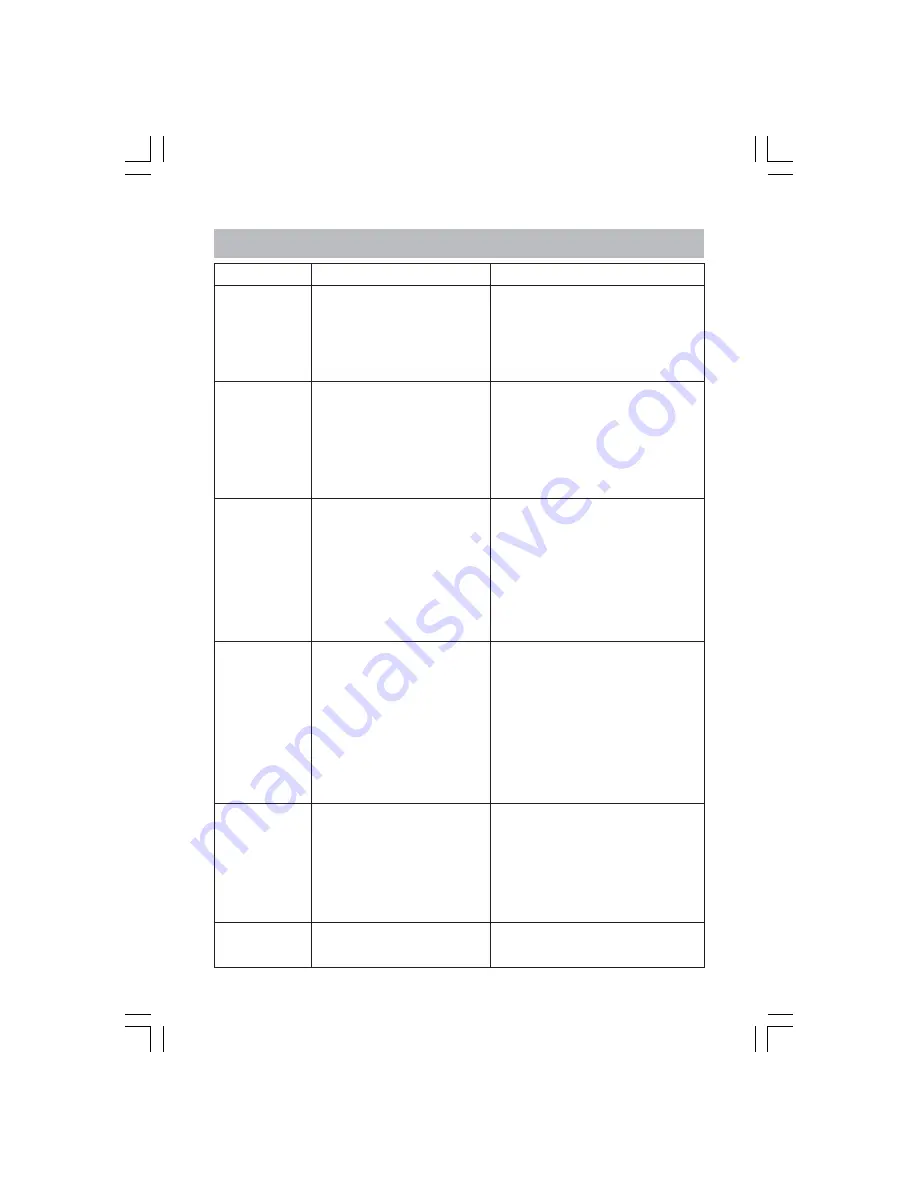
TROUBLE SHOOTING
PROBLEM
A) Incorrect belt tension
B) Dry spindle
C) Loose pulley
D) Worn bearing
A) Adjust tension
B) Remove spindle/quill assembly
and lubricate
C) Tighten pulley
D) Replace bearing
PROBABLE CAUSE
REMEDY
A) Needs lubrication
B) Table lock tightened
A) Lubricate with light oil
B) Loosen clamp
Noisy
operation
(under load)
Table difficult to
raise
Excessive
drill wobble
A) Loose chuck
B) Worn spindle, or bearing
C) Worn chuck
D) Bent drill
A) Tighten by pressing chuck down
on to a block of wood against the
table.
B) Replace spindle shaft or bearing
C) Replace chuck
D) Renew Drill
Motor won’t
start
A) Power supply
B) Motor connection
C) NVR Switch connections
D) Faulty switch
E) Motor windings burned
F) Pulley Cover not closed
G) Micro Switch inoperative
A) Check power cord/fuse
B) Check motor connections
C) Check switch connections
D) Replace switch
E) Replace motor
F)
Close pulley cover.
G) Check operation of micro switch,
See P10 - and renew if faulty
Drill binds
in workpiece
A) Excessive feed pressure
B) Loose belt
C) Loose drill
D) Incorrect drill speed.
E) Drill profile incorrect for
type of material
A) Apply less pressure
B) Check belt tension
C) Tighten drill with key
D) Refer to Cutting Speed chart,
and adjust drill speed accordingly
E) Consult an appropriate manual
re. Materials, Drills and Cutting
Angles, and sharpen drill
accordingly.
Drill burns
or smokes
A) Incorrect speed.
B) Chips are not discharging
C) Dull drill or incorrect profile
for material
D) Lack of coolant
E) Excessive feed pressure
A) Refer to Cutting Speed chart,
and adjust drill speed accordingly
B) Clean drill
C) As ‘E’ above
D) Use coolant whilst drilling
E) Apply less pressure
16
Summary of Contents for METALWORKER CDP201B
Page 1: ...0307 SERIAL No ...
Page 18: ...HEAD ASSEMBLY 18 ...