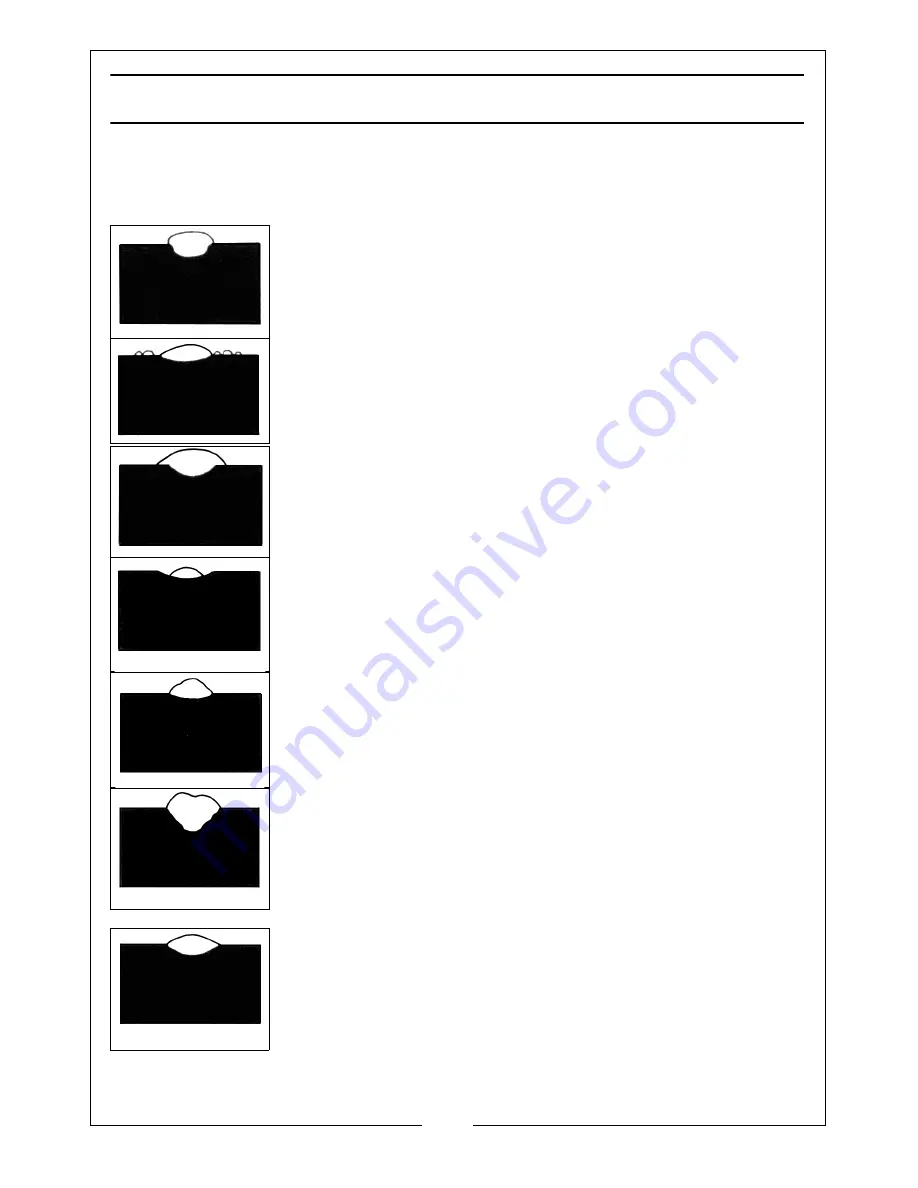
11
Parts & Service: 020 8988 7400 / E-mail: [email protected] or [email protected]
WELDING PITFALLS
The arc welding technique is an acquired skill and requires considerable
practice before perfect results are obtained. The diagrams below will help to
explain the pitfalls in your technique and how to overcome them.
ARC TOO SHORT
This causes irregular masses of weld to be deposited, with
slag contamination on an uneven surface.
ARC TOO LONG
This causes poor penetration resulting in a weak weld with
excessive spatter and porosity. Surface of the weld is rough
and the arc makes a hissing sound
ELECTRODE MOVED TOO SLOWLY
This causes a very wide and heavy deposit which overlaps
at the sides. It is wasteful both in terms of time and electrode
use.
ELECTRODE MOVED TOO QUICKLY
This causes poor penetration with a ‘stringy’ and incomplete
weld deposit. Slag is very hard to remove.
CURRENT TOO LOW
This causes poor penetration and causes the electrode to
stick to the workpiece too readily. Also results in a very
irregular and high weld deposit. Slag is very hard to remove.
CURRENT TOO HIGH
This causes excessive penetration with spatter and deep
pointed crater. It may also cause holes to be burned in the
workpiece.
Burns electrodes very quickly.
THE PERFECT WELD
With the correct combination of arc length, current
regulation, inclination and speed of the electrode, you will,
with practice, produce the perfect weld.
This should be regular with uniform ripples and no slag
contamination. The arc will make a steady crackling sound.
Summary of Contents for EASIARC 165
Page 16: ......