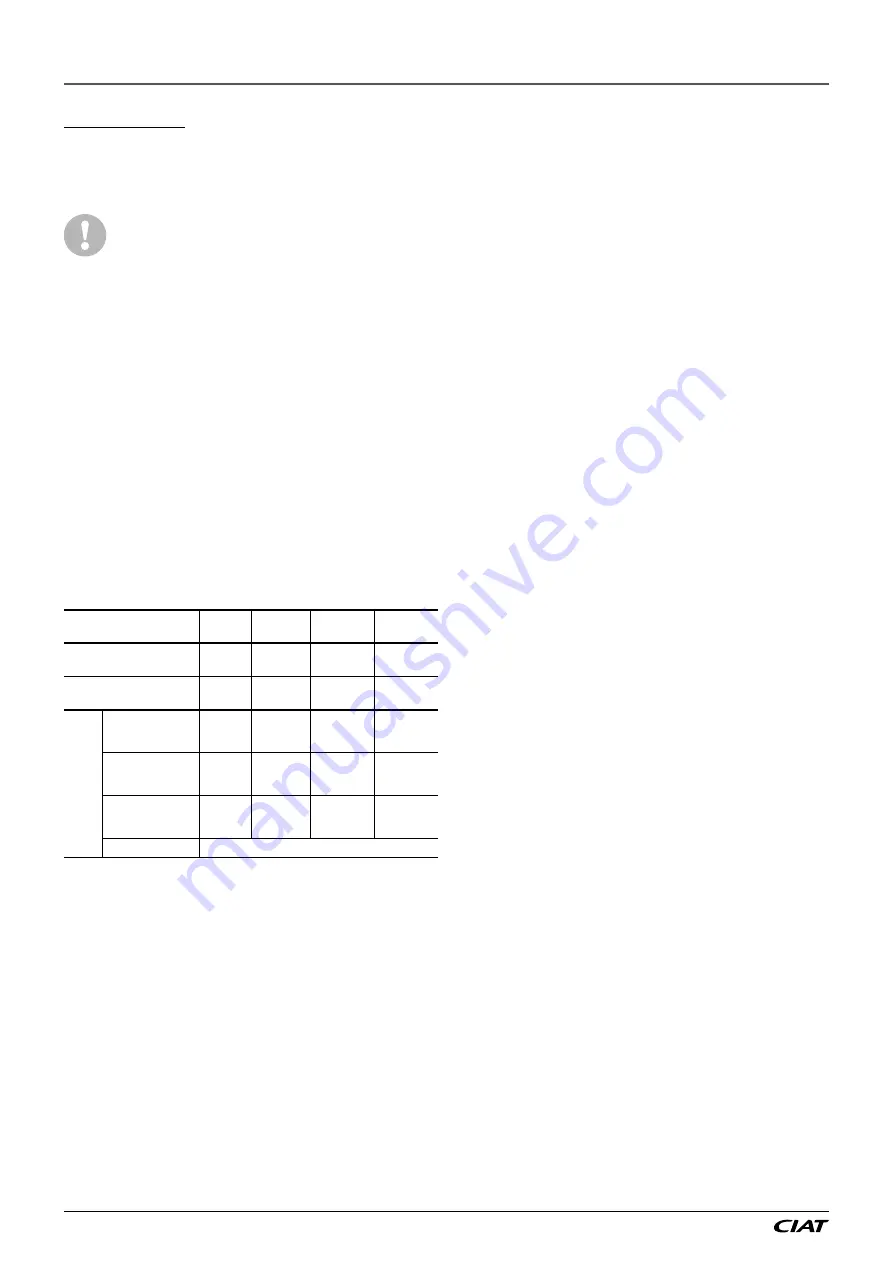
Operating checks:
Important: This product contains fluorinated greenhouse
gas covered by the Kyoto protocol.
Type of fluid: refer to the nameplate.
Global Warming Potential (GWP): refer to the table below:
►
All interventions on this product's refrigerating circuit
must be performed in accordance with applicable
legislation. Within the European Union, this
legislation notably includes regulation No. 517/2014,
known as F-Gas.
►
Ensure that refrigerant is never released to the
atmosphere when the equipment is installed,
maintained or sent for disposal.
►
It is prohibited to deliberately release refrigerant into
the atmosphere.
►
If a refrigerant leak is detected, ensure that the leak
is repaired quickly.
► Only certified, qualified personnel are permitted to
install, service and perform sealing tests on the
refrigerant, decommission the equipment and
recover the refrigerant.
►
The operator must ensure that any refrigerant
recovered is recycled, regenerated or destroyed.
►
The operator is bound by the obligation to perform
sealing tests, or have these performed, at regular
intervals.
►
Regulations within the European Union have set the
following intervals:
System WITHOUT leakage
detection
No test
12 months
6 months
3 months
System WITH leakage
detection
No test
24 months 12 months
6 months
Refrigerant charge per
circuit (equivalent CO
2
)
< 5 tonnes 5 ≤ charge
< 50 tonnes
50 ≤ charge
< 500 tons
Charge >
500 tons
(1)
Refrigerant charge per
circuit (kg)
R134a
(GWP 1430)
Charge <
3.5 kg
3.5 ≤
charge <
34.9 kg
34.9 ≤
charge <
349.7 kg
charge >
349.7 kg
R407C
(GWP 1774)
Charge <
2.8 kg
2.8 ≤
charge <
28.2 kg
28.2 ≤
charge <
281.9 kg
charge >
281.9 kg
R410A
(GWP 2088)
Charge <
2.4 kg
2.4 ≤
charge <
23.9 kg
23.9 ≤
charge <
239.5 kg
charge >
239.5 kg
HFOs: R1234ze
No requirement
(1) From 01/01/2017, units must be equipped with a leak detection system.
►
For all equipment subject to regular sealing tests,
the operator must keep a log used to record the
following: the quantities and types of fluids contained
in the system (added and recovered), the quantity
of fluid recycled, regenerated or destroyed, the date
and results of the sealing tests, the details of the
technician and of the company performing the work,
etc.
►
Contact your local dealer or installer if you have any
questions.
Information on operating inspections given in EN 378 standard
can be used when similar criteria do not exist in the national
regulation.
Check regularly for leaks and, if detected, have these repaired
immediately.
1.3 - Installation safety considerations
After the unit has been received, and before it is started up, it
must be inspected for damage. Check that the refrigerant circuits
are intact, especially that no components or pipes have shifted
or been damaged (e.g. following a shock). If in doubt, carry out
a leak tightness check.
Pressure equipment and components
These products include pressure equipment or components
manufactured by the unit manufacturer or by other manufacturers.
We recommend that you contact your professional body to find
out which regulations affect you as the operator or owner of
pressure equipment or components (declaration, re-qualification,
re-testing). The characteristics of this equipment/these
components are given on the nameplate or in the required
documentation, supplied with the products.
These units comply with the European Pressure Equipment
Directive.
The units are intended to be stored and operated in an
environment where the ambient temperature does not drop below
the minimum allowable temperature indicated on the nameplate.
Do not introduce significant static or dynamic pressure with
regard to the operating pressures used during operation or for
tests in the refrigerant circuit or in the heat exchange circuits.
NOTE:
Monitoring during operation, re-qualification, re-testing,
exemption from re-testing:
-
Follow the regulations on monitoring pressurised equipment.
-
The user or operator is usually required to create and maintain
a monitoring and maintenance log.
-
In the absence of any regulations, or in addition to the
regulations, follow the guidance in EN 378.
-
Follow the local professional recommendations, whenever
they exist.
-
Regularly monitor the surface of the components to detect
cavernous corrosion. To do this check an uninsulated part of
the pressure vessel or at a joint in the insulation.
Regularly check for the presence of any impurities (e.g. sand,
grit) in the heat transfer fluids. These impurities can cause
wear and/or pitting corrosion.
Filter the heat transfer fluid and perform internal visits and
inspections as described in EN 378
Reports from the periodical checks by the user or the operator
must be added to the monitoring and maintenance register.
1 - INTRODUCTION
AQUACIAT
POWER
ILD
EN-6