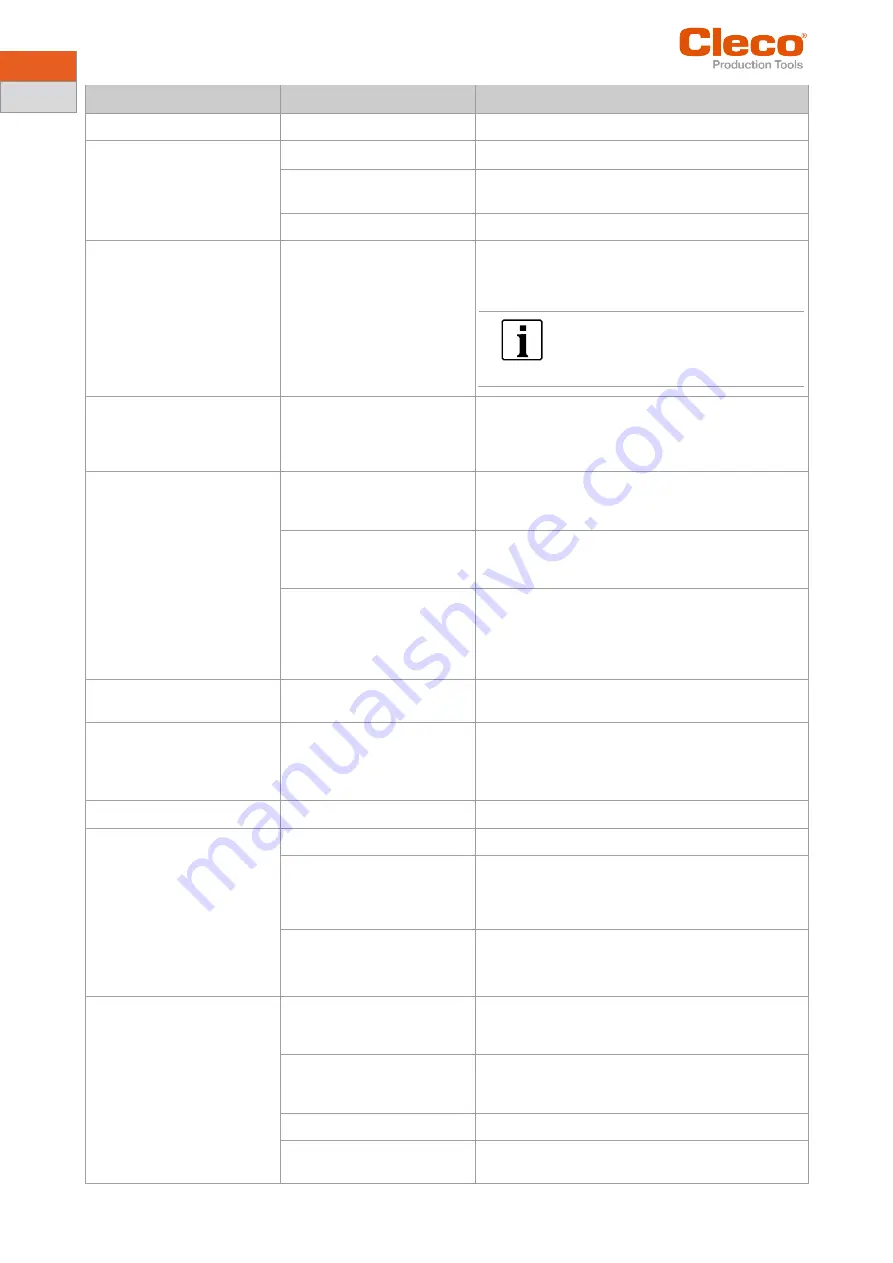
1
EN
12
P2547BA | 2021-07
Apex Tool Group
Problem
Possible causes
Measure
Battery voltage is too low.
►
Change battery.
Tool not recognized.
Software is incorrect.
►
Check
CellClutch
laptop/PC software.
Connection to laptop/PC is not
available.
►
Check USB cable.
►
Check PC driver.
Tool is defective.
►
Change tool.
Tool starts in tightening direc-
tion, but not in counterclock-
wise rotation.
No speed programmed for
counterclockwise rotation.
►
Program the counterclockwise rotation: In the
CellClutch
PC software, set the
Rotation
to
Reverse
in the
Forward and Reverse Application
Settings
and parameterize the
Speed
.
If
Forward
is selected for
Enabled Direction
, the
counterclockwise rotation of the
reverse switch has no function.
Tool does not start with coun-
terclockwise rotation activated.
With counterclockwise rotation,
parameter for Speed is 0 rpm.
►
Program the speed for counterclockwise rotation:
In the
CellClutch
PC software, set the
Speed
and
Rotation
in the
Forward and Reverse Appli-
cation Settings
.
Tool shuts off prematurely.
Operator releases start trigger
before the controller stops the
tool.
►
Make sure that the operator keeps the start trig-
ger pressed throughout the entire sequence.
The fastening time exceeds
the standard time of 10 sec-
onds.
►
Increase the fastening time.
Tool exceeds the angle set-
point.
►
Check the fastening sequence to ensure that the
torque shutoff value and/or angle setpoint are
correct. Adjust as necessary.
►
Check whether the fastening joint has changed
significantly.
Tool does not change speed. Speed is the same in all
stages.
►
Make sure that the speed in the stages is correct.
Status/work light is disabled.
Disabled by parameter set-
tings.
►
Parameterize the work light: In the
CellClutch
PC software, select
Bright
or
Dim
for
Work Light
.
►
Parameterize the status light: In the
CellClutch
PC software, select
Bright
or
Dim
for
Status Light
.
No-load speed not reached.
Battery voltage is too low.
►
Use a fully charged battery.
Expected number of test run-
downs is not achieved with one
charge of the battery.
Battery is not fully charged.
►
Use a fully charged battery.
High torque is needed during a
fastening sequence, e.g. for
coated fastenings.
If a high torque is needed for a longer period, e.g. for
several turns, the number of rundowns that can be
achieved with one battery charge will be significantly
reduces.
Battery is at end of life.
After 800 charging cycles, the capacity is reduced to
approx. 60%.
►
Use new battery.
Encoder is defective.
►
Press start switch. If the status light continues to
flash, send the tool to a
Sales & Service Center
for repair.
Tool temperature is too high.
►
Allow the tool to cool down. The current rundown
can be terminated, but a new one cannot be
started.
Battery voltage is too low.
►
Change battery.
Warning that the next mainte-
nance is due.
►
Send the tool to a
Sales & Service Center
for
maintenance.