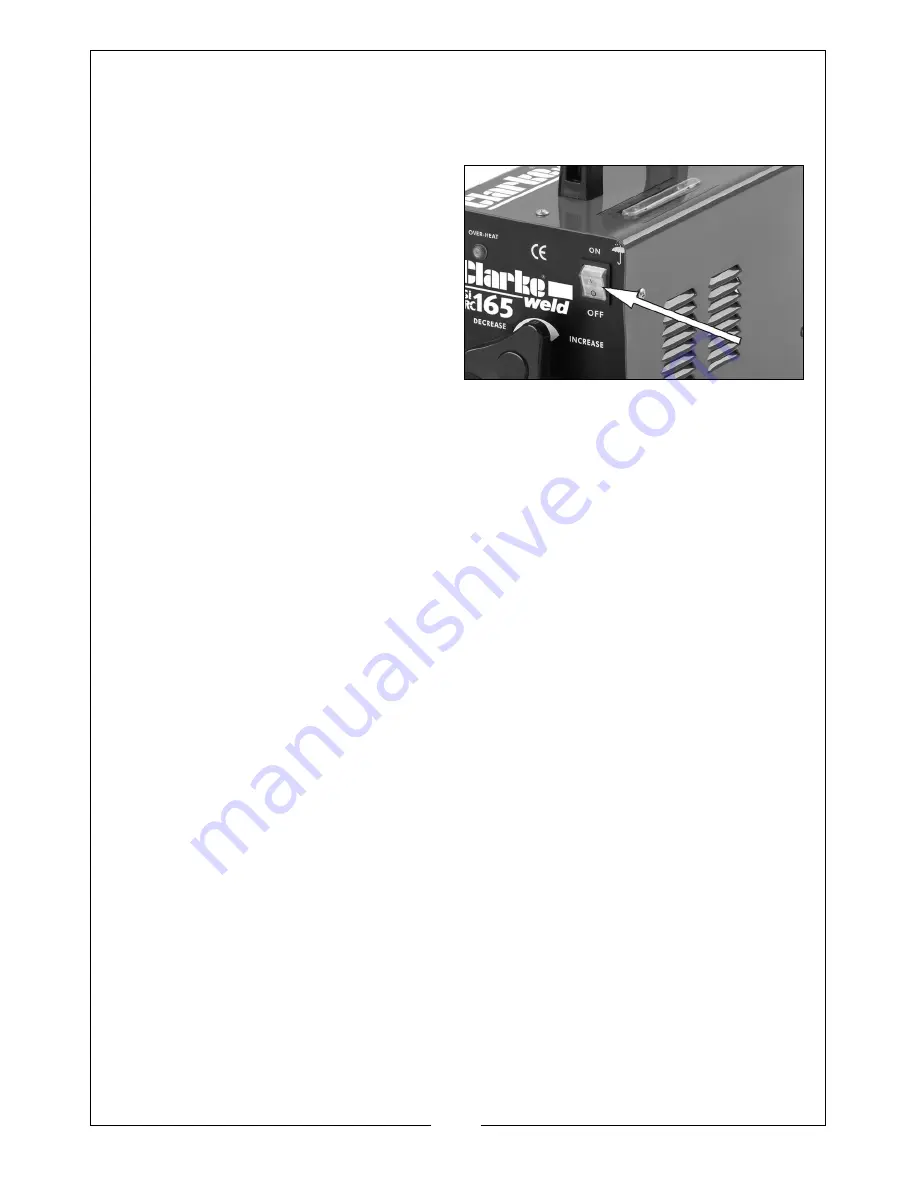
10
Parts & Service: 020 8988 7400 / E-mail: [email protected] or [email protected]
STRIKING AN ARC
IMPORTANT: BEFORE YOU STRIKE AN ARC, ALWAYS BRING THE FACE SHIELD UP
TO PROTECT YOUR EYES.
1. Switch ON the machine.
2. Line up the electrode exactly over
the spot where you want to strike.
3. Position your shield in front of your
face and tap the electrode down
firmly. Once you tap down and
contact is made, you must
instantly raise the electrode to the
required arc gap.
• The arc gap should be roughly the same as the diameter of the
electrode.
• If you withdraw the electrode too far once the arc is struck, you will
lose the arc and have to try again.
NOTE:
One thing that usually happens when you are striking an arc is that the
electrode sticks to the work. It should come unstuck with a sharp tug. If
it will not free easily, turn off the welder immediately as it will quickly
overheat, then give the join a tap from the chipping hammer. As you
get more experienced, this will happen less.
4. Once the arc is struck, move the electrode along its intended path,
keeping the tip in the molten pool at all times.
• You must also get used to feeding down the electrode steadily as it
burns away.
• An even crackling noise should be heard, which is an indication of a
good weld.
5. Inspect the job carefully, the area of weld should be a complete fusion of
the electrode and parent metal(s).
• Any slag which forms on the surface should be chipped away with
the hammer/brush supplied.
• If the resultant weld looks messy and irregular, this is an indication of
porosity or slag contamination, and you have almost certainly failed
to achieve the correct combination of speed and current. This is a
common problem, so do not worry as practice will quickly cure this.
Summary of Contents for EASIARC 165
Page 16: ......