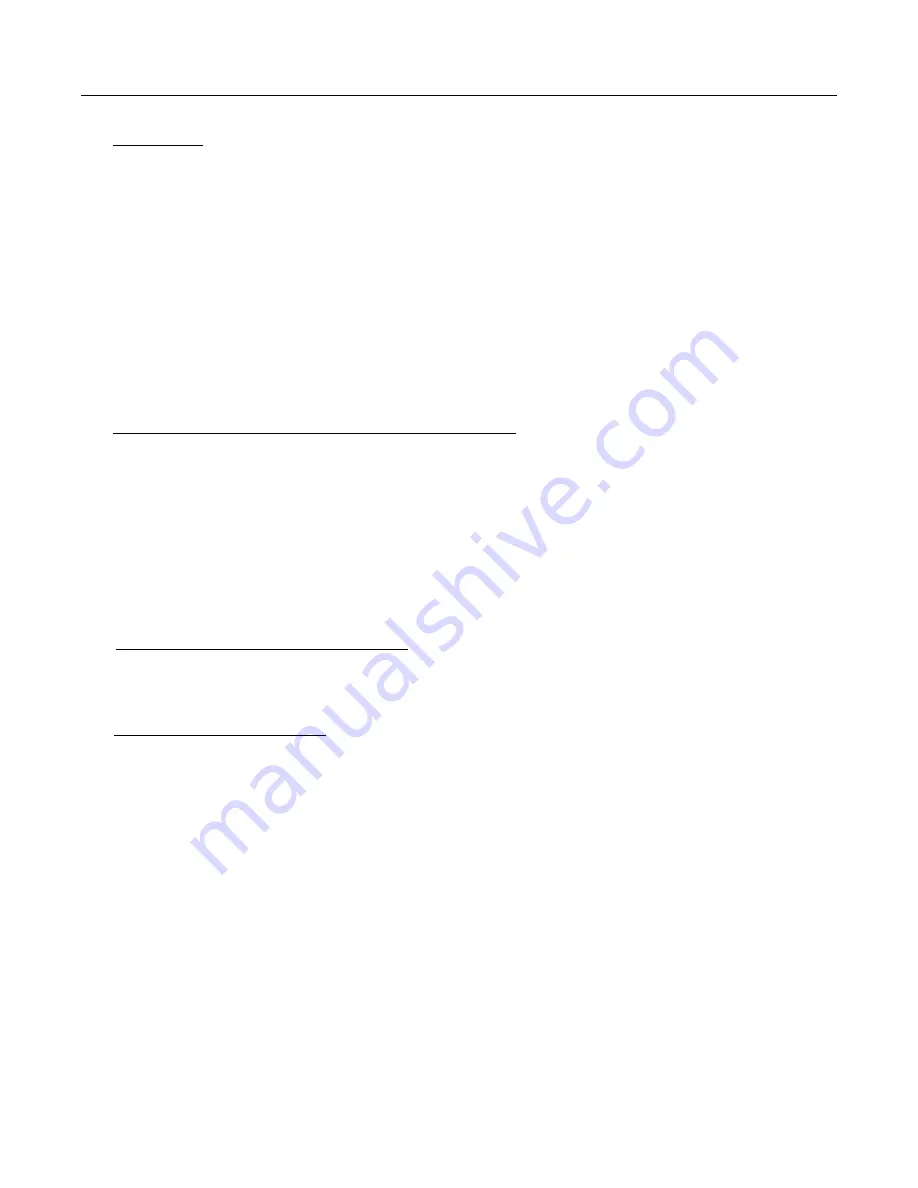
Page 8
4.0 Programming
4.1 Set Dip Switch #8 to the ON position.
4.2 Select the desired program number to change. The LED should be flashing.
4.3 Select DRY TIME. Set the time with the UP/DOWN arrows.
4.4 Select COOL TIME. Set the time with the UP/DOWN arrows.
4.5 Select TEMPERATURE. Set the temperature with the UP/DOWN arrows.
4.6 Press and hold the PROGRAM button about 3 seconds until the LED stops flashing. The selected program
number is now programmed. If the PROGRAM button is pressed for less than 3 seconds, the controller will
cancel the program and display the next programs settings. If not programmed correctly, the display will flash
E2F for 4 seconds, and the default settings will be used. Follow steps 4.2 through 4.7 to re-program any
program number. When finished, set DIP Switch #8 to OFF. The programs are now stored.
4.7 During the program mode, if the UP/DOWN arrows, REV, or DISPLAY button is not pressed within 10
seconds the default program settings will be used.
5.0 Temporary Re-Programming of Current Programs (OPL only)
5.1 The Drying Time, Cooling Time, Temperature, and Reversing Mode of a program currently in use may be
modified simply by adjusting any or all of the program parameters for that program, as needed. Once a
modification has been made the current program LED will flash indicating that it has been modified.
5.2 Use the UP/DOWN arrows to adjust program time.
5.3 Use the Display Select button to choose between Drying Time, Cooling Time, and Temperature. Then use
the UP/DOWN arrows to adjust the times and temperature.
5.4 To cancel this temporary programming mode push the STOP button once to stop the current cycle and once
more to cancel the modified program settings. The program will revert back to its original settings.
6.0 Operational Check for the Board Diagnostics
6.1 Cycle the gear cabinet to check if the buzzer activates.
6.2 The display will read P-F if the thermistor is short circuited or open circuited.
DIAGNOSTIC MICROPROCESSOR CONTROL - FEATURES
7.0 Description of the Control Panel
(See illustration on page 5)
1.
START.
Starts or resumes the current program or cycle.
2.
STOP.
Temporarily halts the current cycle or cancels the current program.
3.
REVERSING/NON-REVERSING (REV).
Not used in this application.
3.1
REVERSING LED.
Will illuminate if reversing is pushed but has no effect on operation.
4.
UP/DOWN ARROWS.
Increases or decreases the value in the display. In conjunction with the
DISPLAY button, these buttons are used to adjust the drying time, cooling time, tempera-
ture, clockwise time, dwell time, counter-clockwise time, and minutes per coin (COIN only).
4.1
DISPLAY.
Displays the drying time, cooling time, drying temperature, and diagnostics.
5.
DISPLAY SELECT.
Toggles the display between the drying time, cooling time, and temperature
settings. Pressing the DISPLAY button for 3 seconds allows the user to display the drying cycle
temperature.
5.1
DRYING LED.
Illuminated when in the drying cycle.
Summary of Contents for Gear Cabinet
Page 11: ...Page 11 MAIN ASSEMBLY...
Page 16: ...Page 16 WIRING SCHEMATIC AGC65 240V 50 60 3...
Page 17: ...Page 17 WIRING SCHEMATIC AGC64 240V 50 60 1...
Page 18: ...Page 18 WIRING SCHEMATIC AGC45 208V 60 3...
Page 19: ...Page 19 WIRING SCHEMATIC AGC44 208V 60 1...
Page 20: ...Page 20 LADDER DIAGRAM AGC65 240V 50 60 3...
Page 21: ...Page 21 LADDER DIAGRAM AGC64 240V 50 60 1...
Page 22: ...Page 22 LADDER DIAGRAM AGC45 208 60 3...
Page 23: ...Page 23 LADDER DIAGRAM AGC44 208 60 1...
Page 24: ...Page 24...