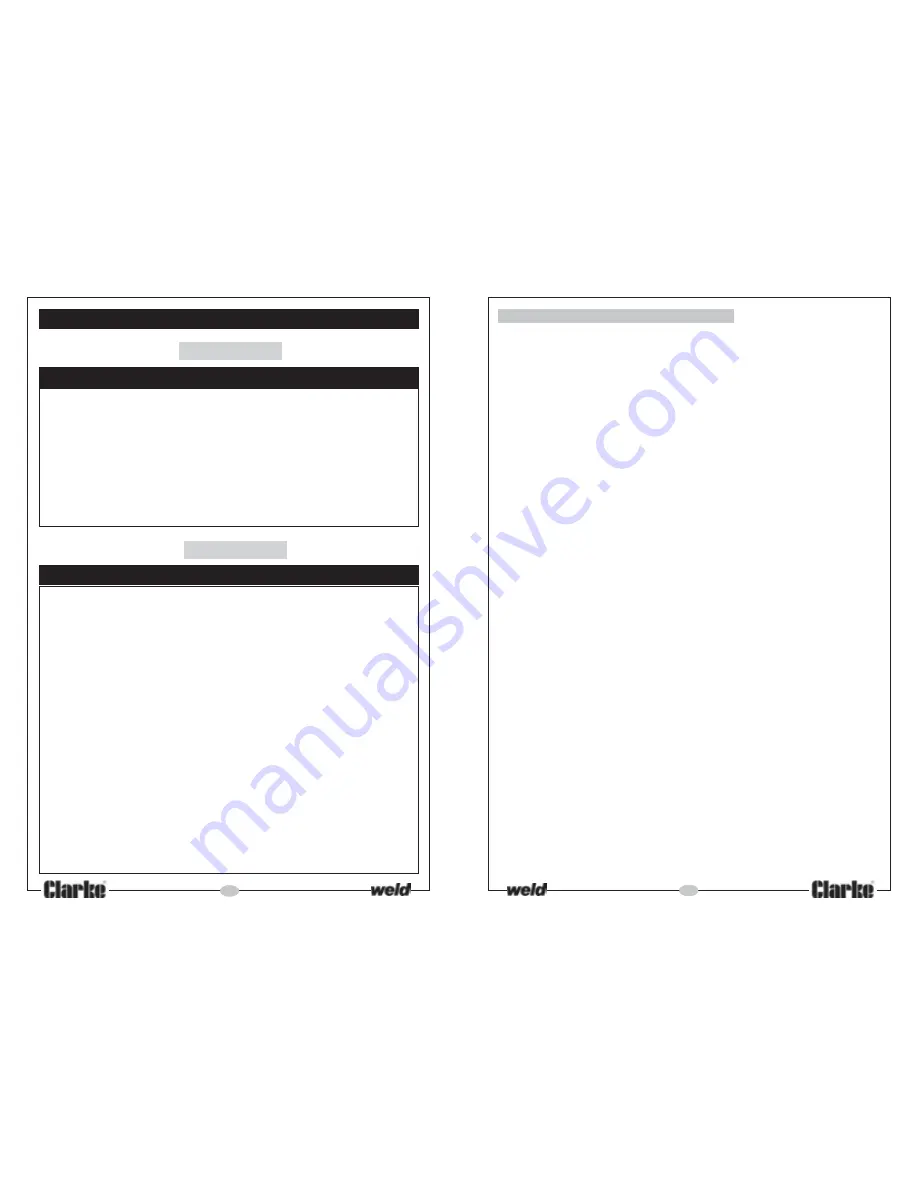
7
C) Fire and explosion prevention
Causes of fire and explosion are:
1) combustibles reached by the arc, flame, flying sparks, hot slag or heated
material;
2) misuse of compressed gases and cylinders;
3) short circuits.
BE AWARE THAT flying sparks or falling slag can pass through cracks, along pipes,
through windows or doors, and through wall or floor openings, out of sight of the
goggled operator. Sparks and slag can fly 10m.
To prevent fires and explosion: keep equipment clean and operable, free of oil,
grease, and (in electrical parts) of metallic particles that can cause short circuits.
If combustibles are in area, do NOT weld or cut. Move the work if practicable, to
an area free of combustibles.
Avoid paint spray rooms, dip tanks, storage areas, ventilators. If the work cannot
be moved, move combustibles at least 10m. away out of reach of sparks and
heat; or protect against ignition with suitable and snug fitting, fire- resistant covers
or shields.
Walls touching combustibles on opposite sides should not be welded on (or cut).
Walls, ceilings, and floor near work should be protected by heat resistant covers
or shields. Fire watcher must be standing by with suitable fire extinguishing
equipment during and for some time after welding or cutting if:
a) appreciable combustibles (including building construction) are within 10m.
b) appreciable combustibles are further than 10m but can be ignited by sparks.
c) openings (concealed or visible) in floors or walls within 10m can expose
combustibles to sparks.
d) combustibles adjacent to walls, ceilings, roofs or metal partitions can be
ignited by radiant or conducted heat.
After work is done, check that area is free of sparks, glowing embers, and flames.
An empty container that held combustibles, or that can produce flammable or
toxic vapours when heated, must never be welded on or cut, unless container
has first been cleaned. This includes.......a thorough steam or caustic cleaning (or
a solvent or water washing, depending on the combustible’s solubility) followed
by purging and inerting with nitrogen or carbon dioxide, and using protective
equipment.
Water filling just below working level may substitute for inerting.
A container with unknown contents should be cleaned (see paragraph above),
do NOT depend on sense of smell or sight to determine if it is safe to weld or cut.
Hollow castings or containers must be vented before welding or cutting - they
can explode.
In explosive atmospheres, never weld or cut where the air may contain flammable
dust, gas, or liquid vapours.
22
No. Description
Qty
Part No.
Part No.
1
Input Cable ........................................... 1
EM20220014
EM20220014
2
Green Pilot-light Switch 16a-250v ....... 1
EM22200002
EM22200002
3
Upper Panel .......................................... 1
EM33705220
EM33705220
4
Belt Regulator ....................................... 1
EM21600024
EM21600024
5
Cable Clamp ........................................ 1
EM21605009
EM21605009
6
Potentiometer Knob ............................ 1
EM21690127
EM21690127
7
Module For Inverter .............................. 1
EM42735015
EM42735016
8
Lower/Back Panel ................................ 1
EM33700139
EM33700139
9
Din Plug ................................................. 2
EM22100002
EM22100002
No. Description
Qty
Part No.
1
Input Cable ................................................................... 1
EM20220014
2
Complete Fan .............................................................. 1
EM22800021
3
Choke Winding Inverter ............................................... 1
EM44035052
4
Cable Clamp ................................................................ 1
EM21605010
5
Plastic Vent .................................................................... 1
EM21690287
6
Cover Panel .................................................................. 1
EM33705335
7
Potentiometer 10k ........................................................ 1
EM26086008
8
Dividing Panel ............................................................... 1
EM33620104
9
Feet ................................................................................ 2
EM21610019
10
Transformer 230v .......................................................... 1
EM44155027
11
On/Off Switch 16a-250v .............................................. 1
EM22200002
12
Rear Panel ..................................................................... 1
EM33700180
13
Plastic Abat-vent .......................................................... 1
EM21690286
14
Female Dinse Plug ........................................................ 2
EM22100002
15
Coupling For Belt .......................................................... 2
EM21690117
16
Belt For Inverter ............................................................. 1
EM21600023
17
Complete Inverter P.c.board ...................................... 1
EM42735020
18
Front Panel .................................................................... 1
EM33710250
19
Potentiometer Knob .................................................... 1
EM21690288
PARTS LISTS
TIG90
&
TIG115
TIG150