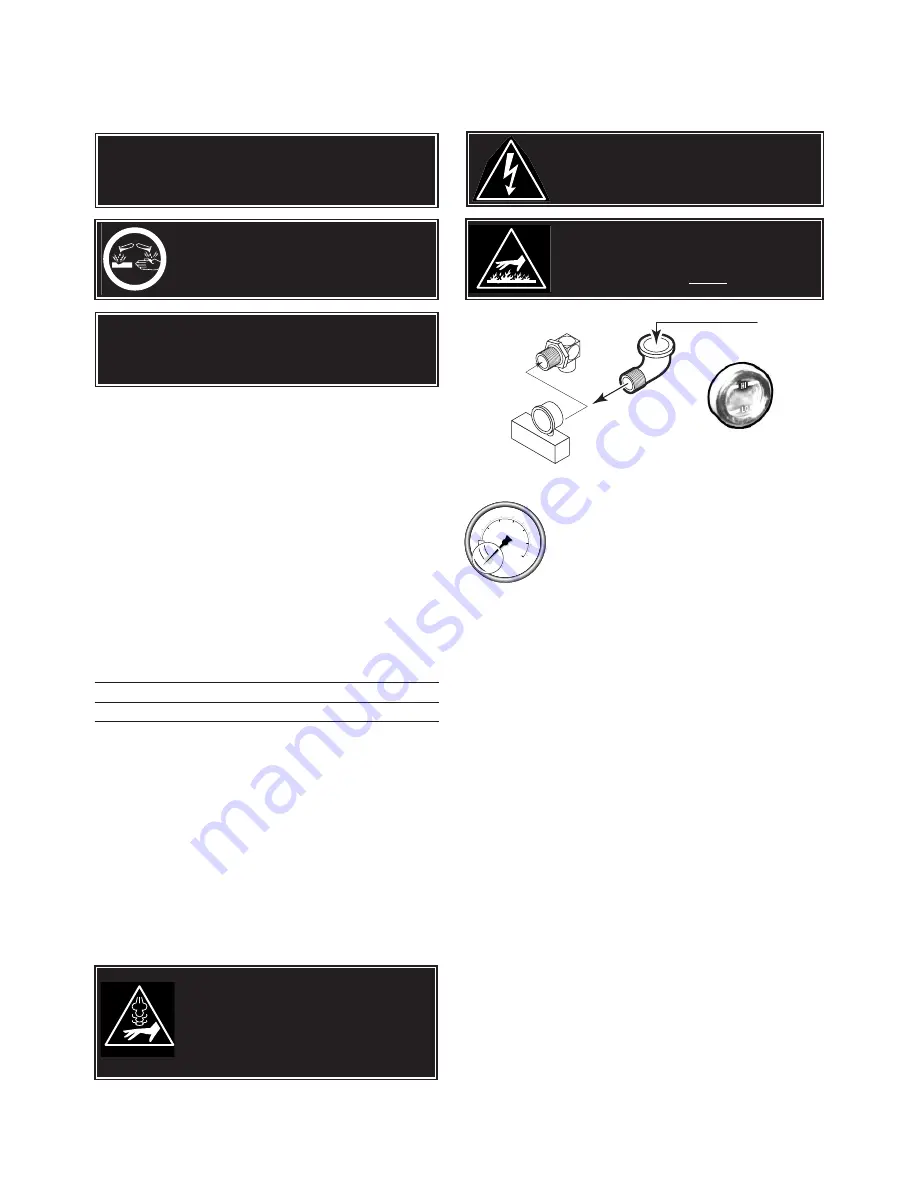
KETTLE JACKET CLEANOUT AND PASSIVATION PROCEDURES
The following procedure should be preformed at least once every three years to prevent possible corrosion
and ensure the optimum life of the kettle.
DESCRIPTION
- Molyfilm 315 inhibits corrosion in
stainless steel and copper. A pH buffer is present to
assist in maintaining the appropriate pH to assist in
corrosion inhibition.
DISPOSAL
- Follow all Federal, State and local codes
when disposing of product.
SHELF LIFE
- Molyfilm 315’s effectiveness will
diminish after three years.
REFILL QUANTITIES
(ORDERING INFO: 1 Liter
Molyfilm 315 Rust Inhibitor - Part# KE600340-1)
IIM
MP
PO
OR
RT
TA
AN
NT
T: To ensure satisfactory mixing follow the
MIXING / FILLING PROCEDURE described below.
Kettle Size
Volume of Water
Volume of Molyfilm 315
U.S. Gal. Liters
oz.
cc (ml.)
25 U.S. Gal.
4.4
16.6
6
176
MIXING / FILLING PROCEDURE
1.
Refer to chart to determine the required volumes of
water and Molyfilm 315.
2.
In a separate container mix 1/2 gallon of the required
volume of water with the total required volume of
Molyfilm 315.
3.
Pour mixture into kettle.
4.
Pour the remaining required volume of water into kettle.
WARNING:
IMPROPER REFILLING OF KETTLE JACKET WILL
RESULT IN IRREVERSIBLE DAMAGE TO UNIT
.
DANGER:
MOLYFILM 315 IS CORROSIVE, AVOID
CONTACT WITH SKIN AND EYES.
DANGER:
AVOID INHALATION - VAPORS FROM
MOLYFILM 315 MAY BE HARMFUL OR FATAL.
DANGER:
PRESSURE RELIEF VALVE WILL
EXHAUST HIGH TEMPERATURE STEAM.
CONTACT WITH SKIN COULD RESULT IN
SERIOUS BURNS. KEEP FACE, HANDS
AND BODY CLEAR OF DISCHARGE
.
DANGER:
WORKING ON MACHINES WITH
POWER COULD RESULT IN SEVERE
ELECTRICAL SHOCK.
DANGER:
EXTREMELY HOT SURFACES.
WORK ONLY ON COLD KETTLE.
Flushing Procedure
1.
Ensure kettle is at room temperature and
pressure gauge showing zero or less
pressure.
2.
Shut off and disconnect gas supply.
3.
Remove electrical plug from power source.
4.
Remove bolts holding kettle to tabletop/floor.
5.
Pull ring on pressure relief valve to insure there
is no pressure within the kettle jacket.
6.
Remove pressure relief valve.
7.
Replace pressure relief valve with street elbow.
8.
Remove sight glass.
9.
Tilt kettle on its side (sight glass down) and allow to
drain. Flush out as much debris as possible with water.
10.
Tilt kettle upright, apply a thread sealant (i.e. Teflon
tape) to the sight glass threads and replace.
11.
Fill jacket via the street elbow with a mixture of water
and Molyfilm 315 (see REFILL QUANTITIES).
12.
Remove street elbow.
13.
Apply a thread sealant (i.e. Teflon tape) to the pressure
relief valve and replace.
14.
Reconnect gas and electrical supplies.
15.
Turn kettle on, vent and heat to high for 1/2 hour.
16.
Cool and drain kettle as per above procedure.
Refilling Unit
1.
Apply a thread sealant (i.e. Teflon tape) to the sight
glass threads and replace.
2.
Fill kettle jacket with a mixture of water and Molyfilm
315 (see REFILL QUANTITIES charts).
3.
Apply a thread sealant (i.e. Teflon tape) to the filler
plug threads and replace.
4.
Turn kettle on and check for leaks at sight glass and
filler plug. See Vacuum Leak Test.
5.
Vent kettle. See Kettle Venting Instructions for proper
procedure.
50
0
100
150
200
250
300
350
400
40
50
60
0
10
20
30
psi
kPa
V
EN
T
A
IR
Remove
Pressure
Relief
Valve
Attach
Street
Elbow
Fill unit via Street Elbow
Important
-
Pull pressure relief valve
ring open to insure vessel
is not pressurized.
Sight
Glass