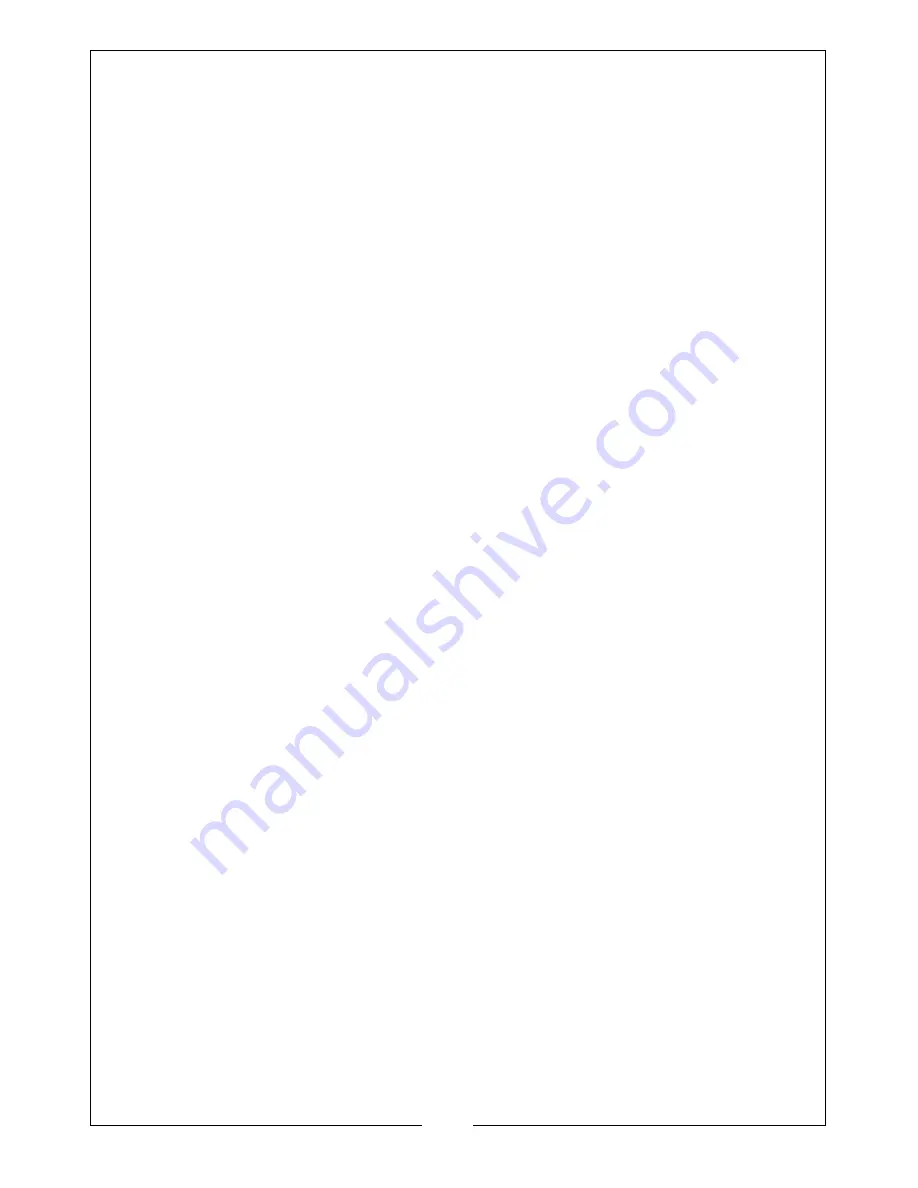
5
Parts & Service: 020 8988 7400 / E-mail: [email protected] or [email protected]
7.
Always use the tool attachments to steady the workpiece. If the tool attachments
are not used, the torque of the spinning grinding/polishing wheel may pull the
workpiece from your hands.
8.
Never leave the grinder unattended when it is connected to an electrical power
supply. Switch off the machine and unplug it before leaving.
9.
ALWAYS check for damaged parts. Before further use of the tool, a guard or other
part that is damaged should be carefully checked to determine if it would operate
properly and perform its intended function. Check for misalignment or binding of
moving parts, breakage of parts and any other condition that may affect the tool's
operation. A part that is damaged should be properly repaired or replaced at an
authorised Service Center. Following this rule will reduce the risk of electric shock, fire
or serious injury.
10. Gloves, manufactured to the current European safety standards should be worn
when operating grinding equipment.
11. Eye protection manufactured to the current European safety standards should be
worn when operating grinding equipment.
Note: Bench grinders used in industrial environments may be subject to the
requirements of The Provision and Use of Work Equipment regulations 1992
(particularly regarding the training requirement of The Abrasive Wheels
Regulations 1970), or other legislation. If in doubt seek advice.
Please keep these instructions in a safe place for future reference.