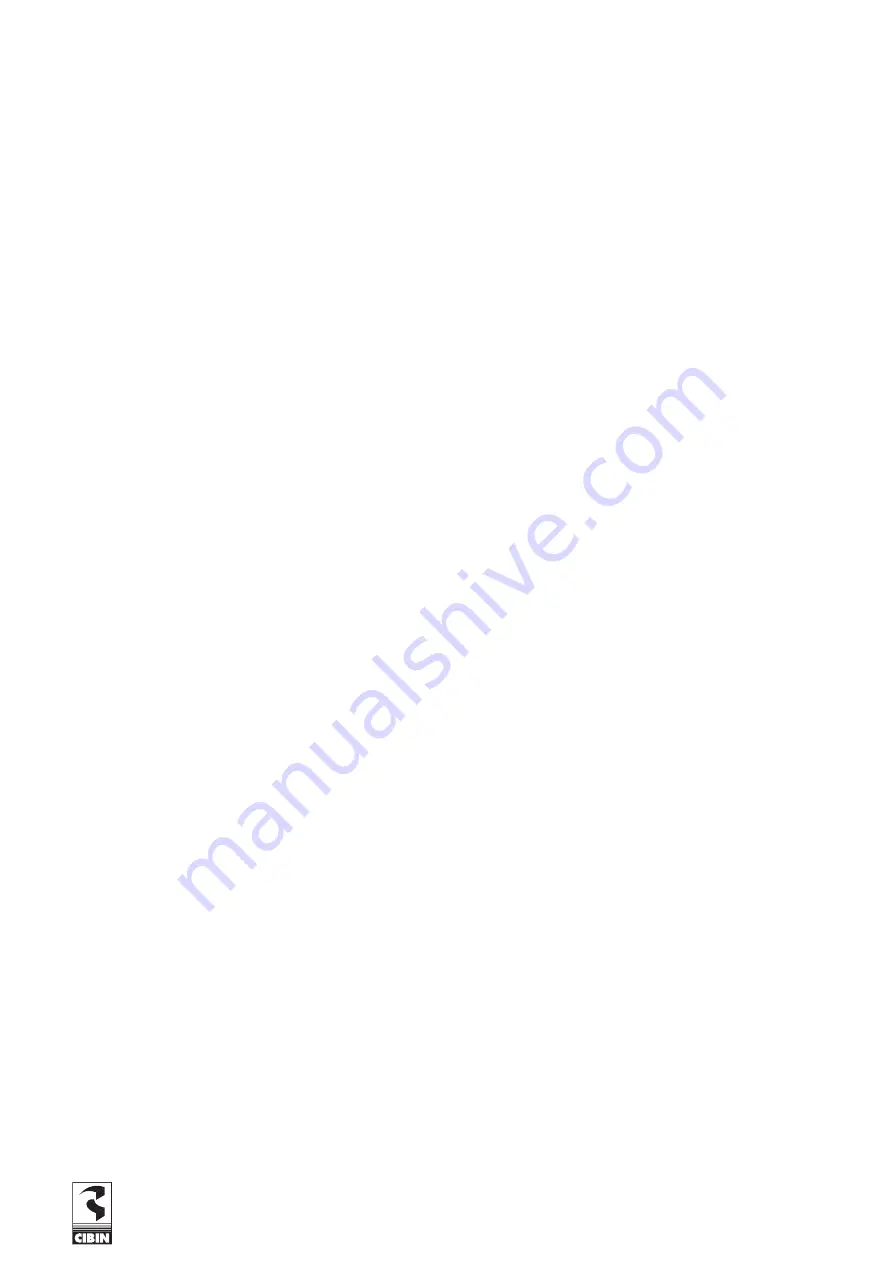
66
4.1.4 DEFROSTING
The machine carries out defrost cycles at intervals pre-set by the manufacturer.
If under specific operating conditions (very hot or humid periods of the year, the introduction of products that releases a great
deal of moisture, or frequent door opening .....), the set defrost cycles are insufficient for the complete removal of ice from the
evaporator, additional “manual” defrost cycles can be carried out. Press DEFROST
button d for more than 5 seconds in order to
start a “manual” defrost cycle, which will begin only if conditions require it.
4.1.5 SWITCHING ON THE COLD ROOM LIGHT
Press the cold room light button
to switch on or switch off the cold room light.
When the light is switched on, the pilot light alongside the button will light up.
4.1.6 STOPPING THE MACHINE
To switch off the machine it is necessary to push POWER
for more than 5 seconds and the DISPLAY
swiches off.
If the machine is to remain switched off for long periods, it is advisable to disconnect it from the power supply mains.
4.1.7 KEYBOARD LOCK
The keyboard has a key lock functionality to prevent unintentional set point changes by the operator. To lock the keyboard, press
and hold the UP and ESC keys simultaneously. To unlock, press the same keys again.
4.2 ALARMS AND SIGNALS
The control panel is equipped to display error messages (Alarms) using the DISPLAY
and the ALARM led
.
The following is a list of possible messages:
SIGNALS OF ALARM
“ AH1 “
:
High temperature alarm (referring to room probe or probe 1)
“ AL1 “
:
Lew temperature alarm (referring to room probe or probe 1)
“ AH3 “
:
High temperature alarm (referring to probe 1)
“ AL3 “
:
Lew temperature alarm (referring to probe 1)
“ Ad2 “
:
Defrosting time dout
“ EA “
:
External alarm
“ Opd “
:
Door Open Alarm
“ E7 “
:
Master-Slave Communication failure
“ E10 “
:
Clock battery alarm
“ PA “
:
General pressure switch alarm
“ LPA “
:
Minium pressure swich alarm
“ HPA “
:
Maximun pressure swich alarm
Press any button to silence the allarm. The LED will start to blink
SIGNALS OF DEFECT FEELER
“ E1 “ :
Faulty probe 1 (thermostat control)
“ E2 “ :
Faulty probe 2 (evaporator)
“ E3 “ :
Faulty probe 3 (condenser)
- If simultaneous, they will be shown on the display alternately every 2 seconds.
- If E1 or E2 appears on the Master and the display is shared, the slaves will always show the Master display: to understand
which unit is faulty, refer to the alarm LED for each instrument.
4.3 SAFETY PRESSOSTATS
In some machines it is estimated the injection of safety pressostats. This pressostats are installed in the circulation of refrigeration
to reveal low pressure and high pressure. This can be done manually or automatically.
The first ones install themselves automatically based on the state of work of the machine. The second ones have to be installed by
a qualified technician for the reset of the pressostats. The releasing causes of the pressostats are:
- the presence of tube-blocking elements
- the presence of influencing air inside the refrigeration-gas system
Summary of Contents for KUMA
Page 1: ...1 č ...
Page 2: ...2 ...