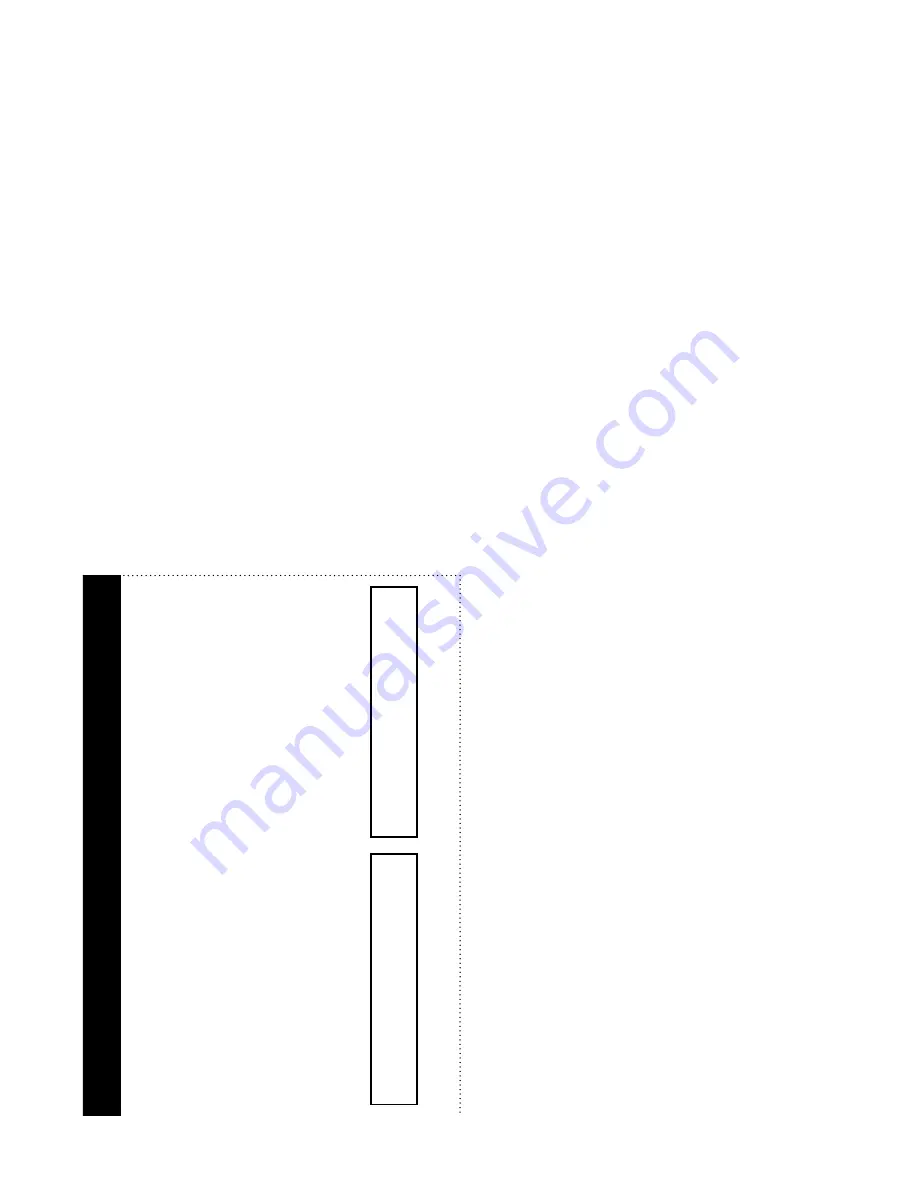
8
"
3
3
"
/
5:
3
&
(
*4
53
"5
*0
/
$
"
3
%
.
0
%
&-
4&
3
*"
-
%
BUF
P
G*O
TUB
MMB
UJP
O@
@@
@@
@@
@@
@@
@@
@@
@@
@@
@@
@@
@
0
X
OF
ST
-
PD
BUJP
O
$
PN
QB
OZ
@@
@@
@@
@@
@@
@@
@@
@@
@@
@@
@@
@@
@@
@@
@@
@@
@@
@@
@@
@@
@@
@@
@@
@@
@@
@@
@@
@@
@
"
EE
SF
TT
@@
@@
@@
@@
@@
@@
@@
@@
@@
@@
@@
@@
@@
@@
@@
@@
@@
@@
@@
@@
@@
@@
@@
@@
@@
@@
@@
@
"
EE
SF
TT
@@
@@
@@
@@
@@
@@
@@
@@
@@
@@
@@
@@
@@
@@
@@
@@
@@
@@
@@
@@
@@
@@
@@
@@
@@
@@
@@
@
5F
MF
QI
PO
F@
@@
@@
@@
@@
@@
@@
@@
@@
@@
@@
@@
@@
@@
@@
@@
@@
@@
@@
@@
@@
@@
@@
@@
@@
@@
@@
$
PO
UB
DU/
BN
F@
@@
@@
@@
@@
@@
@@
@@
@@
@@
@@
@@
@@
@@
@@
@@
@@
@@
@@
@@
@@
@@
@@
@@
@@
@
1
VS
DI
BT
FE
GSP
N
%
FB
MF
S@
@@
@@
@@
@@
@@
@@
@@
@@
@@
@@
@@
@@
@@
@@
@@
@@
@@
@@
@@
@@
@@
@@
@@
@@
@@
@@
@@
@@
5F
MF
QI
PO
F@
@@
@@
@@
@@
@@
@@
@@
@@
@@
@@
@@
@@
@@
@@
@@
@@
@@
@@
@@
@@
@@
@@
@@
@@
@@
@@
$
PO
UB
DU/
BN
F@
@@
@@
@@
@@
@@
@@
@@
@@
@@
@@
@@
@@
@@
@@
@@
@@
@@
@@
@@
@@
@@
@@
@@
@@
@
/
PUF
JO
6
4
"
UI
JT
D
BSE
N
VT
UC
FS
FUV
SO
FE
UP
W
BMJE
BUF
X
BSS
BO
UZ
*.
1
0
3
5"
/
5
*.
1
0
3
5"
/
5
Summary of Contents for 1000 Series HT
Page 15: ... This page intentionally left blank Blank page ...
Page 33: ...25 Model 1000 Series LT Installation Guide 1000 Series HT Installation Guide ...
Page 42: ...34 This Page Intentionally Left Blank Blank Page ...
Page 50: ...42 Blank Page This Page Intentionally Left Blank ...
Page 57: ...49 Replacement Parts Hood 3 4 5 2 1 6 7 8 9 ...
Page 59: ...51 Replacement Parts 9 10 11 15 16 12 13 14 1 2 4 5 6 7 8 3 9 TEMPERATURE GUAGES 17 ...
Page 65: ...57 Replacement Parts 11 14 2 3 4 5 6 1 10 11 12 13 9 7 8 15 15 16 17 18 Low Temp ...
Page 69: ...61 Replacement Parts 1 3 8 8 8 8 9 9 6 7 5 4 2 2 2 2 2 11 12 13 14 15 16 10 ...
Page 71: ...63 1 2 3 4 5 Replacement Parts ...
Page 73: ...65 Replacement Parts ...
Page 75: ...67 Replacement Parts ...
Page 76: ...68 This page intentionally left blank Blank Page ...
Page 78: ...70 Blank Page This page intentionally left blank ...
Page 79: ...Electrical schematics Timer cycle chart High temperature model 71 ...
Page 80: ...72 ...
Page 81: ...Electrical schematics Timer cycle chart Low temperature model 73 ...
Page 82: ...74 ...