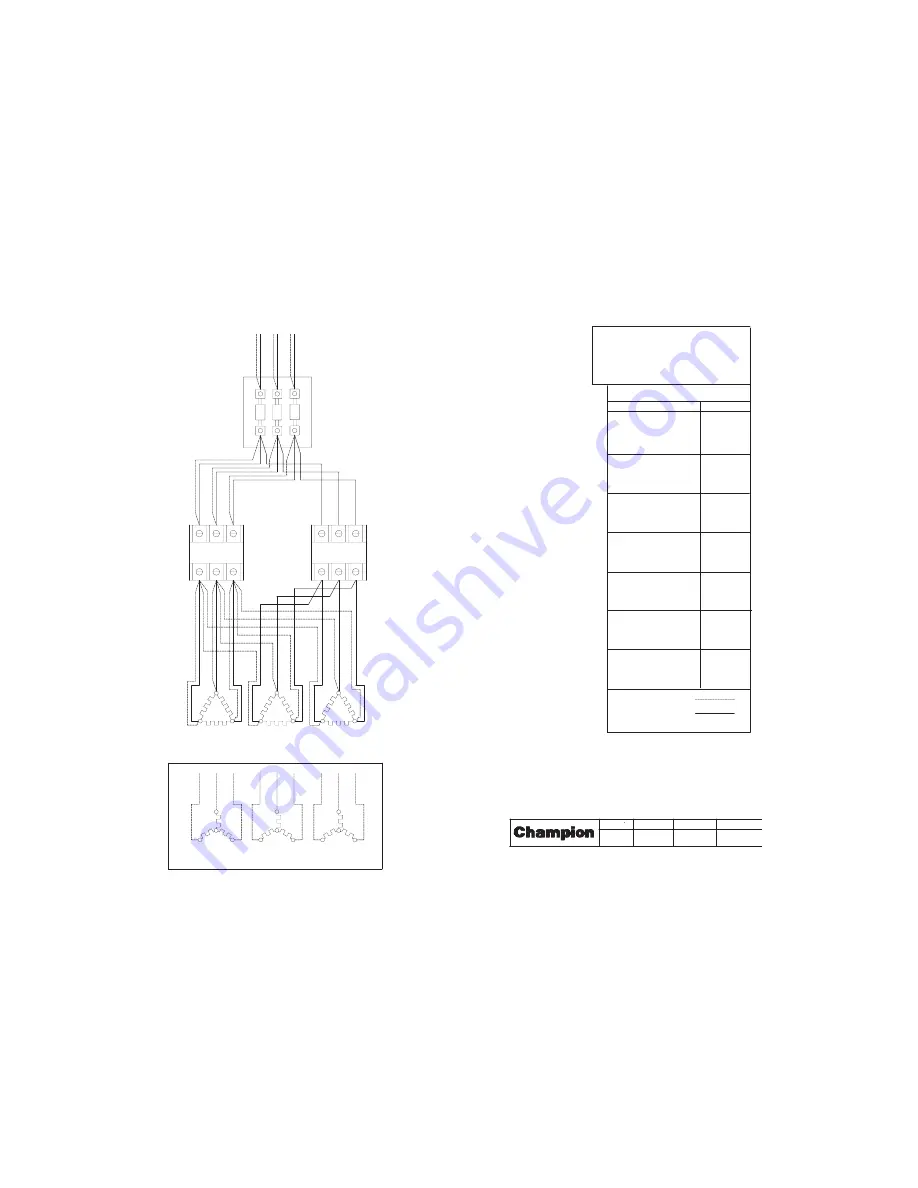
93
92
FUSE BLOCK 1
NOTES
CONTACTOR # 1,2
VOLTAGE 208
HEAT KW/CONTACTOR 9,18
FUSE RATING 100A
FUSE BLOCK # 1
RATING 50A,60A
RATING 50A,60A
FUSE BLOCK # 1
FUSE RATING 100A
VOLTAGE 220
CONTACTOR # 1,2
RATING 60A
FUSE BLOCK # 1
FUSE RATING 60A
VOLTAGE 415
CONTACTOR # 1
9KW
9KW
9KW
CONTACTOR 1
CONTACTOR 2
69
68
67
75
74
73
70
71
72
CANISTER/KW 1/27
L1
L3
L2
CANISTER 1
TOTAL KW
27KW
CONTACTOR # 1,2
VOLTAGE 240
FUSE RATING 90A
FUSE BLOCK # 1
RATING 50A,60A
RATING 50A
FUSE BLOCK # 1
FUSE RATING 50A
VOLTAGE 480
CONTACTOR # 1
380/415/480/575V
208/220/240V
CONTACTOR # 1
VOLTAGE 575
FUSE RATING 45A
FUSE BLOCK # 1
RATING 50A
VOLTAGE 380
CONTACTOR # 1
RATING 60A
FUSE BLOCK # 1
FUSE RATING 60A
73
74
75
9KW
9KW
9KW
67
68
69
70
71
72
"Y" CONNECTION 380/415V ONLY
HEAT KW/CONTACTOR 9,18
HEAT KW/CONTACTOR 9,18
HEAT KW/CONTACTOR 27
HEAT KW/CONTACTOR 27
HEAT KW/CONTACTOR 27
HEAT KW/CONTACTOR 27
ELECTRICAL CODES.
POINT MUST COMPLY WITH ALL LOCAL
ALL POWER SUPPLIED TO EACH CONNECTION
PER ORDER, TO DISCONNECT SWITCH.
VOLTAGE/PHASE/Hz, AS SPECIFIED
CUSTOMER TO SUPPLY RATED
93-01-29
700848/A
HEAT
DATE
NUMBER/REV
MODEL
ELEC
BSTR HEAT
CH-27 PP-28
27KW
Summary of Contents for PP-28 Corner
Page 4: ...REVISION RECORD CONT REVISIONS ii ...
Page 43: ...35 REPLACEMENT PARTS REPLACEMENT PARTS ...
Page 44: ...36 REPLACEMENT PARTS 5 2 5 1 5 4 3 5 5 5 6 9 7 10 11 12 A B A A 8 Figure 22 Panels ...
Page 48: ...40 REPLACEMENT PARTS 2 1 1 3 6 7 3 5 4 A A A 8 9 10 B B B Figure 24 Cable Pulley Assembly ...
Page 50: ...42 REPLACEMENT PARTS 2 3 3 4 8 7 6 5 3 5 5 5 3 9 10 1 11 12 Figure 25 Counterweight System ...
Page 64: ...56 REPLACEMENT PARTS 2 3 6 4 5 1 7 Figure 32 Scrap Screens Baskets ...
Page 75: ...67 REPLACEMENT PARTS THIS PAGE INTENTIONALLY LEFT BLANK ...
Page 83: ...75 REPLACEMENT PARTS THIS PAGE INTENTIONALLY LEFT BLANK ...
Page 84: ...76 REPLACEMENT PARTS 3 5 6 4 5 5 5 1 2 5 3 Figure 40 Side Mount Booster Cabinet ...
Page 86: ...78 REPLACEMENT PARTS 1 2 3 4 7 8 6 9 10 4 11 12 13 5 Figure 41 Pump Assembly ...
Page 88: ...80 REPLACEMENT PARTS 3 4 5 6 7 8 10 1 2 9 11 11 Figure 42 Machine Control Panel ...
Page 94: ...86 REPLACEMENT PARTS 0 1 2 1 2 3 4 6 7 8 5 Figure 45 Vent Fan Control Cabinet Optional ...
Page 98: ...90 THIS PAGE INTENTIONALLY LEFT BLANK ...
Page 99: ...91 ELECTRICAL SCHEMATICS ELECTRICAL SCHEMATICS ...
Page 103: ...98 ...
Page 104: ...99 ...
Page 105: ......