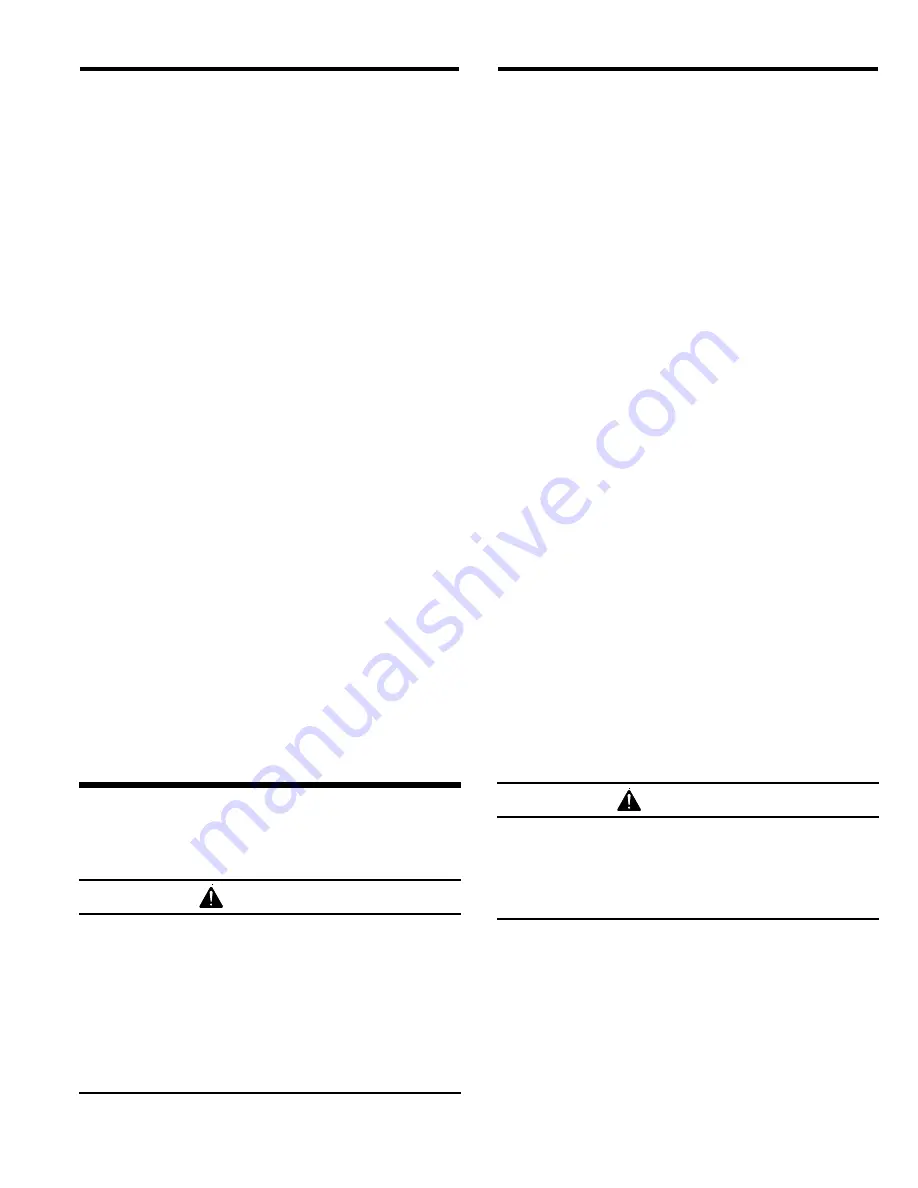
TLR-50 PNEUMATIC REMOTE CONTROLS
Page 6
5.1
Inlet Valve, Ref. Figure 5
4.1.2
While blasting, inspect the following:
5.1.1
All service on the inlet valve must be done with
the air off and the air supply locked-out and tagged-out.
•
Check the control handle for leaks.
4.2 Weekly
5.1.2
Use snap-ring pliers to remove the top and
bottom retaining rings.
4.2.1
Inspect the following while blasting.
5.1.3
To remove the top cap, twist the petcock/cross
assembly while pulling up.
•
Inspect all control hoses, and valves for leaks. If
leaks are found, stop blasting and repair.
5.1.4
Pull down on the bottom plug to remove it. If
necessary, use pliers to grab the wrench flats to remove
it from the body. Cup the bottom opening to catch the
spring, retainer, and washer as the plug is removed.
4.3 Periodic
Inspection
NOTE: Periodic inspection of the following items will
help avoid unscheduled down-time.
5.1.5
If the piston cannot be removed with finger or
thumb force, use a dowel or similar object inserted
through the bottom opening to push the piston assembly
out the top.
4.3.1
The remote control system is a safety device. To
be safe and to avoid unscheduled down-time, the
internal parts of the inlet valve and outlet valve should
be inspected periodically. Inspect them for wear and
lubrication of O-rings, pistons, springs, seals, and
castings. See Service Maintenance in Section 5.
5.1.6
Clean all parts and inspect for wear as follows:
•
The spring is approximately 1" long. If it is rusted or
compressed, replace it.
4.3.2
The control handle is the actuator of the remote
control system. Periodically clean around the springs,
handle lever, and safety lever lock to ensure that the unit
is free of abrasive and debris that could cause the
handle lever or safety lever lock to bind. See the RLX
Owners Manual for service instructions.
•
Inspect the piston, rubber washer, washer retainer
top cap and bottom plug for damage. Replace all
damaged parts.
•
Look into the bottom opening in the valve body. If
the machined seat is worn, replace the body.
4.4 Lubrication
•
Inspect all O-rings. If any are damaged or flattened,
replace them.
4.4.1
Once per week, while the air is off, put one or
two drops of lightweight machine oil in the inlet valve
through the safety petcock. This lubricates the piston
and O-rings in the inlet and outlet valves.
5.1.7
Remove the lower twinline hose connection, and
remove the orifice fitting for inspection. Clean the 1/16
″
orifice and reassemble the connection.
WARNING
The orifice fitting must not be removed,
modified, or substituted with another fitting.
Altering the orifice fitting may cause involuntary
activation of the blast machine or some other
malfunction which could result in serious injury.
5.0 SERVICE
MAINTENANCE
WARNING
Failure to observe the following before
performing any maintenance could cause
serious injury or death from the sudden release
of compressed air.
5.1.8
Lubricate all O-rings, and use the illustration in
Figure 5, to reassemble the valve in reverse order,
assembling the top end first.
•
Depressurize the blast machine.
5.2
Diaphragm Outlet Valve, Ref. Figure 4
•
Lock out and tag out the compressed air
supply.
5.2.1
All service on the outlet valve must be done with
the air off and the air supply locked-out and tagged-out.
•
Bleed the air supply line to the blast
machine.