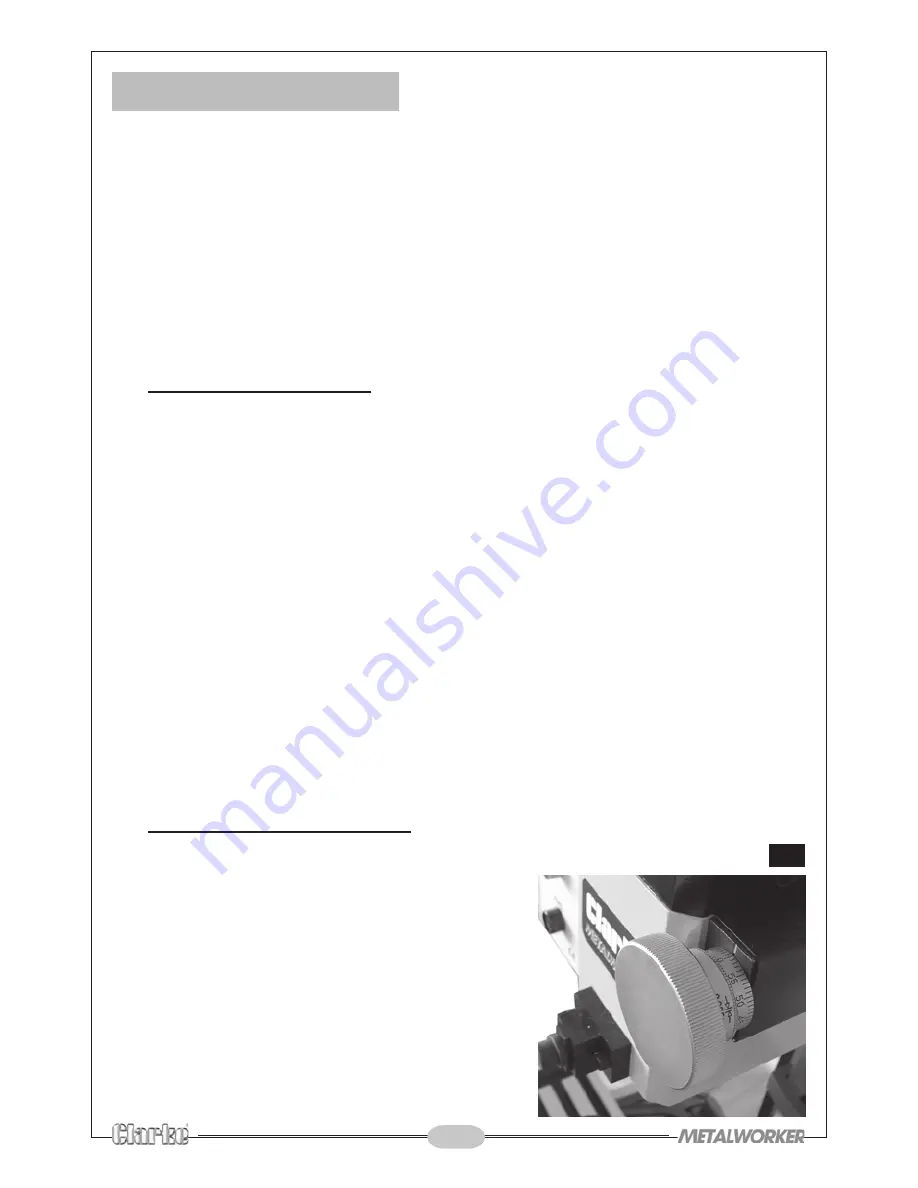
12
B. Milling
Vertical Milling is similar to drilling, except that instead of the workpiece being held stationary,
it may be moved in 3 directions - a. vertically, and b. horizontally in both axis. Milling cutters
are capable of cutting with their ends and their faces.
Several broad categories of end and face milling tools exist, such as centre cutting versus
non-centre cutting (whether the mill can take plunge cuts), and categorisation by number
of flutes, by helix angle, by material, and by coating material. Each category may be
further divided by specific application and special geometry.
Please note that It is not within the scope of this manual to advise on types of cutter, it is
assumed that the user is familiar with milling applications, cutters and techniques.
This machine is also capable of milling at any angle from vertical - 90º, to 45º left or right
of vertical.
Installing the Cutter
If the chuck is installed, proceed as follows:
1.
Insert the tommy bar into the hole in the side of the head so that it locates in the hole
in the spindle.
2.
Remove the draw bolt cover and with the spindle being held, undo the draw bolt by
two complete turns only, using the spanner provided.
3.
Strike the head of the draw bolt sharply with a soft faced mallet, or by placing a
piece of wood on the head and striking the wood with a hammer. The taper shank
will disengage, thereby allowing the draw bolt to be fully unscrewed and the drill
chuck and taper shank to be withdrawn.
NOTE: It is possible that when the head of the draw bolt is struck, the chuck could become
disengaged with the taper shank and drop on to the bed, with possible resultant damage.
It is strongly advised therefore, that the operator holds the chuck with one hand whilst
striking the head of the draw bolt, or a substantial piece of cloth is placed beneath the
chuck, in order to avoid damage when it drops.
With the taper shank removed, the cutter may be installed in a similar manner to the drill
chuck, please see the notes on pages 10/11.
Please note that a range of accessories, including collet sets and collet chuck sets which are used
to secure the cutter, are available from your Clarke dealer - see Accessories on page s 20/21.
Using the Micro Feed
17
For Milling, the micro feed should always be used.
In order to use this device, it is first of all necessary to
engage the dog clutch on the raise/lower hub
assembly. Simply turn the raise/lower handles until the
cutter is as near the workpiece as possible and the
dogs become aligned, then push the hub IN fully.
In this mode, the handles cannot be used to raise or
lower the head, only by turning the micro adjuster
knob, will this be effected.
A scale on the adjuster sleeve may be used to
determine the depth of cut.
Turn the adjuster so that the cutter just touches the
workpiece, then zero the scale by holding the adjuster
Fig.8
Summary of Contents for CMD300
Page 8: ...8 Parts Identification FIG A FIG B FIG C ...
Page 15: ...15 Parts Diagram ...
Page 16: ...16 Parts Diagram ...
Page 23: ...23 ...
Page 24: ......