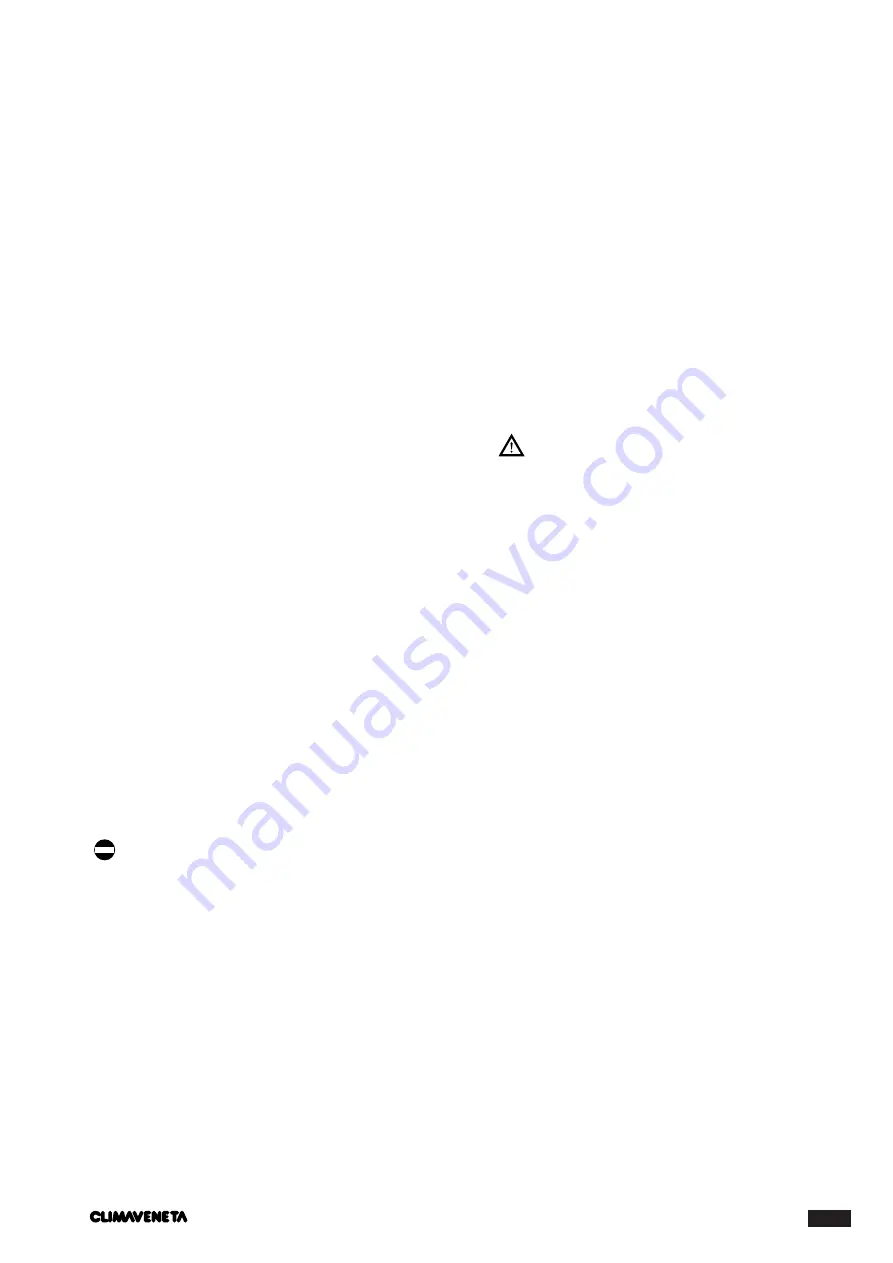
HRAT E - HRAT/HRAN
11
English 09/02
ELECTRICAL POWER CONNECTIONS
For the functional connection of the unit, bring the power
supply cable to the electrical panel inside the unit and con-
nect it to terminals U-N and PE, respecting the (U) phase,
(N) neutral and (PE) earth in the case of single phase units
(230V~50Hz), and U-V-W phases, N neutral and PE earth
in three phase units (400V-3N~50Hz).
AUXILIARY CONNECTIONS
All terminals referred to in the explanations below are to
be found on the terminal board inside the electrical panel
and described as “installer terminals”.
REMOTE START UP AND SHUT DOWN
To fit a remote on/off device, the jumper must be replaced
with a switch connected to terminals 6 and 7 of the
installer terminal board. For timed operation, connect a
daily or weekly timer between terminals 6 and 7.
REMOTE HEATING/COOLING CONTROL
To fit a remote heating/cooling switching device, the
jumper must be replaced with a switch connected to ter-
minals 8 and 9 of the installer terminal board.To install the
kit, proceed as follows:
- Select the parameter H27 on the HSW4 control panel
and set the value to 2.
REMOTE ALARM
For remote display of unit shut-down due to malfunction,
an audible or visual alarm warning device can be connected
between terminals 10 and 11. Connect the phase to termi-
nal 11 and the alarm warning device between terminal 10
and neutral (max. load: 500mA at 24V).
It is prohibited
to earth the secondary of the 24V
transformer, as the chiller is compliant to the stan-
dards in force in the country concerned.
REMOTE KEYBOARD KIT
The remote keyboard kit can be used to display all unit func-
tions and access the parameters of the electronic board
from a point located at some distance from the unit itself.
It consists of a remote control module and a transformer.
To install the kit, proceed as follows:
- disconnect the power supply by means of the QS1 door
lock disconnecting switch then access the inside of the
electrical panel.
- connect the remote control module with 3 wires to ter-
minals 18, 19 and 20 on the installer terminal board.
terminal 18 connected to terminal 26 on the module;
terminal 19 connected to terminal 24 on the module;
terminal 20 connected to terminal 25 on the module;
Make sure that parameter H27 is set to 0.
To avoid interference due to magnetic fields,
the use of shielded cable is recommended. The
cable should not be more than 100m long.
CONNECTING A PUMP
If a pump is to be fitted to the unit or storage tank, it
should be connected to terminals 16, 17 and earth on the
installer terminal board.
CONNECTING A FLOW SWITCH
If a flow switch is used, connect it to terminals 14 and 15
on the installer terminal board after removing the jumper.