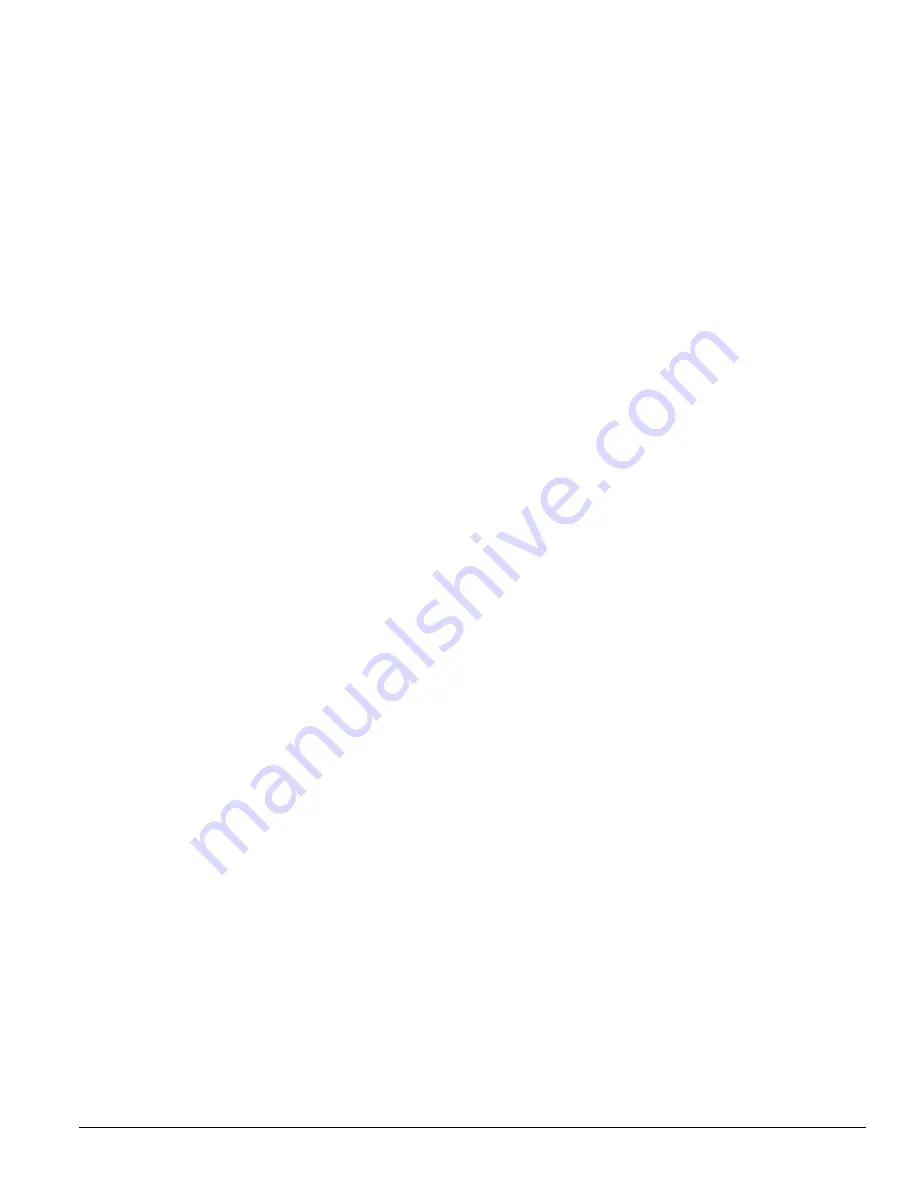
1310 3012 08
9
2 Leading
Particulars
2.1 Description of Safety Pictograms Used in this Manual
f
This symbol draws your attention to dangerous situations. The operation concerned may endanger persons and
cause injuries.
+
This symbol is followed by supplementary information.
Fig. 2.1 General view of CPS 185 PD7
2.2 General
Description
The CPS 185 is a silenced, single-stage, oil-injected screw compressor, built for anl effective working pressure of 100 psi (7 bar).
— Engine
The compressor is driven by a water-cooled diesel engine. The engine’s power is transmitted to the compressor through a flexible
coupling.
— Compressor
The compressor casing houses two screw-type rotors, mounted on ball and roller bearings. The male rotor, driven by the engine,
drives the female rotor. The male rotor has four lobes and the female rotor has six flutes. Thus, the male rotor revolves at 1 1/2
times the speed of the female rotor. The element delivers pulsation-free air.
Injected oil is used for sealing, cooling and lubricating purposes.
—
Compressor Oil System
The oil is boosted by air pressure. The system has no oil pump.
The oil is removed from the air, in the air/oil vessel first by centrifugal force, second through the oil separator element. The vessel
is provided with an oil level indicator.
— Regulation
The compressor is provided with a continuous regulating system and a blow-down valve which is integrated in the unloader
assembly. The valve is closed during operation by outlet pressure of the compressor element and opens by air receiver pressure
when the compressor is stopped.
When the air consumption increases, the air receiver pressure will decrease and vice versa.
This receiver pressure variation is sensed by the regulating valve which, by means of control air to the unloader and engine speed
regulator, matches the air output to the air consumption. The air receiver pressure is maintained between the pre-selected working
pressure and the corresponding unloading pressure.
— Cooling
System
Engine and compressor are provided with a radiator and oil cooler. The cooling air is generated by a fan, driven by the engine.
— Safety
Devices
A thermal shut-down switch protects the compressor against overheating. The air receiver is provided with a safety valve.
The engine is equipped with low oil pressure and high coolant temperature shut-down switches and an alternator/V-belt protection
system.
— Frame
and
Axle
The compressor/engine unit is supported by rubber buffers in the frame.
The standard CPS 185 PD7 is equipped with a non-adjustable drawbar with a towing eye and road lighting.
As an option, the unit can be equipped with electric or hydraulic braking systems.
When driving backwards the hyduralic brake is not engaged automatically.
— Bodywork
The bodywork has openings at the shaped front and rear end for the intake and outlet of cooling air and a specially hinged canopy
for maintenance and service operations. The bodywork is partially lined with sound-absorbing material.
— Lifting
Eye
A lifting eye is accessible through the roof panel at the top of the unit.
— Control
Panel
The control panel grouping the air pressure gauge, control switch etc., is placed at rear of air compressor.
— Data
Plate
The compressor is furnished with a data plate located on the front, drivers side of the unit showing the compressor type, serial
number, maximum final pressure and normal working pressure.