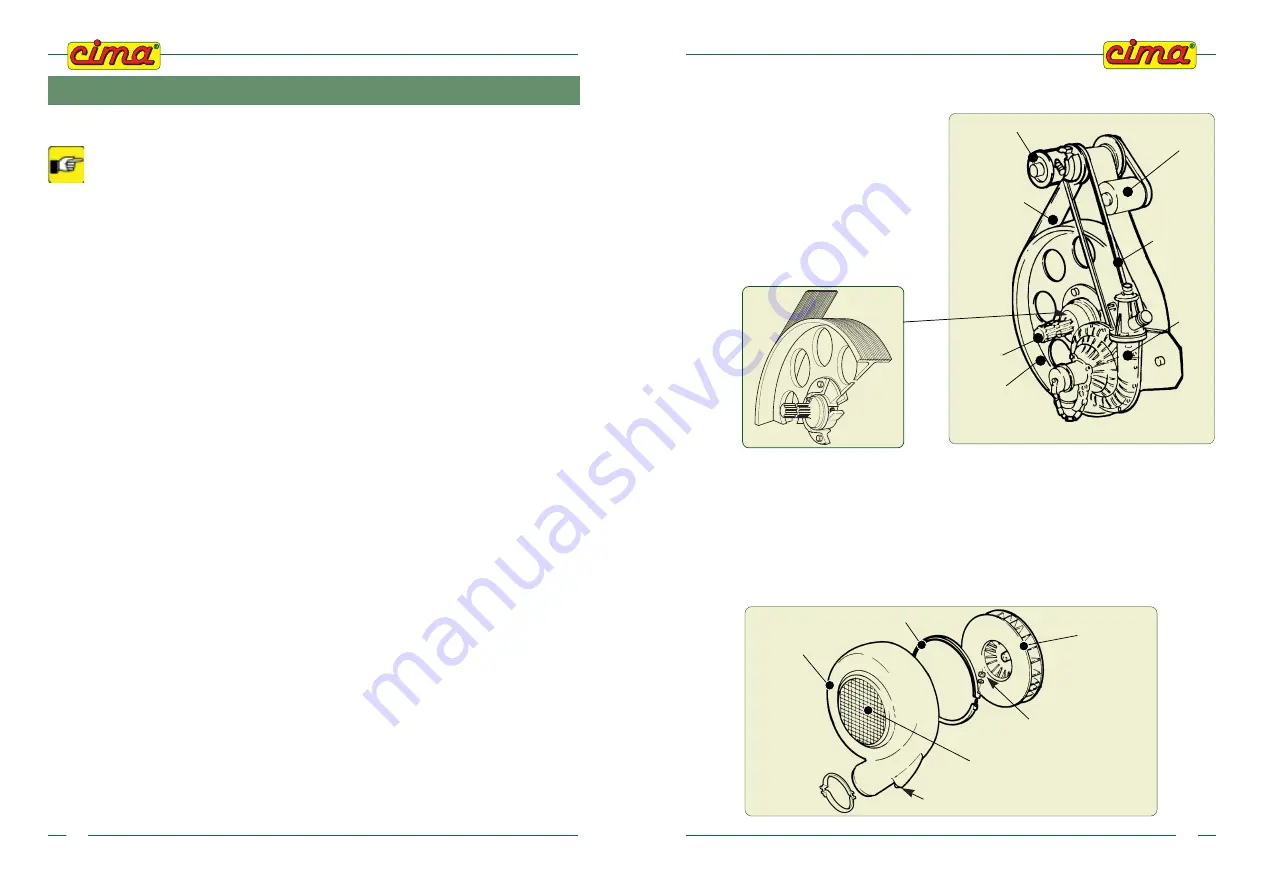
09-2008
Plus 42 - 45 - 50 - 55
13
4.2 - FAN SERVO AMPLIFIER
Centrifugal fan
The front-engaging clutch assembled on the fan shaft allows the operation of the centrifugal pump
whitout the fan. (for versions on which it is foseen).
The fan housing can rotate 360 degrees. This permits the positioning of the outlet spout at the point
necessary for the assembling of the different distribution devices.
An air intake, pre-set on the outer edge of the housing, is connected to the plunger tap placed above
the tank. Through this tap it is possible to carry out or exclude pneumatic agitation. The closed blades’
impeller is sheet steel realized and dynamically balanced; the air intake opening on the casing is
protected by a steel grating.
POWER
TAKE-OFF
(PTO)
PUMP
DRIVE
TRAPEZOID
BELT
00014
AUTOMATIC
BELT
TIGHTENER
PUMP
LOWER
PULLEY
RELEASE
FREE
WHEEL
FAN
CONTROL
POLY-V BELT
00402
00014
Servo amplifier
It is equipped with an automatic tensioner of the
driving poly-V belts that keeps the belt tension
constant, avoiding slipping and wear.
A free-
wheeling gear is included
between the Power
Take-off of the servo amplifier and the fan control
pulley (for versions on which it is forseen). In
case of sudden decelerations or unexpected
engine stoppage, this allows the fan to continue
its free rotation, thus avoiding extreme mechan-
ical stresses to be transmitted to the drive mem-
bers.
00251
FAN
SWINGING
HOUSING
COLLAR
NUT
SHAKER
AIR INTAKE
PROTECTION
GRILL
Plus 42 - 45 - 50 - 55
09-2008
56
14
FAULTS FINDING
14
A. FAULT:
By utilising the filler piping the pump doesn’t operate (suction)
It is necessary to disengage the drive outlet (PTO) and wait for it to stop rotating
before repeating the filling operation.
1. CAUSE: the quantity of water poured into the tank is insufficient to trigger the pump.
REMEDY:
Add water to the tank until the pump starts its cycle.
2. CAUSE: the filler piping sucks in air.
REMEDY:
Completely submerge the suction filter of the filler piping.
3. CAUSE
Lack of seal of the pipes.
REMEDY:
Check the tightening of ring nuts, fittings and clamps. Check the efficiency
of sealers and that piping elements are not cracked or broken. Replace parts that are
possibly found to be defective.
4. CAUSE
Slipping of the pump’s belt.
REMEDY:
Check the tension of the belt-tensioner’s spring. (4÷5 cm).
5. CAUSE
The pump’s belt might be broken.
REMEDY:
Replace the belt.
B. FAULT:
Leakage and dripping from the pump
1. CAUSE
Non-sealing of the fittings and clamps connecting the piping to the pump.
REMEDY:
Check for proper tightening of ring nuts and clamps. Check the efficiency of
the sealers. Replace parts that are possibly found to be defective.
2. CAUSE
Mechanical sealing defective.
REMEDY:
Address a C.I.M.A. point of “Sale and Service”.
C. FAULT:
Drop in pressure of the hydraulic circuit signalled by the gauge
1. CAUSE
Dirty filter.
REMEDY
: Clean the cartridge
2. CAUSE: Faulty sealing of the hydraulic circuit.
REMEDY
:
Check the operation of the pump and the tension of its belt. Check the proper
tightening of ring nuts, fittings and clamps. Check the efficiency of the sealers and the
integrity of the piping. Replace the parts that are possibly found to be defective.
3. CAUSE: Gauge defective.
REMEDY
: Replace the pressure gauge.
4. CAUSE: Suction or gauge connection pipe clogged
.
REMEDY
: Clean.
D. FAULT:
Variations in the pressure of the hydraulic circuit (marked by the gauge)
1. CAUSE
Lack of seal of the pipes and/or the valves.
REMEDY
: Check the clamping of the ring nuts, the connections and the clamps.
Verify the efficiency of the gaskets and the integrity of the pipes.
Replace the possibly defective parts.
2.
CAUSE: Residue of product at the entrance of the gauge
REMEDY
: Clean.
3. CAUSE: Wrong positioning of the circuit-washer faucet (P15) with the circuit-washer tank empty.
REMEDY
: Position the lever of the faucet correctly (P15 - pos”. 1") and fill the circuit-
washer tank.