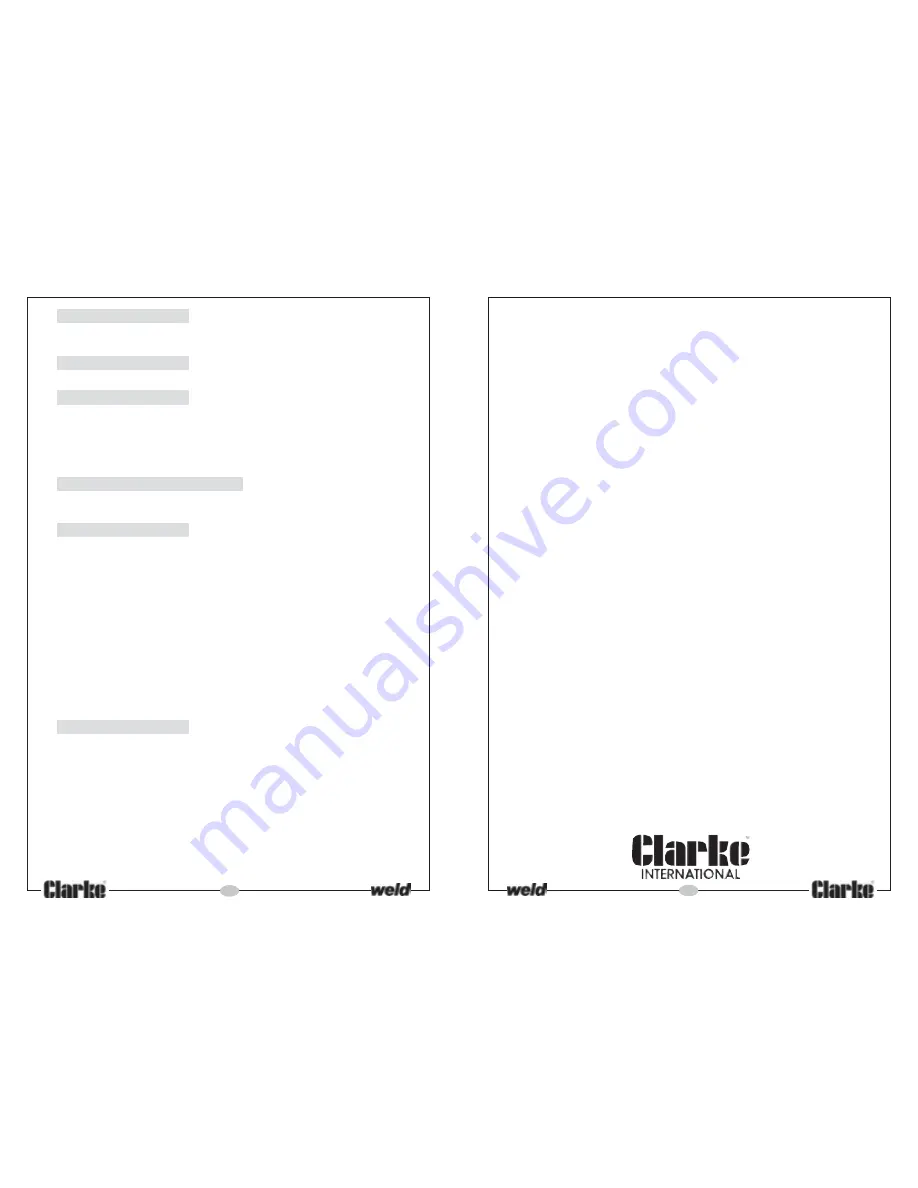
10
2) Electrode holders
Fully insulated electrode holders should be used. Do NOT use holders with
protruding screws or with any form of damage.
3) Connectors
Fully insulated lock-type connectors should be used to join welding cable.
4) Cables
Frequently inspect cables for wear, cracks and damage. IMMEDIATELY
REPLACE those with excessively worn or damaged insulation to avoid
possibly lethal shock from bared cable. Cables with damaged areas may
be taped to give resistance equivalent to original cable. Keep cable dry,
free of oil and grease, and protected from hot metal and sparks.
5) Terminals and other exposed parts
Terminals and other exposed parts of electrical units should have insulating
covers secured before operation.
6) Electrode
a) Equipment with output on/off control (contactor)
Welding power sources for use with the gas metal arc welding, gas
tungsten arc welding and similar processes normally are equipped with
devices hat permit on/off control of the welding power output. When
so equipped the electrode wire becomes electrically LIVE when the
power source switch is ON and welding gun switch is closed. Never
touch the electrode wire or any conducting object in contact with
the electrode circuit unless the welding power source is off.
b) Equipment without output on/off control (no contactor)
Welding power sources used with shielded metal arc welding and similar
processes may not be equipped with welding power output on/off
control devices. With such equipment the electrode is electrically LIVE
when the power switch is turned ON. Never touch the electrode unless
the welding power source is off.
7) Safety devices
Safety devices such as interlocks and circuit breakers should not be
disconnected or shunted out. Before installation, inspection, or service of
equipment,shut OFF all power and remove line fuses (or lock or red-tag
switches) to prevent accidental turning ON of power. Do not open power
circuit or change polarity while welding. If, in an emergency, it must be
disconnected, guard against shock burns, or flash from switch arcing.
Always shut OFF and disconnect all power to equipment. Power disconnect
switch must be available near the welding power source.
Scratch the tip of the electrode on soon as an arc develops, quickly withdraw
the electrode to maintain a gap of approx. 3-4 mm, and proceed to weld.
(See notes below).
To stop welding, simply remove the torch from the workpiece.
This method is referred to as ‘Scratch Arc’.
REMEMBER to turn OFF the gas immediately you finish welding.
NOTES:
a) To avoid a visible strike mark on the surface of the workpiece, it is advisable to
strike the arc in the joint, where the mark will be concealed by the weld.
b) Thin sheet and stainless steel may be welded with or without filler, similar to
gas welding.
The filler is fed in at the edge of the pool. The rod must not touch the tip of the
electrode or enter the arc. The end of the rod must always be shielded by the
argon atmosphere to prevent as far as possible the formation of oxides of its
surface. When welding stainless steel and copper, it is often possible to feed
in the filler continuously at the edge of the pool.
c) The arc length generally varies between 3 and 6mm. depending on the type
of joint, type and thickness of material, and so on.
d) The torch is advanced in the direction of welding, without lateral movement,
maintaining the torch angle of 45
0
to the workpiece.
Guidelines for the TIG welding current needed and recommended electrode sizes
etc. for different gauges of material are shown in the chart on the following page:
19