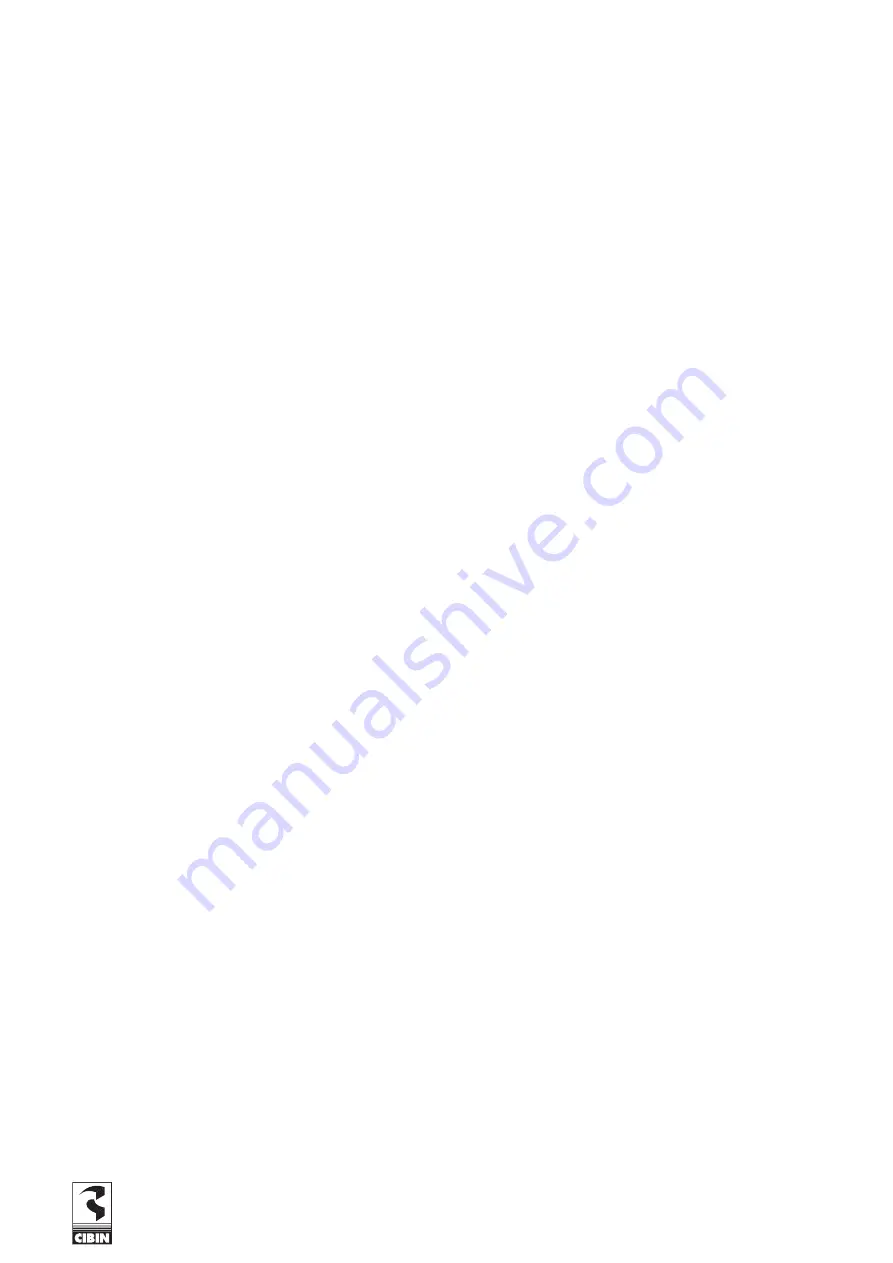
56
1. INSTALLATION
1.0 GENERAL STANDARDS AND WARNINGS
1.0.1 INSPECTION TEST AND GUARANTEE
1.0.1.1 Inspection Test
All equipment must pass inspections and tests before it is dispatched. Inspection test types are :
- visual.
- leakage control.
- optimal vacuum attainment.
- electrica.
-operation.
Equipment is dispatched ready for use. Passing of inspection tests is certified in the specific annexes.
1.0.1.2 Guarantee
Our equipment and the component parts manufactured by us are guaranteed for
1 year
from the date of manufacture, against
any defect in workmanship.
Materials found to have defects must be returned
carriage free
to the factory of dispatch, where they will be checked and
repaired or replaced in the event that, in our final judgement, they are found to be defective.
It will be the specific task of the manufacturer to repair any defects on condition that the equipment has been correctly used in
full respect of the guidelines given in the manuals.
This guarantee does not cover chance defects such as those caused during transport, handling or interventions carried out by
personnel not authorised by us, improper use, or the incorrect installation of the equipment. Materials replaced under guarantee
will remain our property.
1.0.2 FOREWORD
This manual contains all information necessary for the correct installation, use and maintenance of the equipment. The manual is
for technical personnel who are qualified to install and service the equipment. It is also for the end user in order to ensure that he
or she will use the equipment correctly. The manual is to be considered as an integral part of the machine. It is obligatory for the
user to read it carefully and to refer always to the manual before carrying out any installation or start operations. The manual,
or in any case a copy thereof, should always be kept in close proximity to the machine in order for consultation by the end user
whenever necessary.
Tampering with this manual, even partially, is strictly forbidden (copyright © )
THE MANUFACTURER DECLINES ALL RESPONSIBILITY FOR IMPROPER USE OF THE MACHINE.
1.0.3 MACHINE DESCRIPTION
The machines described in this manual are refrigerator units with water-cooled or air condensers. The machine includes :
- a condenser on the cold room exterior.
- an evaporator on the cold room interior.
- a remote control panel
- supplied fittings.
The machine is a machine that is ready for operation when installed and it has been manufactured exclusively for use as follows:
TO MAINTAIN A DETERMINED TEMPERATURE IN A COLD ROOM SUITED FOR THIS USE
This machines are destined for installation in cold rooms.
The cyclic defrosting system is fully automatic.
The machine operates using a refrigerator compressor with reciprocating motion and which operates using the power supply
mains (mono- or three-phase) and refrigerant. The refrigerant flows into the evaporator and cools its surrounding atmosphere
(by absorbing the heat). The “hot” fluid is sucked in/compressed by the compressor and sent to the exchange battery “conden-
ser” to regain its cooling capacity. The cycle is then repeated.
1.0.4 GENERAL SAFETY STANDARDS
The machine must only be used by those personnel who are aware of its specific characteristics and of the main safety procedu-
res. Accident prevention rules and other health and safety requirements must always be respected. Any unauthorised alteration
made to the machine will absolve the Manufacturer from any responsibility regarding possible resulting damages.
Summary of Contents for KUMA
Page 1: ...1 č ...
Page 2: ...2 ...