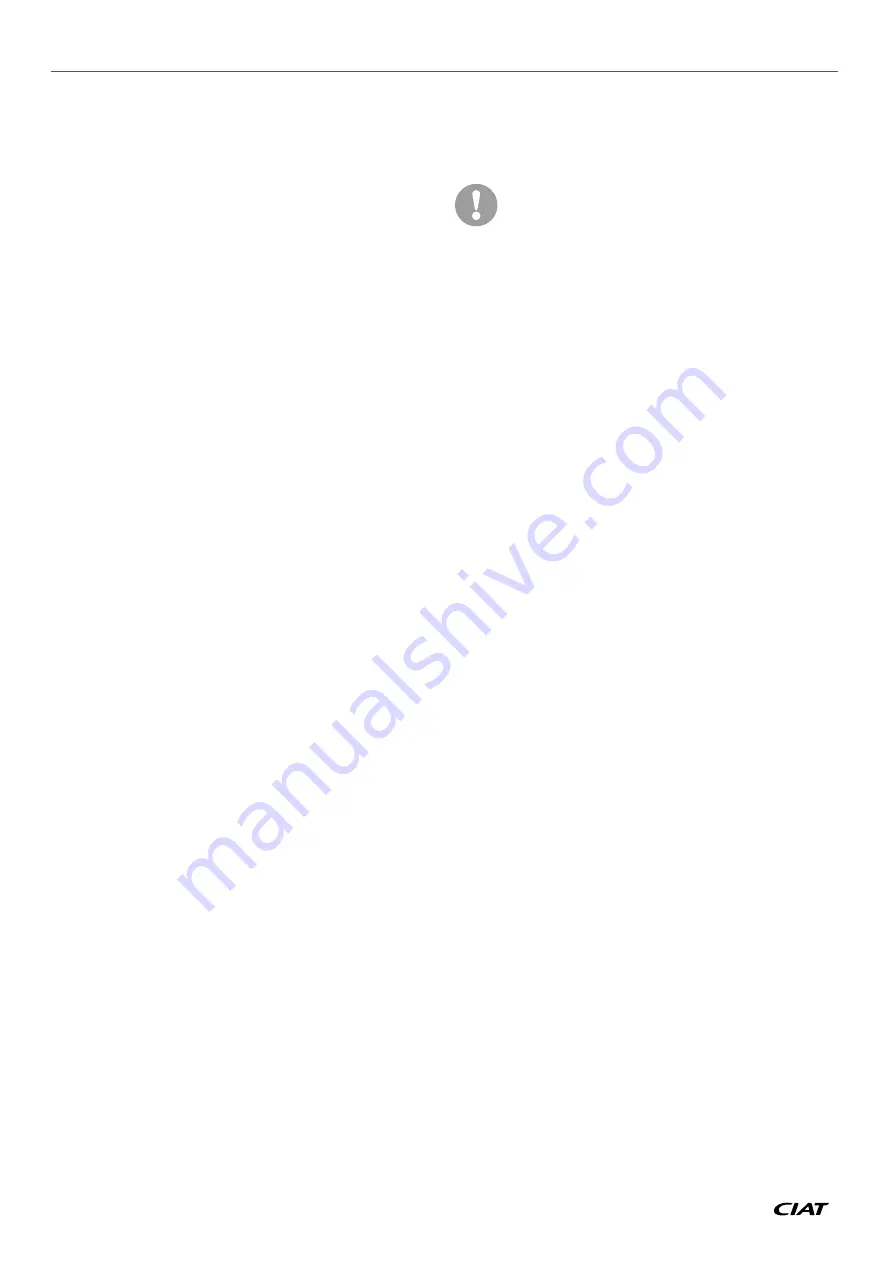
10 - SYSTEM START-UP
10.1 - Checks before system start-up
Before starting up the thermodynamic system, the complete
system, including the thermodynamic system, must be verified
against the installation drawings, dimensional drawings, system
piping and instrumentation diagrams and the wiring diagrams.
All measures must be taken to ensure that the pressure and
temperature limits, specifically those listed on the unit nameplates,
are not exceeded during operation, maintenance and recycling.
Heat exchange fluid temperatures above the maximum
recommended can lead to an increase in the refrigerant pressure
and can cause a loss of refrigerant due to the relief valve discharge.
National regulations must be respected during these checks.
If the national regulation does not specify any details, refer to
standard EN 378 as follows:
External visual installation checks:
- Ensure that the machine is charged with refrigerant. Verify on
the unit name plate that the ‘fluid transported’ is that
recommended for operation, and is not nitrogen.
- Compare the complete installation with the refrigeration system
and power circuit diagrams.
- Check that all documents provided by the manufacturer
(dimensional drawings, pipe and instrument diagram (PID),
declarations, etc.) to comply with the regulations are present.
If any documentation is missing, order a replacement.
- Make sure the environmental safety and protection devices
and arrangements provided by the manufacturer to comply with
the regulations are in place.
- Make sure all declarations of conformity for the pressure
containers, identification plates and documentation required to
comply with local regulations are present.
- Verify the free passage of access and safety routes.
- Comply with the instructions and directives to prevent the
deliberate release of refrigerant fluids.
- Verify the installation of connections.
-
Verify the supports and fixing elements (materials, routing and
connection).
- Verify the quality of welds and other joints.
- Check the protection against mechanical damage.
- Check the protection against heat.
- Check the protection of moving parts.
- Verify the accessibility for maintenance or repair and to check
the piping.
- Verify the status of the valves.
- Verify the quality of the thermal insulation.
- Check the condition of 400 V cable insulation.
10.2 - Commissioning
Always ensure you have read and fully understood the operating
instructions for the units before starting up the unit, and ensure
the following precautions have been taken:
-
Check the heat-transfer fluid circulation pumps, the air handling
equipment, and any other equipment connected to the heat
exchangers.
- Refer to the manufacturer’s instructions.
- Refer to the electrical diagram delivered with the unit.
- Ensure there are no refrigerant leaks. Check the tightening of
the fastening clips on all the pipes.
- Check the power supply at the main connection point and the
order of phases.
-
For units without the factory-fitted hydraulic module option,
the installer is responsible for heat protection and the
connections relating to the installation's pump.
-
Check that the compressor crankcase heaters, and the
compressor head heaters if applicable, have been energised
for 6 hours before starting up the system.
- Open the suction shut-off valves on each circuit for the
corresponding units.
Commissioning and start-up must be supervised by a
qualified technician.
-
The system must have a heat load and water
flowing in the exchangers when it is started up and
tested.
-
All setpoint adjustments and control tests must be
carried out before the unit is started up.
-
Refer to the Service guide.
Proceed with the unit commissioning.
Make sure all safety devices are operational, and
especially that the high pressure switches are
engaged and that any alarms have been cleared.
NOTE:
If the manufacturer's recommendations (system, water and
power connections) are not observed, no claims made under
the warranty will be accepted.
10.3 - Essential points to check
Compressors
Ensure that each compressor is rotating in the correct direction,
checking that the discharge temperature rises quickly, the high
pressure increases and the low pressure drops. If it is rotating in
the wrong direction, the power supply is incorrectly wired (reversed
phases). To ensure rotation in the correct direction, swap two power
supply phases.
- Check that the power cables are tightened securely in the
terminal unit for each compressor
- Check the compressor discharge temperature using a contact
sensor
- Check that the input current is normal
- Check all safety devices to make sure they operate correctly
Hydraulic
As the exact total system pressure drop is not known at start-up,
adjust the water flow rate with the control valve until the desired
nominal rate is obtained.
Please refer to the chapter “Nominal system water flow rate control -
Procedure for adjusting the flow rate” for the steps to follow.
In any case, the hydraulic circuit must be free from pollution
(removal of any solid particles in the circuit) before start-up: Please
refer to the chapter “Nominal system water flow rate control -
Procedure for cleaning the hydraulic circuit” for the steps to follow.
Refrigerant charge
Each unit is shipped with an exact charge of refrigerant and oil.
Check that there are no visible refrigerant or oil leaks:
-
No apparent damage on the refrigerant circuit pipes (no trauma,
cracks, deformation)
- No traces of grease on the connections and refrigerant circuit
sensors
In case of doubt, use a refrigerant leak detection device suited to
the fluid in the unit.
AQUACIAT
POWER
™ LD/ILD
EN-46
Summary of Contents for AQUACIAT POWER LD 1100R
Page 1: ...AQUACIAT POWER LD 602R 3500R ILD 602R 2000R 12 2021 10590 Instruction manual...
Page 81: ...EN 81 AQUACIATPOWER LD ILD...
Page 82: ......
Page 83: ......