FIGURE 6 3 PACKING THE FF6300 WITH OD MOUNT...
Page 94: ...Page 78 FF6300 Operating Manual This page intentionally left blank...
Page 99: ...P N 80679 Rev 10 Page 83 This page intentionally left blank...
Page 126: ...Page 110 FF6300 Operating Manual This page intentionally left blank...
Page 129: ...P N 80679 Rev 10 Page 113 APPENDIX C SDS Contact CLIMAX for the current Safety Data Sheets...
Page 130: ...Page 114 FF6300 Operating Manual This page intentionally left blank...
Page 131: ......
Page 132: ......