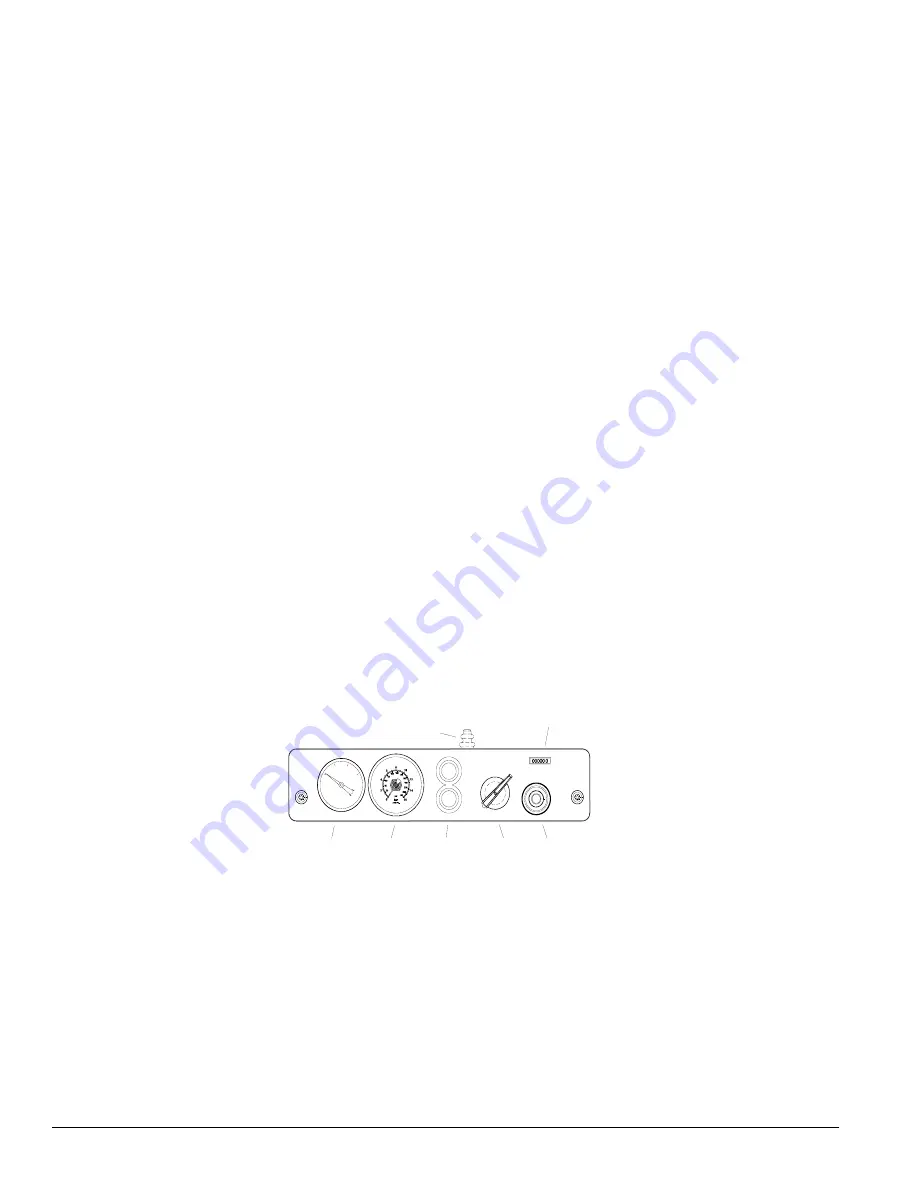
18
1310 3012 08
3.2 Before Starting
f
If the compressor is to be connected to a common compressed air system, fit an appropriate check valve between
compressor outlet and air system. Observe the right mounting position/direction!
1.
Before initial start-up, prepare battery for operation if not already done. See section 4.7.
2. With the compressor standing level, check the level of the engine oil. Add oil, if necessary, to the upper mark on dipstick.
Consult the Engine Operation Manual for the type and viscosity grade of the engine oil.
3. Check the level of the compressor oil. The pointer of oil level gauge (OLG- Fig. 2.3) should register in the green range. Add
oil if necessary. See section 4.3 for the oil to be used.
4. Check that the fuel tank contains sufficient fuel. Top up, if necessary. Consult the Engine Operation Manual for the type of
fuel.
5. Check coolant level in overflow bottle. Top off coolant if necessary. Consult engine’s operation manual for water/coolant
specifications.
6. Drain any water and sediment from the fuel filter until clean fuel flows from the drain cock.
7. Press vacuator valve (VV- Fig. 2.3) of the air filter to remove dust.
8. Check the air filter service indicator (VI- Fig. 2.3). If the red part shows completely, service or replace the filter element. Reset
the indicator.
9. Open an air outlet valve (AV-fig. 2.2) to allow air flow to the atmosphere.
3.3 Starting/Stopping (See Fig. 3.3)
Before starting, first operate the circuit breaker button (Fl) located on the back of the control panel cover. To start, the start button
is turned clockwise to position 1, lamp H2 (general alarm) will go on and the preahest relay K5 will be energized. If needed, press
button S4 to activate the K5 Relay and the glow plugs (HTR). The button should be held in this position for 10 to 15 seconds to
allow for proper pre-heating of the cylinders. Holding glowplug button for more than 60 seconds can cause damage to the engine.
When the button is turned further to position 3, the starter motor will set the engine in motion. Lamp H2 will go out as soon as the
engine has been started. The start button automatically springs back to position 1.
Make sure one discharge valve is opened at time of start-up to regulate engine speed at higher rpm for proper warm-up –
stay out of path of discharge valve during process.
Lamp H1 only produces a signal when the compressor outlet temperature is too high Shutting-down is simply done by turning the
start button counter clockwise to position 0 (with valves closed).
During operation, the canopy must remain closed and can only be opened for short periods.
F1
Fuse reset (Circuit breaker) located inside the unit on the control panel’s cover
H1 Temperature alarm (red)
H2 General alarm (red)
PG Working pressure gauge
P1 Hour meter
P2 Fuel gauge
S1 Contact switch (engine ignition)
S4 Preheat
button
P1
PG
H1,H2
S1
S4
P2
E
F
1/2
F1
Fig. 3.3 Control panel
The control panel in addition indicates receiver pressure (PG) and accumulated operating hours (P1).
Fault situations and protective devices:
—
The starter motor is protected against attempts to start when the unit is already running.
—
A fault which occurs with the engine, either: engine oil pressure (too low), compressor oil temperature (too high), engine
coolant (too high) or alternator voltage (too low) will always and immediately cause the engine to cut out and the control lamp H2
will go on. By doing some simple checks, it can be determined what it was that caused the engine to fail: low oil level, clogged-up
cooler, slack alternator belt tension or broken belt.
—
When the outlet temperature of the element becomes too high, a thermocontact will also switch off the unit immediately.
Both control lamp H1 and H2 will go on. Both control lamps will remain on until the unit has been restarted (start button to position
3) or the contact is turned off (start button to position 0): also when, due to cooling off, the thermocontact has closed again (=
memory function).