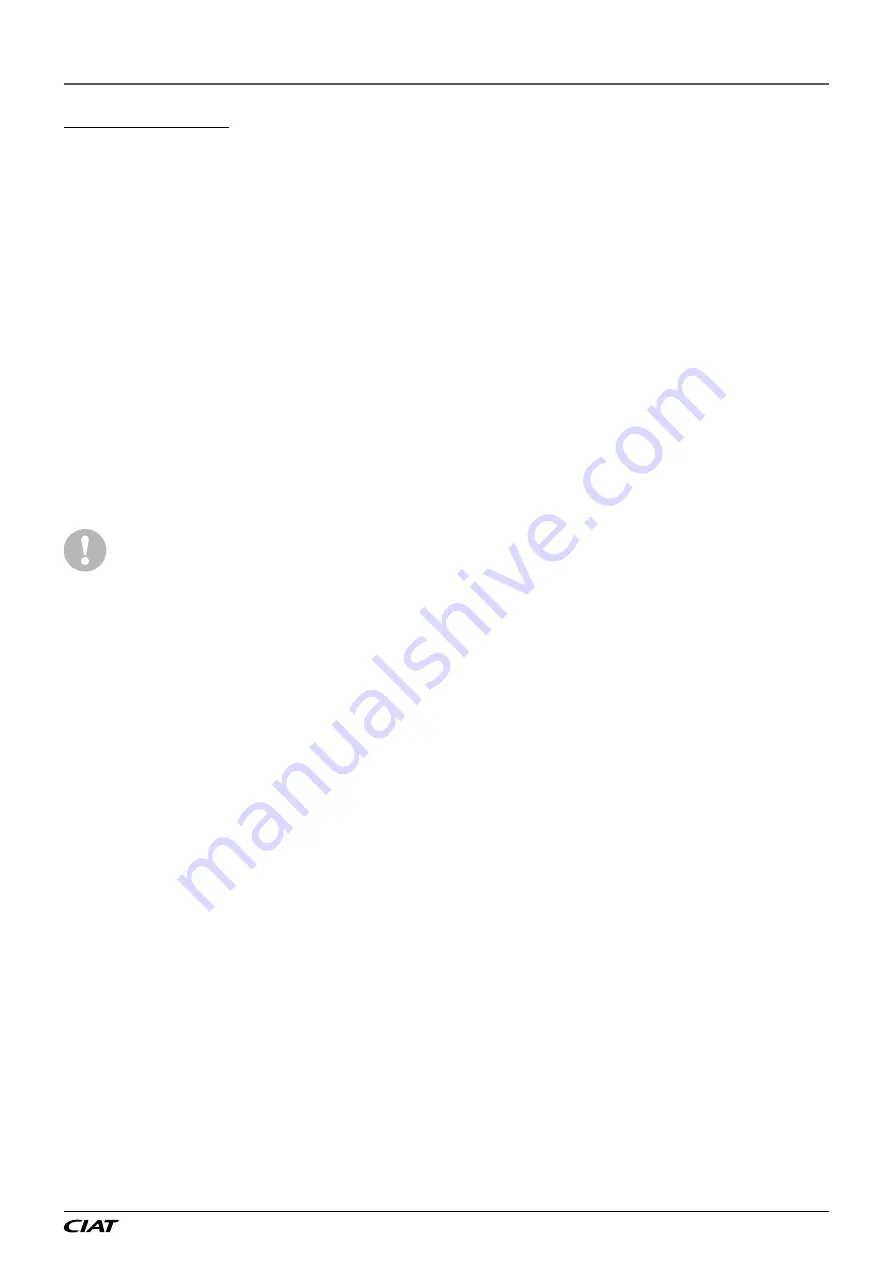
1 - INTRODUCTION
Protective device checks:
If no national regulations exist, check the protective devices on
site in accordance with standard EN378: once a year for the high
pressure switches, every five years for the external relief valves.
The company or organisation that conducts a pressure switch
test must establish and implement detailed procedures for:
-
Safety measures,
-
Measuring equipment,
-
Values and tolerances for cut-off and discharge devices,
-
Test stages,
-
Recommissioning of the equipment.
The principle for performing a test without disassembly of the
pressure switch is given here, however the manufacturer
recommends contacting the Service for this type of test:
-
Verify and record the setpoints of pressure switches and
external relief devices (valves and possible rupture disks),
-
Be ready to switch off the main disconnect switch of the power
supply if the pressure switch does not trigger (avoid over-
pressure or excess gas if there are valves on the high pressure
side on the recovery air exchangers, for example),
-
Connect a calibrated pressure differential gauge with integral
damping (oil bath with pointer if mechanical); instantaneous
reading gauges may give inaccurate readings because of the
control's scanning delay,
-
Carry out the HP quicktest built into the control (refer to the
Service Guide).
If the test results in the replacement of the pressure
switch, it is necessary to recover the refrigerant
charge; these pressure switches are not installed
on Schrader type automatic valves.
If the machine operates in a corrosive environment, inspect the
protection devices more frequently.
Do not attempt to repair or recondition a valve if there has been
any corrosion or build-up of foreign material (rust, dirt, scale,
etc.) on the valve body or mechanism. In this case, it must be
replaced.
Do not install relief valves in series or backwards.
1.2 - Refrigerant safety considerations
Use safety goggles and safety gloves.
All precautions concerning handling of refrigerant must be
observed in accordance with local regulations.
If a leak occurs or if the refrigerant becomes contaminated (e.g
by a motor short circuit or BPHE freeze-up), and before any
intervention, remove the complete charge using a recovery unit
and store the refrigerant in mobile containers. The compressors
cannot transfer the whole refrigerant charge and can be damaged
if used to pump-down. The refrigerant charge should not be
transferred to the high-pressure side.
Detect and repair the leak, check the type of refrigerant in the
machine and then recharge the machine/circuit with the total
charge, as indicated on the unit nameplate. Do not top up the
refrigerant charge. Only charge the liquid refrigerant given on
the nameplate at the liquid line.
Charging any refrigerant other than the original type will impair
machine operation and can even cause irreparable damage to
the compressors. The compressors operating with this refrigerant
type are lubricated with a synthetic polyolester oil.
Do not unweld the refrigerant pipework or any refrigerant circuit
component or cut these with a torch until all refrigerant (liquid
and vapour) as well as the oil have been removed from the unit.
Traces of vapour should be displaced with dry nitrogen.
Refrigerant in contact with an open flame produces toxic gases.
Do not siphon refrigerant.
Any accidental release of refrigerant, whether this is caused by
a small leak or significant discharges following the rupture of a
pipe or an unexpected release from a relief valve, may cause
any personnel exposed to experience heart palpitations,
faintness, frostbite and burns. Always take any such event
seriously.
Installers, owners and especially service engineers for these
units must:
-
Create a procedure to ensure medical attention is sought
before treating any symptoms;
-
Provide first aid equipment, flush the eyes and skin
immediately if splashed with refrigerant, and seek medical
attention.
We recommend to apply standard EN 378-3 Annex 3.
Ensure there is sufficient ventilation if the unit is installed in an
enclosed area. In gas form, refrigerant is heavier than air and,
if allowed to accumulate in a confined area, it can reduce the
quantity of oxygen in the air, causing respiratory issues.
The refrigerant used in units in this range is R410A, a high-
pressure fluid (the operating pressure of the unit is greater than
40 bar).
Special equipment must be used when working on the refrigerant
circuit (pressure gauge, charge transfer equipment, etc.).
Do not clean the unit with hot water or steam. This may cause
the refrigerant pressure to rise.
NOTE:
If a liquid line valve is present, never leave refrigerant in
liquid form between this closed valve and the expansion valve
as the change in temperature may cause the liquid to expand,
rupturing this section of the circuit. This valve is situated on the
liquid line before the filter drier.
Never apply an open flame or pressurised steam to a refrigerant
container. Dangerous overpressure can result. If it is necessary
to heat the refrigerant, only use hot water.
The standard NF E29-795 describes the regulations permitting
conditioning and recovery of halogenated hydrocarbons under
optimum quality conditions for the products and optimum safety
conditions for people, property and the environment. If any
damage is caused to the equipment, the refrigerant must be
changed in accordance with this standard, or an analysis of the
fluid must be performed by a specialist laboratory.
Any refrigerant transfer and recovery operations must be carried
out using a transfer unit.
Service valves are positioned on the liquid, suction and discharge
lines and are available on all units for connection to the transfer
unit.
The units must never be modified to add refrigerant and oil
charging, removal and purging devices. These units have the
required openings. Refer to the certified dimensional drawings.
It is dangerous and illegal to re-use disposable (non-returnable)
cylinders or attempt to refill them. When the cylinders are empty,
evacuate the remaining gas pressure, fill out the relevant
paperwork and hand them over to an approved recovery agency.
Do not incinerate.
EN-5
AQUACIAT
POWER
ILD