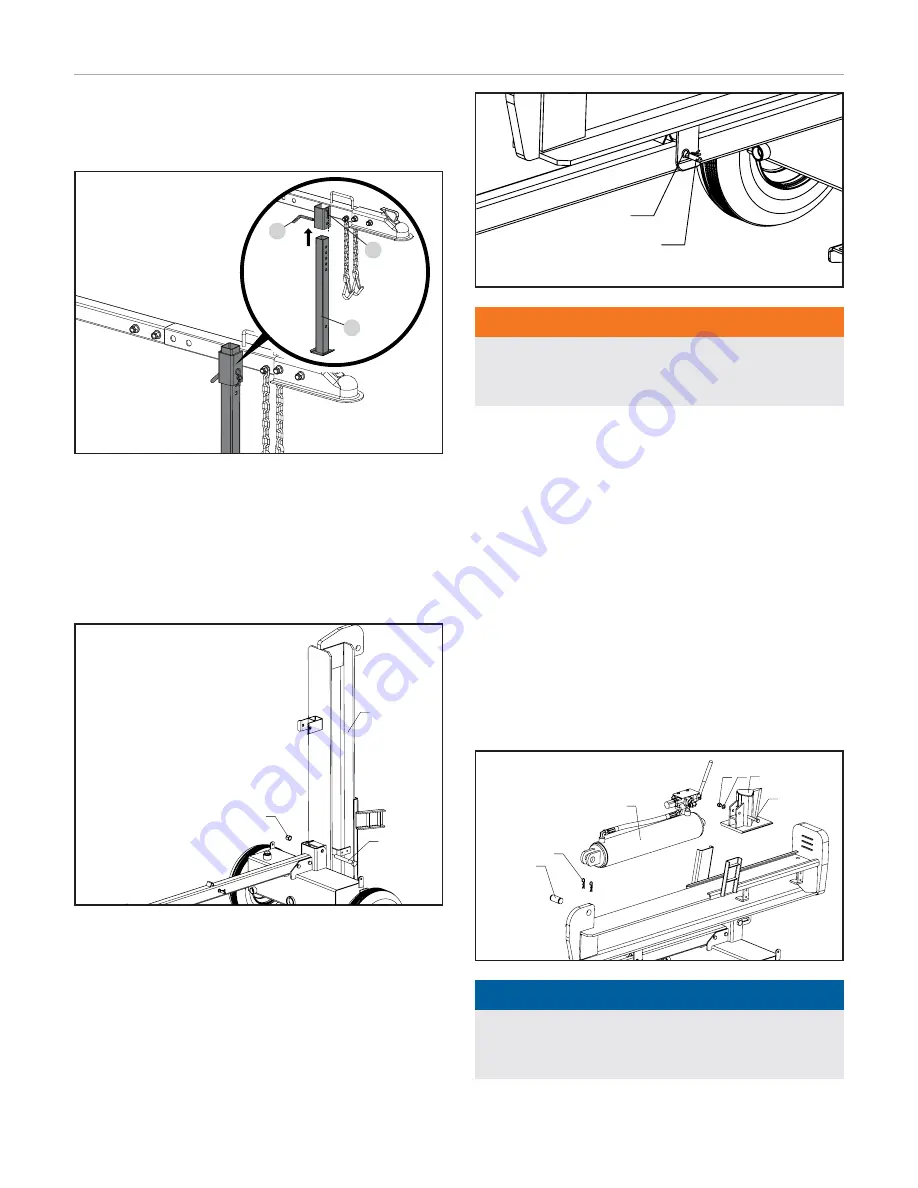
16
100250 - 37 TON FULL BEAM LOg SPLiTTER
ASSEMBLY
4) install the Support Leg
1. Insert the support leg (67) into the leg holder on the tow bar
and secure with pin (66) and R-pin (38).
67
38
66
5) install the Beam
1. Stand the beam (1) vertical on the foot plate.
2. Roll the tank into position so the pivot holes of the tank and
beam are aligned.
3. Insert the bolt (36) and secure it with the lock nut (34).
1
34
36
4. Block the wheels to prevent the frame from rolling.
5. Pivot the beam to the horizontal position and secure it with
the lock pin (37) and R-clip (38) through the tow bar.
38
37
16
2
4
5
3
17
18
WARNiNg
The beam is extremely heavy and should only be handled
with 2 or more people. DO NOT try and lift or handle the beam
without assistance.
6) install the Cylinder and Wedge
1. Slide the wedge (4) under the beam rails. Push it toward the
foot plate to make room for the cylinder (16).
2. Position the cylinder clevis between the mounting plates at
the end of the beam.
3. Align the holes in the cylinder clevis to the holes on the
mounting channels on the beam.
4. Slide the cylinder pin (18) through the mounting channel and
cylinder clevis holes and secure with the two R-clips (17).
5. Align the holes in the cylinder rod end with the holes in the
wedge.
6. Secure the cylinder rod end to the wedge with the bolt (5),
washer (3) and lock nut (2). Tighten, but DO NOT over tighten.
38
37
16
2
4
5
3
17
18
NOTiCE
The cylinder rod may need to be rotated slightly in order to
properly align the wedge. Insert a screwdriver into the bolt
hole in the cylinder rod and slowly rotate as needed.