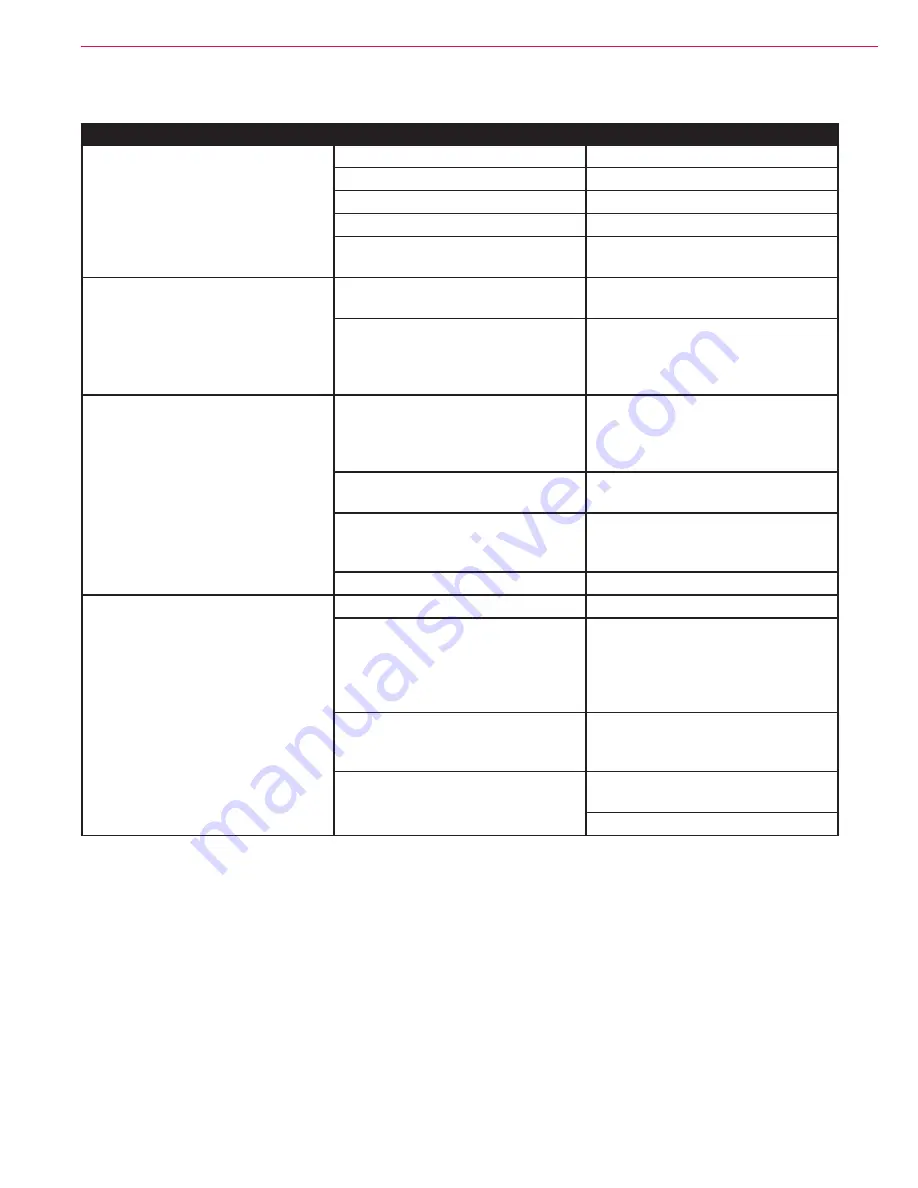
Recovery System
29
Service Manual – CA90 32T
Troubleshooting
Pr
Problem
Cause
Correc tion
• No Vacuum Motor Operation
(Other functions work)
• Vacuum circuit breaker tripped
• Reset circuit breaker
• Defective vacuum motor
• Replace vacuum motor
• Defective vacuum solenoid
• Replace solenoid
• Defective vacuum switch
• Replace vacuum switch
• Defect in wiring
• Trace wiring using circuit
diagram
• Poor pick-up at squeegee
Restricted air flow
• Clogged or kinked vacuum
(pick-up) hose
• Check and clean out vacuum
(pick-up) hose
• Clog at center tube of
squeegee casting, pick-up tube
adapter, or recovery tank entry
hole
• Check and clean all (3) places
Air Leaks
• Recovery tank cover gasket is
leaking
• Insure the cover is fully in
place. Replace the cover
assembly if there is damage to
the gasket
• Drain hose stopper is not fully
seated
• Seat the stopper into the drain
hose properly
• Pick-up tube adapter is not
adjusted properly
• Adjust pick-up tube adapter
(See instructions above in
maintenance section
• Drain hose has leaks
• Replace drain hose assembly
Squeegee Issues
• Squeegee angle not correct
• Adjust squeegee angle
• Squeegee not mounted
properly
•
Confirm that the squeegee
is mounted firmly, and that
the “T” nuts are seated into
the notches of the squeegee
bracket
• Squeegee blades have dirt or
debris between the blade and
the floor
• Clean off the squeegee blades
using a damp cloth
• Squeegee blades are worn out
or torn
• Flip the squeegee blades to put
a different edge on the floor
• Change the squeegee blades
Poor pick-up at squeegee
Good water pick up performance depends on the proper amount of air flowing through the squeegee
assembly. Air entering the vacuum system before the squeegee will reduce it’s ability to pick up water.
Anything that restricts the movement of air through the system will also reduce it’s ability to pick up water.
It is also critical to the recovery system that the squeegee blades are in good condition, and in the correct
position (angle). Adjustment of the squeegee angle and instructions for replacing the squeegee blades will be
discussed in the squeegee system section.