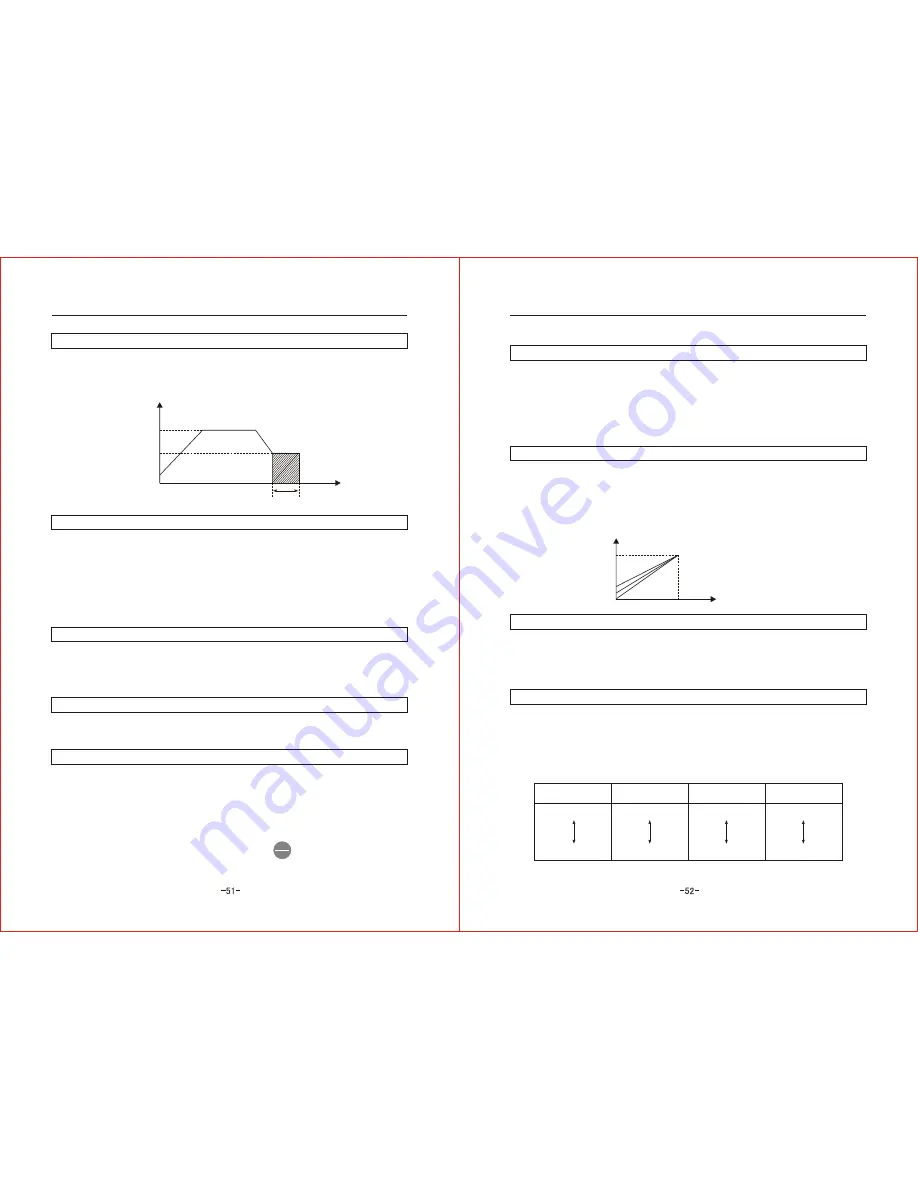
F004
F005
0
1.0KHz
10.0KHz
Special Function
F082 AVR Function Setting Range: 0~1 Factory Setting: 1
F082=0: Ineffective.
F082=1: Automatically stabilized the voltage.
Function Instruction: Such function is used to set the Inverter's voltage-stabilization
function.
Note: When F082=1 and input voltage > or = output voltage set value, AVR function will
ensure output voltage constant. When F082=1, input voltage < output voltage set
value, output voltage =input voltage
F083 Torque Hoisting Setting Range: 0~30% Factory Setting: 4%
Function Instruction: Such function is used to improve t he torq ue char acter w hen the
Inverter is operated in low frequency, through adjusting the output
voltage of the
I nverter, it can improve the output moment in the operation in low frequency. If the
set value is to large, the Inverter will come out jump fault.
Note: When the torque hoisting is set to 0, the torque hoisting will be ineffective, the
Inverter will be operated according to the set val ue of V/F curve, otherw ise V/F
curve set will be ineffective.
Voltage
Frequency
F084 Slip Compensation Setting Range: 0.0~5.0HZ Factory Setting: 0.0HZ
Function Instruction: Such function is used to set the rated compensation frequency
value of the slip compensation. When load of motor increases, its rotational speed
will be down. The aim of slip compensation is to adjust output frequency to compen
sate the reduced rotational speed, to make motor reach synchronizing speed more,
when the set value is 0.0, the slip compensation will not act.
F085 Carrier Wave Frequency Setting Range: 1~12KHz Factory Setting: 5
Function Instruction: The higher the carrier wave frequency is, the more perfect the
current waveform will be, the lower the motor noise will be, th e smaller the tor que
on low frequency will be, the larger electromagnetism disturbance will be, the larger
main element loss will be, the larger Inverter fever will be, the larger leakage
current will be, the lower the efficiency will be. The lower carrier wave frequency is,
it will be reverse.
Carrier Wave Frequency abridged general view is as below:
Carrier Wave
Frequency
Electromagnetism
Noise
Disturbance,
Leakage Current
Fever Value
Large
Small
Small
Large
Small
Large
Note: Carrier wave of Inverter above 30KW is factory set to 3.
F077 DC Operation Torque Setting Range: 0~30% Factory Setting: 4%
Function Instruction: Such function is used to se
t the braking torque after in DC braking
to ensure to make the motor fully stop in braking time.
Note: If DC braking torque is set to high, the Inverter will easily stop. Increase it slowly
when setting the braking torque.
Output Frequency
Operation Frequency
DC Braking Start Frequency
Time
DC Braking Time
Counter Function
F078 Count Mode Setting Range: 0~2 Factory Setting: 0
F078=0: Count function is ineffective.
F078=1: Count function is effective, upward count mode.
F078=2: Count function is effective, downward count mode.
Function instruction: When choosing count function is effective (F078=1 or F078=2),
count pulse is input by multi-function (X1~X4), X1~X4 multi-function terminal must
have one of which to choose pulse input function (details are in function code F093
~F096 function choice), otherwise this function will be ineffective.
F079 Count Value Setting Range: 0~9999 Factory Setting: 1
Function Ins truction: Such function is used to set the counter's default value, if choosing
upward count way, when count value is equal to the default value, it will stop count
and execute coun t to treatment action. If choosing downward count way, when count
value is 1, it will stop count and execute count to treatment action.
F080 Count Unit Setting Range: 0~9999 Factory Setting: 1
Function Instruction: Such function is used to set the unit value of each count pulse and
could count relevant object.
F081 Count to Treatment Setting Range: 0~3 Factory Setting: 0
F081=0: Stop count and close output.
F081=1: Stop count and continue output.
F081=2: Restart count and stop output.
F081=3: Restart count and continue output.
Function Ins truction: Such function is used to choose the action when the counter count
to time.
Note: Counter Zero Clearing Operation please press .
Article6 Function parameter illustration
Article6 Function parameter illustration
STOP
RESET