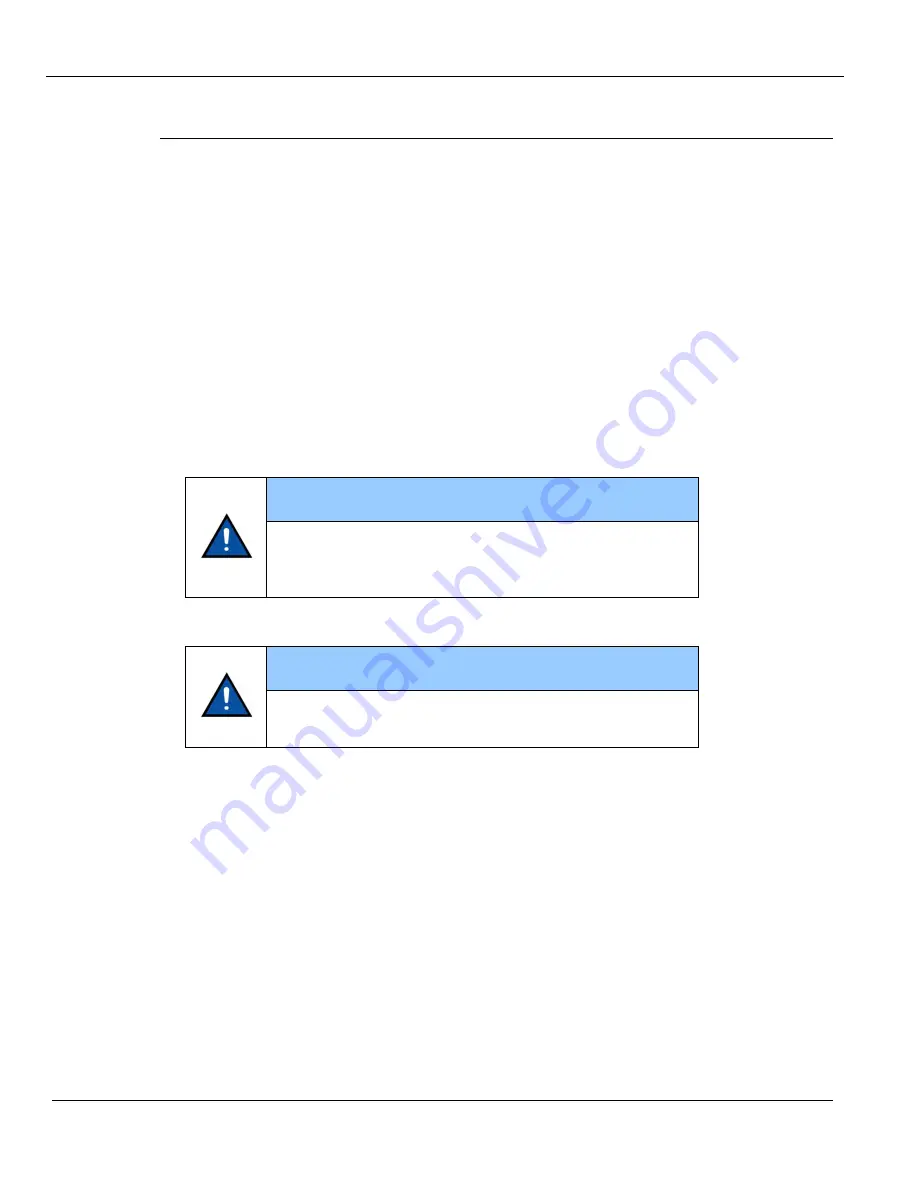
Page 32
BB5500 Operating Manual
Setting up the tool holder
The 5/16” square bit holder accepts high speed steel, solid carbide or brazed carbide tool
bits. The cartridge holder is designed for the sizes 2 and 3 Microbore cartridges and uses
supplied replaceable carbide inserts.
The cartridge holder is designed for the size 2 and 3 cartridges and uses supplied
replaceable carbide inserts.
Tooling made of high speed steel is recommended for roughing bores. High speed steel
cuts more freely and causes less bar deflection for large depth of cut. Carbide has superior
wear characteristics and is recommended for light finish passes.
Although the tool holder can be installed so the cutting surface faces either the RDU or the
feed end of the bar, always insert the tool holder so it is correctly positioned for clock-wise
bar rotation, as shown below. If needed, simply remove the tool holder and rotate the
locating key 180 degrees.
Gib Adjustment
Turn the center screw counterclockwise to tighten.
IMPORTANT
Always place the tool holder completely in the
pocket of the tool slide and secure with the two
setscrews provided in the tool slide.
IMPORTANT
Excessive clearance in the tool slide can affect final
finish and tolerance of the bore.
Summary of Contents for BB5500
Page 2: ......
Page 13: ...P N 29327 Rev 3 Page 11 Climax BB5500 Components...
Page 48: ...Page 46 BB5500 Operating Manual...
Page 50: ...Page 48 BB5500 Operating Manual Figure 5 27285 28765 Bar Boring 2 1 2 Dia...
Page 51: ...P N 29327 Rev 3 Page 49...
Page 52: ...Page 50 BB5500 Operating Manual...
Page 53: ...P N 29327 Rev 3 Page 51...
Page 54: ...Page 52 BB5500 Operating Manual...
Page 55: ...P N 29327 Rev 3 Page 53...
Page 56: ...Page 54 BB5500 Operating Manual...
Page 57: ...P N 29327 Rev 3 Page 55...
Page 58: ...Page 56 BB5500 Operating Manual...
Page 59: ...P N 29327 Rev 3 Page 57...
Page 60: ...Page 58 BB5500 Operating Manual...
Page 61: ...P N 29327 Rev 3 Page 59...
Page 62: ...Page 60 BB5500 Operating Manual...
Page 63: ......
Page 64: ......