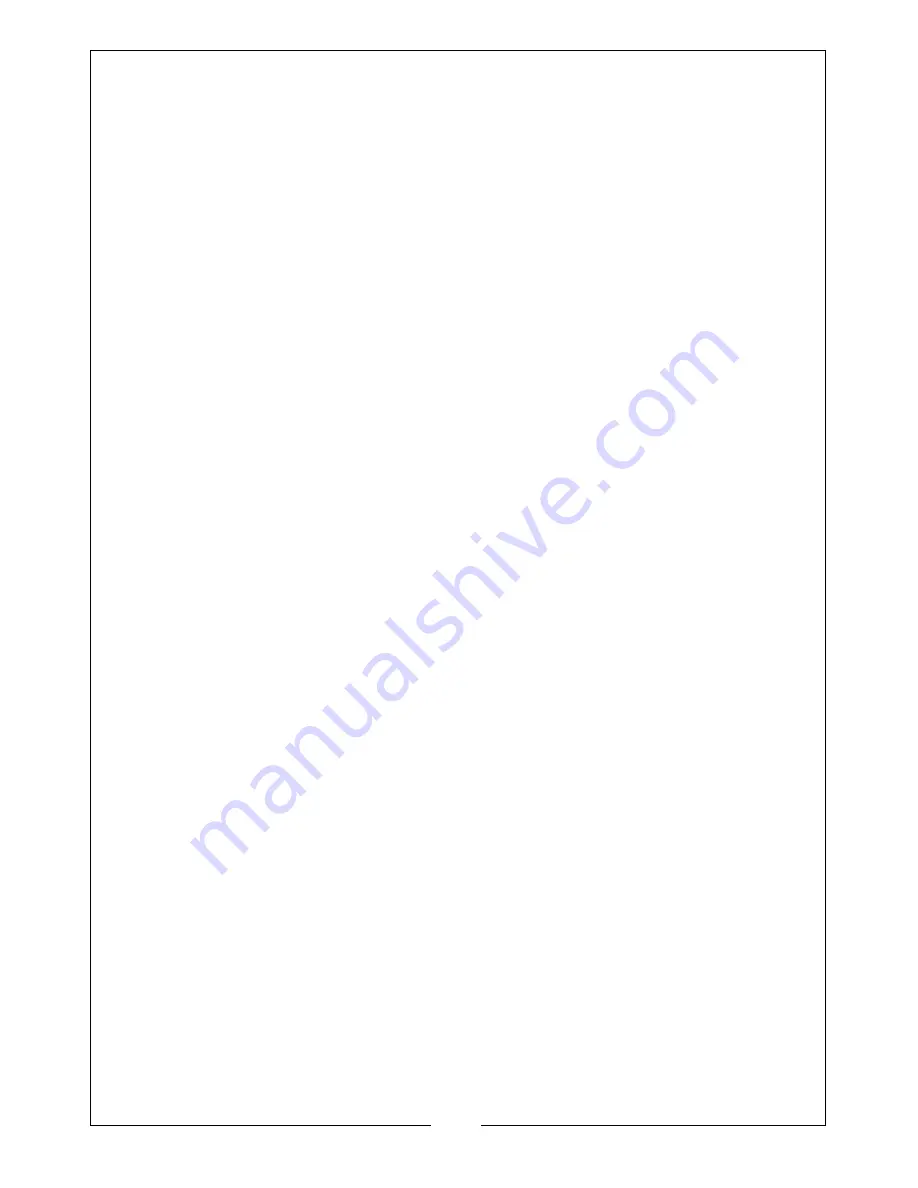
4
Parts & Service: 020 8988 7400 / E-mail: [email protected] or [email protected]
15. Keep safety guards in place at all
times when the machine is in use. If
removed for maintenance
purposes, use extreme caution
and replace the guards
immediately.
16. Make sure the planer/thicknesser is
firmly secured to the floor or bench
before use.
17. Check damaged parts. Before
further use of the machine, a
guard or other part that is
damaged should be carefully
checked to determine that it will
operate properly and perform its
intended function. Check for
alignment of moving parts, binding
of moving parts, breakage of
parts, mounting and any other
conditions that may affect its
operation. A guard or other part
that is damaged should be
properly repaired or replaced.
18. Provide for adequate space
surrounding work area and non-
glare, overhead lighting.
19. Keep the floor around the
machine clean and free of scrap
material, oil and grease.
20. Keep visitors a safe distance from
the work area. Keep children
away.
21. Make your workshop child proof
with padlocks, master switches or
by removing starter keys.
22. Give your work undivided
attention. Looking around,
carrying on a conversation and
“horse-play” are careless acts that
can result in serious injury.
23. Maintain a balanced stance at all
times so that you do not fall or lean
against the cutterhead or other
moving parts. Do not overreach or
use excessive force to perform any
machine operation.
24. Use the right tool at the correct
speed and feed rate. Do not force
a tool or attachment to do a job
for which it was not designed. The
right tool will do the job better and
safer.
25. Use recommended accessories;
improper accessories may be
hazardous.
26. Maintain tools with care. Keep
knives sharp and clean for the best
and safest performance. Follow
instructions for lubricating and
changing accessories.
27. Turn off the machine before
cleaning. Use a brush or
compressed air to remove chips or
debris — do not use your hands.
28. Do not stand on the machine.
Serious injury could occur if the
machine tips over.
29. Never leave the machine running
unattended. Turn the power off
and do not leave the machine
until it comes to a complete stop.
30. Before turning on machine,
remove all extra equipment such
as keys, wrenches, scrap, stock,
and cleaning rags away from the
machine.
31. Always use a hold-down or push
block when surfacing stock less
than 300mm inches long, or 75mm
wide, or 75mm thick.
32. Do not perform edge jointing
operations on material shorter than
150mm, narrower than 18mm or
less than 6mm thick.
Summary of Contents for CPT1000
Page 24: ......