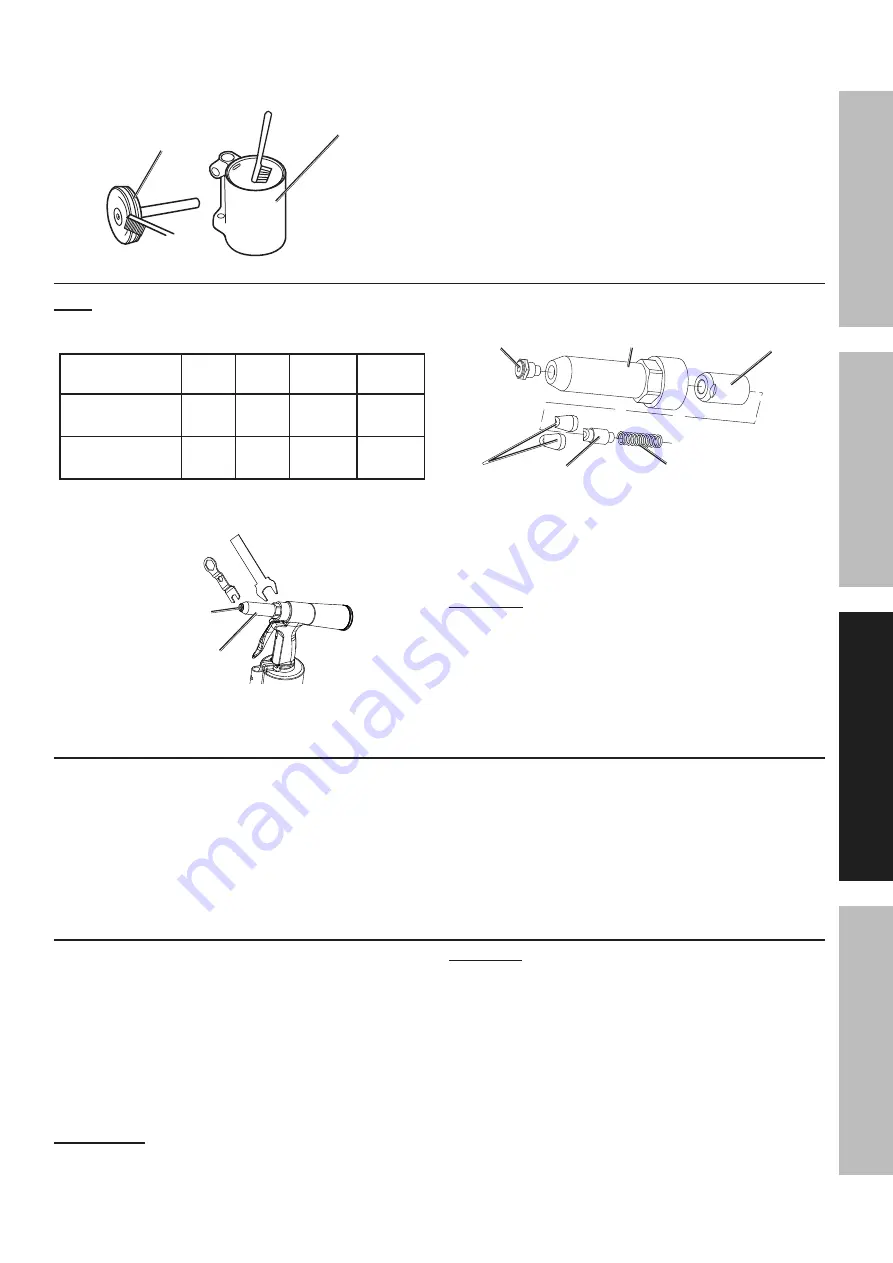
Page 11
For technical questions, please call 1-888-866-5797.
Item 64518
Sa
FE
ty
Op
Era
ti
O
n
Maint
Enanc
E
SE
tup
5. Apply silicone based grease (not included)
to the inner wall of the Air Cylinder
and the Piston Head O-Ring.
piston Head
O-ring
air cylinder
6. Replace the Piston Head.
configuring For rivet Size:
note:
Tool comes with a 1/4″ (1A) Nosepiece
with its appropriate matched hardware
installed as shown in the table below.
nosepiece
Jaw
case
Jaws
Jaw
pusher
pusher
Spring
1/8" (1E)
5/32" (1D)
6-1A
7A
8A
10-1
3/16" (1C)
1/4" (1A)
6-1
7
8
10
1. Use the included Wrenches to remove
the Nosepiece and Outer Cylinder.
Outer
cylinder
nosepiece
2. Unscrew the Jaw Case from the Jaw Cylinder.
3. Remove the Jaw Pusher and Jaws from the Jaw
Case, and remove the Spring from the Jaw Cylinder.
nosepiece (1) Outer cylinder (11)
Jaw case (6)
Jaw (7) Jaw pusher (8) Spring (10)
4. Reassemble with the correct hardware to
match the selected Nosepiece size. When
reassembling the Jaw Case, line up the
wedge on the Jaw Pusher’s head in-between
the Jaws, pushing them slightly apart.
important:
When reassembling the Jaw Case,
line up the wedge on the Jaw Pusher’s head
in-between the Jaws, pushing them slightly
apart. Reference steps 7 through 10 in the
User-Maintenance Instructions on page 12.
Workpiece and Work area Set up
1. Work areas must be clean and well-lit.
Do not allow access by children or pets
to prevent distraction and injury.
2. Route the air hose to the work area to
minimize tripping hazards, hose damage,
etc. The air hose must be long enough to
allow free movement while working.
3. Secure loose workpieces using a vise or clamps
(not included) to prevent movement while working.
4. Remove hazardous objects (such as utility lines or
foreign objects) that present a hazard while working.
General Operating instructions
1. If an automatic oiler is not used, add a few drops of
Pneumatic Tool Oil to the airline before use, with a
few drops more after each hour of continual use.
2. Screw the Pin Cap onto the Riveter Housing
and tighten firmly. Turn the slot in the Pin Cap
upward to avoid spilling used rivet pins.
3. Depending on the rivet pin size, install the
correct hardware for that rivet size as described
above under
configuring For rivet Size:
.
iMpOrtant:
When drilling rivet holes in a
workpiece, use the same diameter drill bit as
the outer diameter of rivet being used.
cautiOn!
Verify the work surface has
no hidden utility lines before drilling.
4. Attach an air hose to the Air Inlet of the Riveter.
5. Turn on the air compressor, and set its regulator to
the needed pressure.
Do not exceed the tool’s
maximum air pressure rating.
6. Insert the small end of a rivet fully through
the Nosepiece.
cautiOn! Keep clear of
the trigger when inserting rivets.
7. Insert the rivet through the predrilled
hole in the workpiece.