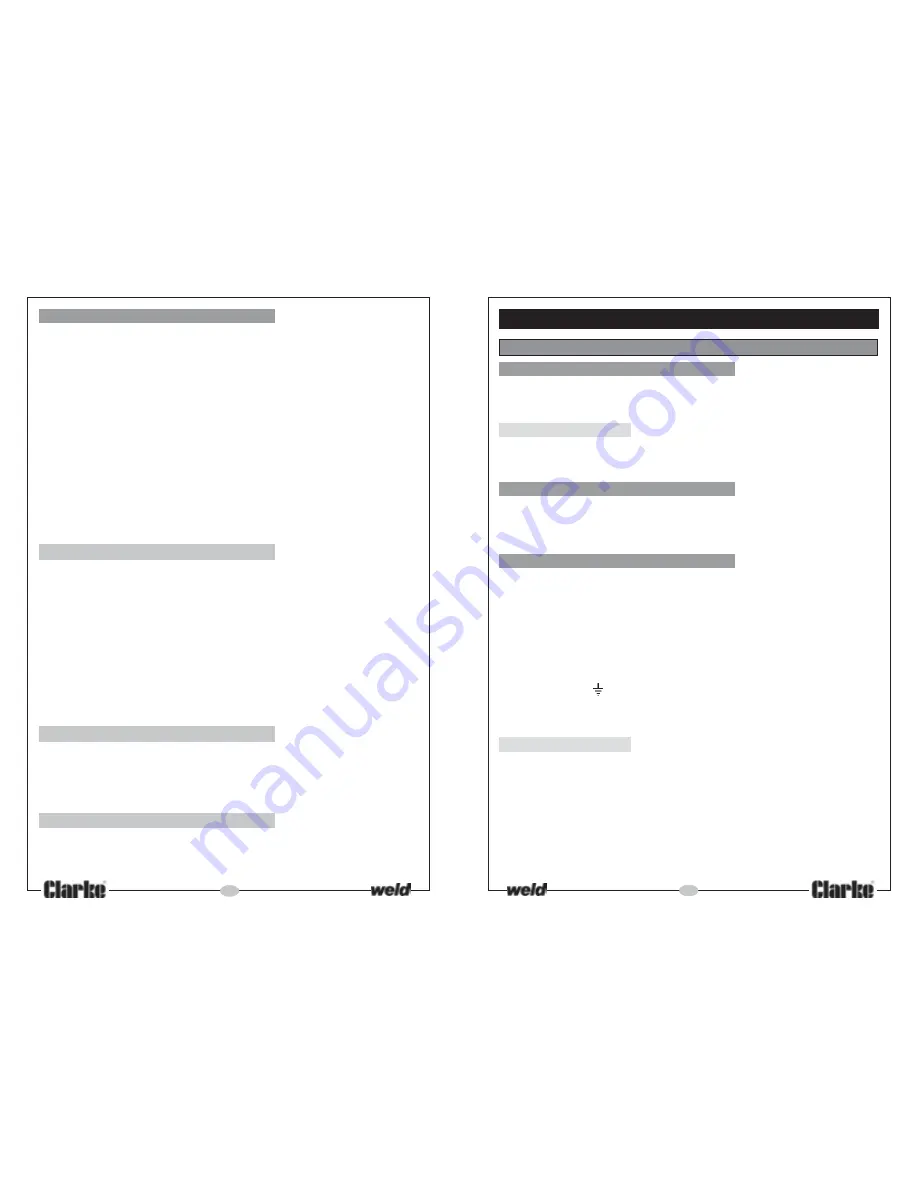
2. TIG WELDING
TIG welding Is primarily a DC current process, but can also utilise AC, usually for
very thin materials and when welding Aluminium or other non ferrous metals. It
uses a non-consumable tungsten (or tungsten alloy) electrode, held in a torch.
Shielding gas (100% Argon), is fed through the torch to protect
a.
the electrode,
b.
molten weld pool,
and c.
solidifying weld metal........ from contamination by the atmosphere.
The electric arc is produced by the passage of current through the conductive,
ionized shielding gas. The arc is established between the tip of the electrode and
the work. Heat generated by the arc melts the base metal. Once the arc and
weld pool are established, the torch is moved along the joint and the arc
progressively melts the joined surfaces. Filler wire, if used, is usually added to the
leading edge of the weld pool to fill the joint.
This process is ideally suited for welding thin metals, pressure vessels, heat
exchangers, pipes etc., where accuracy and a high quality weld is desired, as it
produces a very low porosity weld.
Tig Welding Process Advantages
•
It produces superior quality welds, generally free of defects.
•
It is free of the spatter which occurs with other arc welding processes.
•
It can be used with or without filler metal as required for the specific
application.
•
It allows excellent control of root pass weld penetration.
•
It can produce inexpensive autogenous welds at high speeds.
•
It can use relatively inexpensive power supplies.
•
It allows precise control of the welding variables.
•
Welds all metals
•
Capable of welding very thin material (0.5mm), without undue distortion.
Main Features of Tig Welding
1.
Welds all metals.
2.
Electronic control of welding current.
3.
Forced air cooling.
4.
A Thermal Overload Protection Device prevents overheating the transformer.
Limitations
1.
Greater weld dexterity is required
2.
It is more expensive to weld thicker materials - greater than 4 - 5mm
14
15
WARNING! THIS APPLIANCE MUST BE EARTHED.
a. Arc/TIG90
Connect the power cable directly to suitably fused, 230 volt (50Hz) domestic
electrical supply or to a standard 13 amp BS 1363 plug, fitted with a 13 amp fuse.
We
strongly recommend that this be done via a Residual Current Device (RCD).
Fuse Rating
The fuse in the plug must be replaced with one of the same rating (
13 amps
) and
this replacement must be ASTA approved to BS1362.
b. Arc/TIG’s 120 & 150
Connect the mains lead, through a suitably fused isolator switch, to a 230 Volt
(50Hz) electrical supply, with a fuse rating in accordance with the specifications
shown on page 21.
A standard 13 Amp plug MUST NOT be used with these welders.
c. ALL MODELS
IMPORTANT: The wires in the mains lead are coloured in accordance with the
following code:
Green & Yellow .......... Earth
Blue .......... Neutral
Brown .......... Live
As the colours of the flexible cord of this appliance may not correspond with the
coloured markings identifying terminals in your plug, proceed as follows:
•
Connect GREEN & YELLOW cord to plug terminal marked with a letter “E” or
Earth symbol “ ”, or coloured GREEN or GREEN & YELLOW.
•
Connect BROWN cord to plug terminal marked letter “L” or coloured RED.
•
Connect BLUE cord to plug terminal marked letter “N” or coloured BLACK.
Extension Cable
If an extension cable is fitted, ensure the minimum cross section of the conductor
is 1.5mm
2
for up to 15 metres in length, and 2.5mm
2
for up to 25 metres.
ELECTRICAL CONNECTIONS