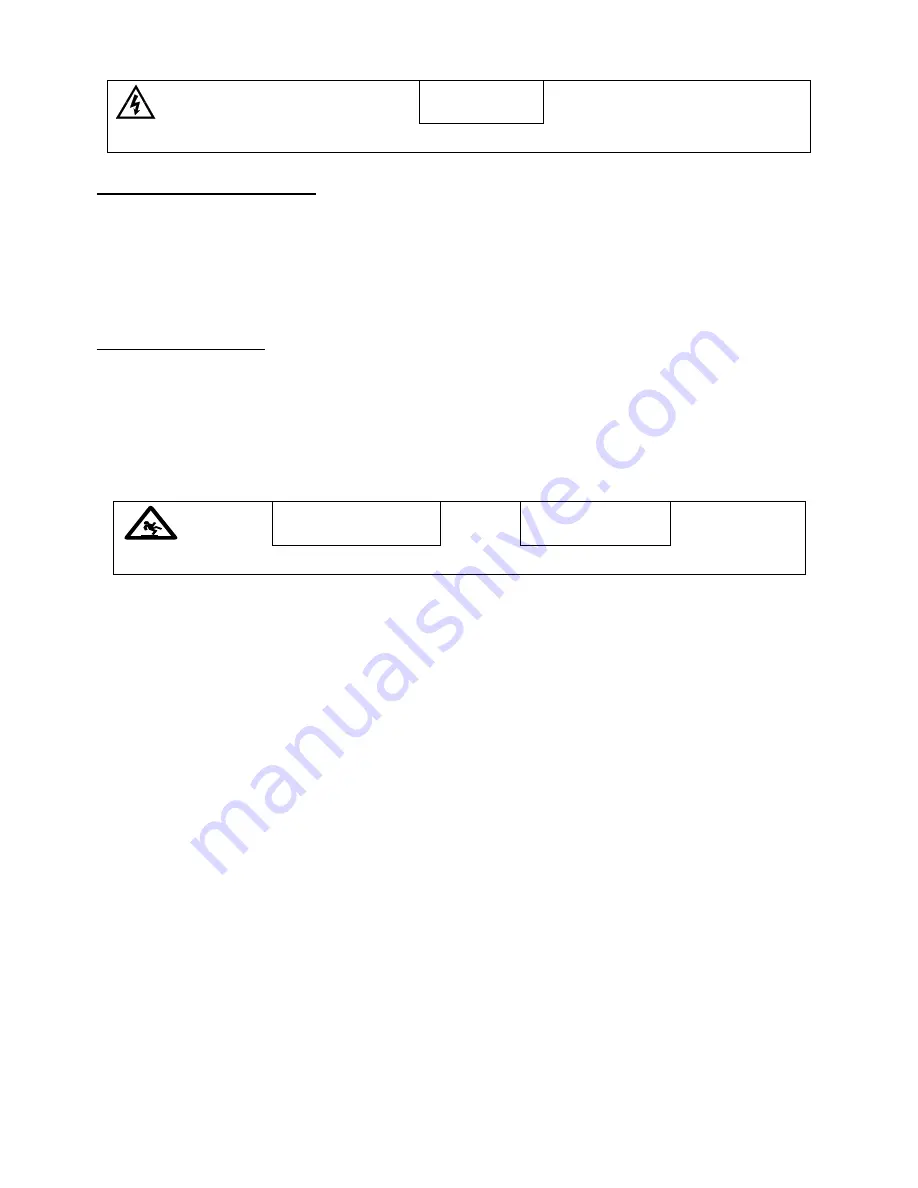
6
6
DANGER
BEFORE working on equipment, be sure all power to equipment is disconnected and locked-out.
GENERAL COMMENTS
Part number identifiers (IDPs) contained in Table 2 and shown within parenthesis such as “(8)” refer to circled
numbers shown on Assembly Drawing.
NOTE: If upon disassembly, significant wear on power or idler rotors or rotor housing is found, Imo
Pump recommends replacement of entire pump.
TOOLS REQUIRED.
The procedures described in this manual require common mechanics hand tools, an arbor press, a torque wrench
and a suitable lifting device such as a sling for smaller pumps or a strap for larger models.
PUMP DISASSEMBLY
See seal drawings (Figures 2 and 3) and assembly drawings (Figures 4 and 5)
CAUTION
ATTENTION
Fluid leakage from disassembly of pump may make floor slippery and cause personal injury.
The following steps are required before starting any maintenance action:
A)
De-energize and lock out power to driver and tag power control box “
WARNING - OUT OF SERVICE
”.
B) Close all inlet and outlet valves and tag valves “
WARNING - OUT OF SERVICE
”.
B)
Vent pressure from pump and drain pumping liquid.
C)
Remove pipe fittings/flanges at pump inlet and outlet openings.
E) Remove bolts holding pump to its mounting.
F) Remove coupling hub and key (13) from power rotor (7) shaft and locate pump on a suitable workbench.
NOTE:
The 3G Series pumps incorporate highly finished precision parts that must be handled carefully
to avoid damage to critical machined surfaces. Parts removed should be tagged for
identification and their exact positions in pump carefully noted so that new or remove parts can
be properly replaced.