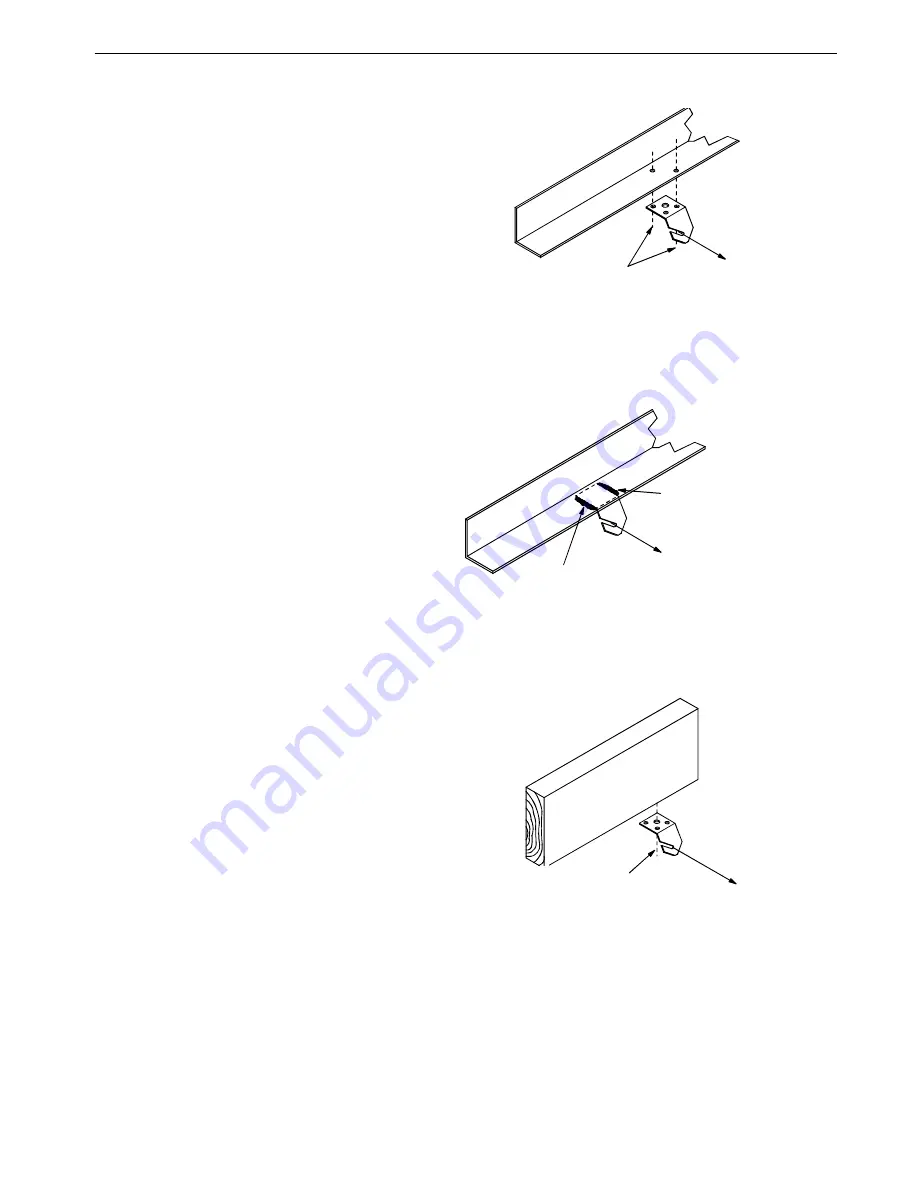
LIBERTY® Feeding System with Electronic Sensor (ES)
Installing the Suspension System
13
Ceiling Hook Installation
The ceiling hook may be used in a variety
of installations. Depending on your
ceiling or rafter type, install the Ceiling
Hooks as shown in
17
.
Steel Truss Installations
Wood Truss Installations
1523-80 4/2002
Secure Ceiling Hook to truss
using self-drilling screws
through opposite holes
Cable Travel
Figure 14.Steel Truss Ceiling Bracket Installation
1523-78 4/2002
Cable Travel
Weld Ceiling Bracket
to truss here
Weld Ceiling Bracket
to truss here
Figure 15.Welded Steel Truss Ceiling Bracket Installation
Figure 16.Wood Truss Ceiling Bracket Installation
1523-79 4/2002
Secure Ceiling Bracket to truss
using a 1/4" lag screw (not supplied)
through the center hole
Cable Travel