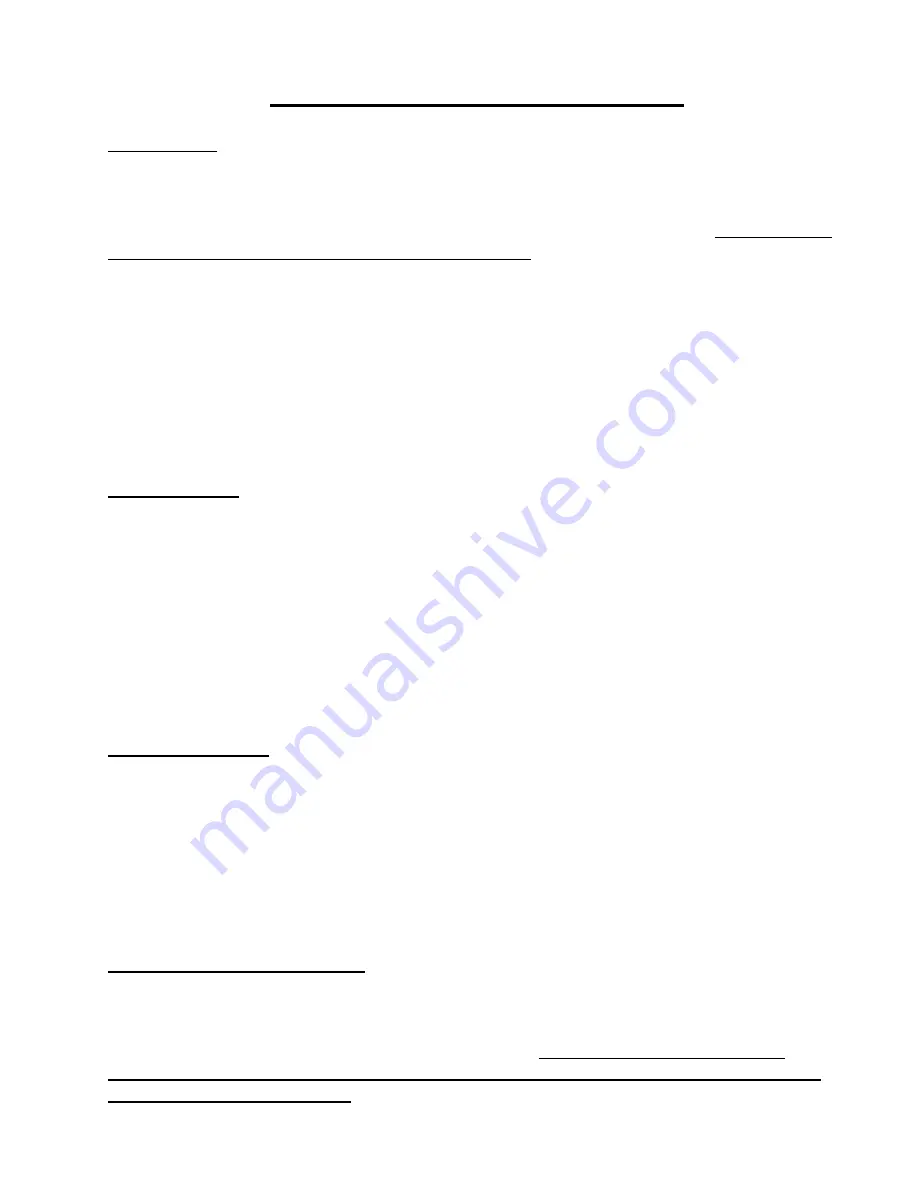
INSTALLATION INSTRUCTIONS
UNCRATING
Uncrate the machine very carefully and check for concealed damage. If any damage caused by
shipping is found, it should be reported to the transportation company and a claim filed by you.
Unbolt the machine from the base and move to approximate location of installation. CAUTION: DO
NOT USE HEADS OF BUCKS IN RIGGING MACHINE. After the machine has been placed in
position, level it by adjusting the leveling bolts.
Step #1
Connect the air supply (3/8) to the press (85 PSI, 6 Bars).
Step #2
Make sure the power switch is turned to off.
Step #3
Remove the access panel from the rear of the press.
Step #4
Connect 110V to junction box located on the inside of the right rear channel leg.
Step #5
Set head position switch to middle position.
Step #6
Turn power switch on head should go to normal operating position (about 60
degrees).
STEAM PIPING
Secure the services of a competent steam fitter. Steam inlets and outlets are marked. Do not connect
with any smaller piping than the size of the connection on the machine. Use traps and check valves
on all return lines. If your machine is piped according to the illustration on page 5, you should have
no problem with steam supply NOTE: This illustration does not illustrate the piping of this machine
but is representative of correct steam piping procedure. The connections are tagged.
If there are any questions about the connections, refer to the DETAIL LINE DRAWINGS (Page 5).
The steam must be connected to the machine in such way that the steam first goes to the press head
then to the press buck. Steam lines should be blown out thorougly before connecting to the machine.
This will prevent debris from damaging valves and stopping up lines.
COMPRESSED AIR
Connect air to the 3/8" filter / Regulator at the rear of the press. This should be drained daily or at
regular intervals. The air pressure regulator should be set at 80 to 100 p.s.i. on the gauge. The com-
pressor should be set so air does not go below 80 p.s.i. if a constant-running compressor is being
used with an unloading valve, set between 80 and 100 p.s.i. If other equipment require higher pres-
sures, it is all right to set the air compressor higher since the press has an internal preset regulator. A
cut-off valve should be installed at each machine so that it can be serviced, if necessary, without
shutting down the rest of the units.
ELECTRICAL CONNECTIONS
A qualified electrician should be employed to make connections. Electrical specifications can be
found on the machine serial plate . Electrical Connections Instructions are attached to the machine
and an electrical wiring diagram is included in this manual.
NOTE: All electrical wiring and
connections must be made in compliance with the requirements of the National Electric Code
and local codes and ordinances.
Page 2
Summary of Contents for AOLAUKMAN592
Page 6: ...Page 5...