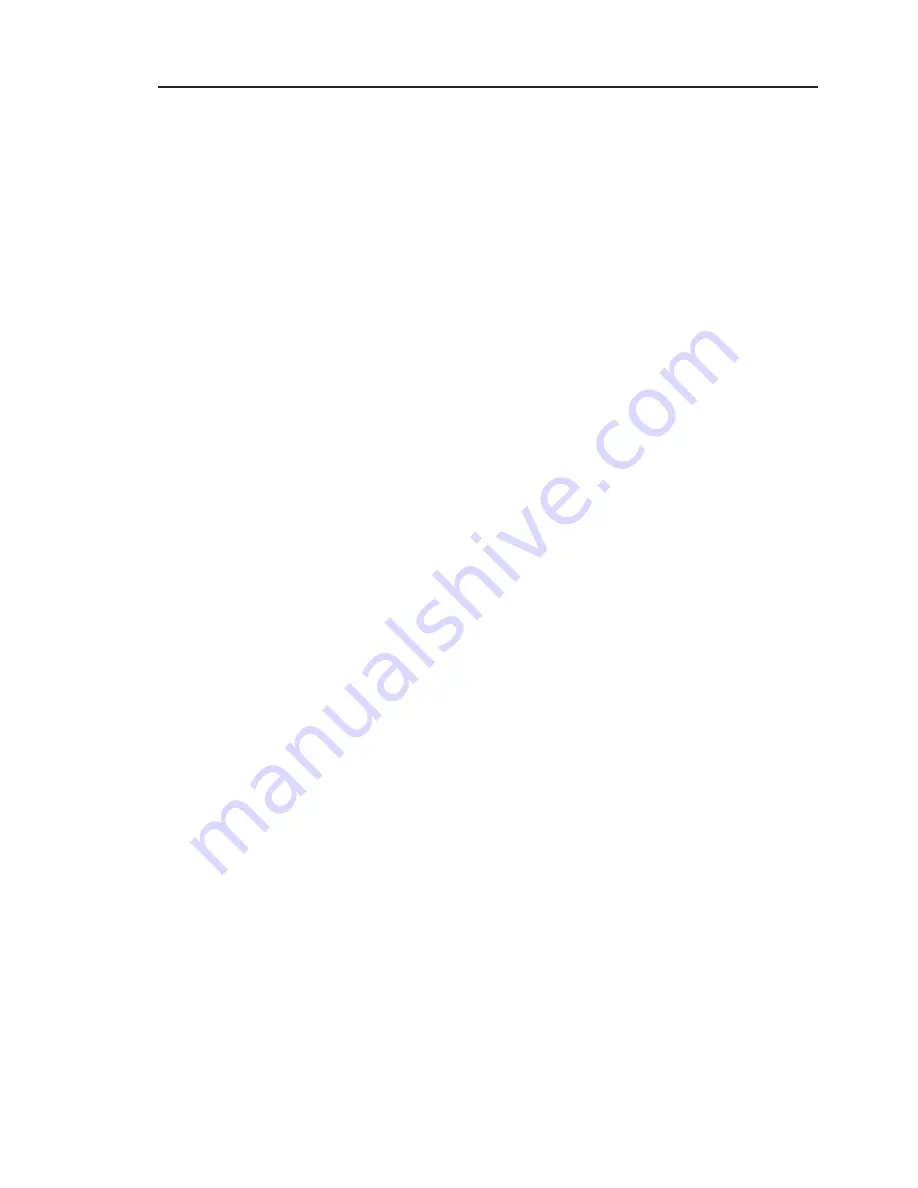
CIGWELD - LIMITED WARRANTY TERMS
LIMITED WARRANTY: CIGWELD Pty Ltd, A Victor Technologies Company, hereafter, “CIGWELD” warrants to
customers of its authorized distributors hereafter “Purchaser” that its products will be free of defects in work-
manship or material. Should any failure to conform to this warranty appear within the time period applicable to
the CIGWELD products as stated below, CIGWELD shall, upon notification thereof and substantiation that the
product has been stored, installed, operated, and maintained in accordance with CIGWELD’s specifications,
instructions, recommendations and recognized standard industry practice, and not subject to misuse, repair,
neglect, alteration, or accident, correct such defects by suitable repair or replacement, at CIGWELD’s sole
option, of any components or parts of the product determined by CIGWELD to be defective.
CIGWELD MAKES NO OTHER WARRANTY, EXPRESS OR IMPLIED. THIS WARRANTY IS EXCLUSIVE AND
IN LIEU OF ALL OTHERS, INCLUDING, BUT NOT LIMITED TO ANY WARRANTY OF MERCHANTABILITY OR
FITNESS FOR ANY PARTICULAR PURPOSE.
LIMITATION OF LIABILITY: CIGWELD SHALL NOT UNDER ANY CIRCUMSTANCES BE LIABLE FOR SPECIAL,
INDIRECT OR CONSEQUENTIAL DAMAGES, SUCH AS, BUT NOT LIMITED TO, LOST PROFITS AND BUSINESS
INTERRUPTION. The remedies of the Purchaser set forth herein are exclusive and the liability of CIGWELD
with respect to any contract, or anything done in connection therewith such as the performance or breach
thereof, or from the manufacture, sale, delivery, resale, or use of any goods covered by or furnished by CIG-
WELD whether arising out of contract, negligence, strict tort, or under any warranty, or otherwise, shall not,
except as expressly provided herein, exceed the price of the goods upon which such liability is based. No
employee, agent, or representative of CIGWELD is authorized to change this warranty in any way or grant any
other warranty.
PURCHASER’S RIGHTS UNDER THIS WARRANTY ARE VOID IF REPLACEMENT PARTS OR ACCESSORIES
ARE USED WHICH IN CIGWELD’S SOLE JUDGEMENT MAY IMPAIR THE SAFETY OR PERFORMANCE OF ANY
CIGWELD PRODUCT. PURCHASER’S RIGHTS UNDER THIS WARRANTY ARE VOID IF THE PRODUCT IS SOLD
TO PURCHASER BY NON-AUTHORIZED PERSONS.
The warranty is effective for the time stated below beginning on the date that the authorized distributor delivers
the products to the Purchaser. Notwithstanding the foregoing, in no event shall the warranty period extend
more than the time stated plus one year from the date CIGWELD delivered the product to the authorized
distributor.
Summary of Contents for 170Oi
Page 6: ......
Page 16: ...TRANSTIG 170Pi GENERAL INFORMATION 1 10 Manual 0 5242 Notes ...
Page 20: ...TRANSTIG 170Pi INTRODUCTION 2 4 Manual 0 5242 Notes ...
Page 26: ...TRANSTIG 170Pi INSTALLATION 3 6 Manual 0 5242 Notes ...
Page 44: ...TRANSTIG 170Pi OPERATION 4 18 Manual 0 5242 Notes ...
Page 46: ...TRANSTIG 170Pi INTRODUCTION 5 2 Manual 0 5242 Notes ...
Page 66: ...TRANSTIG 170Pi TROUBLESHOOTING 6 20 Manual 0 5242 Notes ...
Page 80: ...TRANSTIG 170Pi ASSEMBLY PROCEDURE 8 6 Manual 0 5242 Notes ...
Page 84: ...TRANSTIG 170Pi KEY SPARE PARTS 9 4 Manual 0 5242 Notes ...