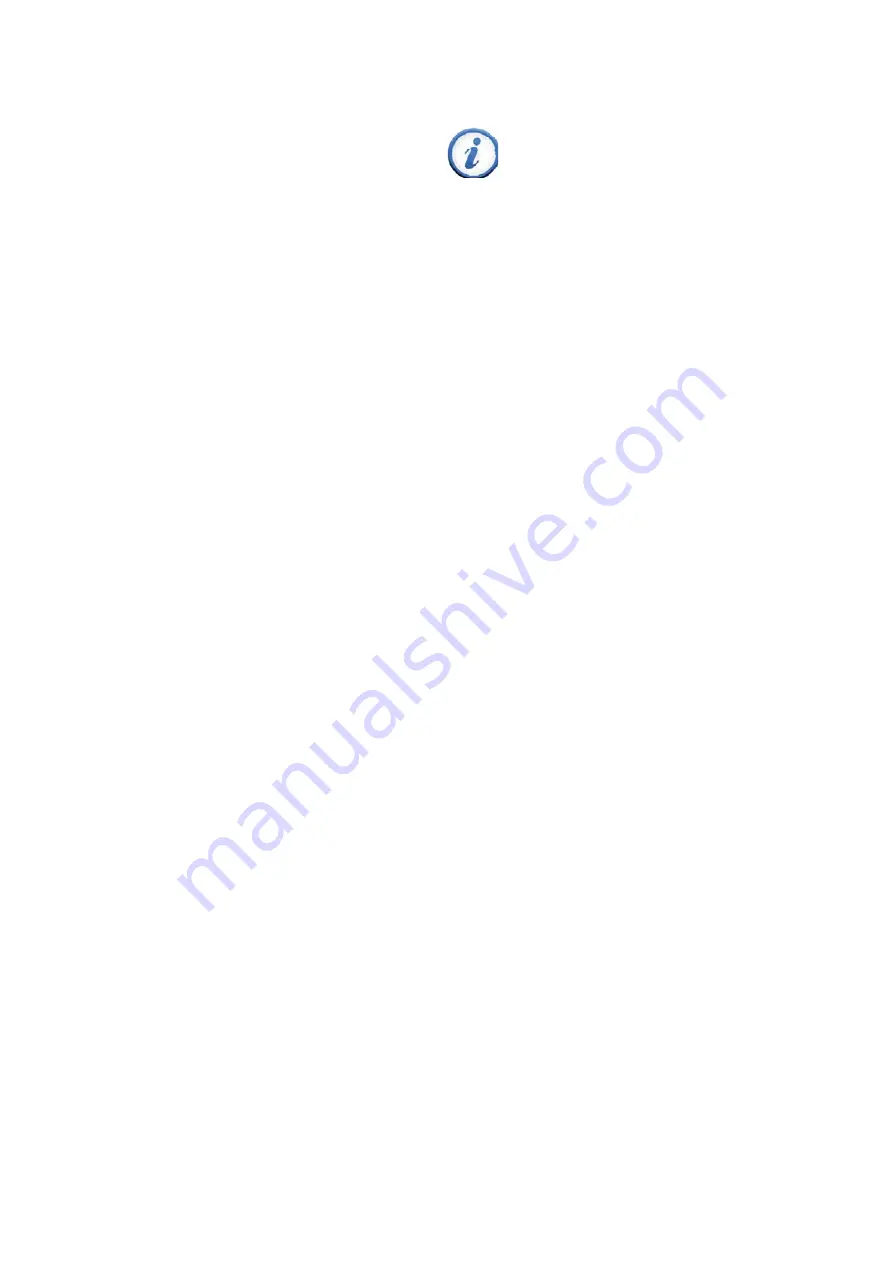
3.0 Installation
17
Genie S
Pool pump fl ow rate
This heater has a very low resistance to pool water
fl ow and will tolerate a wide range of fl ows.
The minimum recommended fl ow is:
80 litres/min
3.9 CONDENSATE CONNECTION
The direction of the plastic condensate drain pipe
connection can be altered from the factory position
on the left, to the right.
•
Remove the blanking plate from the right hand
side
(See illustration in 3.5)
.
•
Loosen the two screws holding the trap
bracket and swivel the trap through 90 degrees.
•
Secure the bracket and fi t the supplied 40 mm
pipe.
•
Example installations are shown on next page
•
Fit blanking plate to the left hand side
(See illus-
tration on next page).
Where possible an internal termination of the con-
densate discharge pipework should be used. If this is
not possible external pipes should be kept as short
as possible and insulated.
Where fi tted in pipework that includes another trap
or a pump, for example the fi lter backwash pipework
to drain, an air break should be fi tted between the
heater and that pipework. Avoid connecting to a
kitchen sink trap as the solids and fats in the drain
will cause a blockage.
It is permissible to connect to an external gully or
rain water hopper provided they connect to a com-
bined system. The condensate should not be run into
a ‘grey water’ recycle system.
If the condensate pipe is connected to a stack it
should join not less than 450 mm above the foot of
the stack. In addition it should be positioned so there
no chance of cross-fl ow to another connection.
Installation pipework must be in 40 mm Hunter
plastic pipe to a suitable drain location with a gradi-
ent of 2.5° (45mm/ metre run) minimum. If connected
to another drainage trap, an air break is required
between the heater drain and that trap
(See illustra-
tion on next page).
Horizontal external pipework should be avoided if at
all possible. If not possible, the pipes should be insu-
lated or trace heated to help prevent the condense
liquid freezing.
Check during commissioning that there is a leak
free working connection from the heater to the drain.
The simplest way to do this is to carefully pour some
water into the boiler fl ue and check it emerges at the
drain. This will also fi ll the trap ready for operation.
3.7 TERMINAL GUARD
& ROOF
TERMINAL
The fl ue outlet from this heater is low temperature
(normally below 60
O
C) so a guard is only required
if the terminal is in a position where it may be dam-
aged or blocked. A suitable guard is available from:
TFC Ltd.
01732 351555, Model DK6
The vertical roof terminal should be fi tted in a mini-
mum of 300mm clear unobstructed space. It is not
permitted to alter the construction of the terminal,
above the roof line, however the concentric section
below the roof line can be altered to suit the installa-
tion.
It is recommended that:
1. The Installation of the fl ues are completed before
connection to the heater. This will ensure that
any debris from the construction of the fl ue does
not enter the heater.
2. Whenever possible bends in vertical fl ues are 45
degrees.
3. Flues may be reduced in length by cutting. The
inner fl ue pipe should be cut so it is 5 to 10mm
longer than the outer Air duct. It will ease assem-
bly if the cut edges are cleaned, chamfered and
greased before assembly.
3.8 POOL WATER PLUMBING
The heater requires pool water to be fl owing to operate
and this is achieved via a pressure switch in the pool
water fl ow. It must therefore be installed downstream
of the fi lter and pump.
A typical installation is plumbed as follows:
1. The Pump outlet is plumbed to the inlet of the fi lter.
2. The outlet side of the fi lter is then plumbed to the
inlet of the heater.
3. The outlet of the heater is plumbed to the return
line to the pool or spa. The pump, fi lter and heater
are plumbed in series.
If it is necessary to install a valve on the return to the
pool then it is recommended that a fl ow switch is in-
stalled and interlocked with the heater supply.
The heater must be located so that any water leaks
will not damage the structure of adjacent area. The
heat shunt connections of the heater, can be made in
standard plastic 1½” pipe supplied demountable.
Use the pressure loss chart in
2.15
to specify a suit-
able pump.
Connection to the heater can be made from either
left to right, or right to left, it is supplied with the
‘From Pool’ connection on the left. To change, undo
the demount connection on the
right,
complete with
blanking plates, and swap with the connections on
the
left.
Ensure that the pool sensor is correctly posi-
tioned in its pocket after the change.
Summary of Contents for MB20S
Page 2: ...Condensing pool heater 2 Genie S Blank page ...
Page 32: ...5 0 Fault finding 32 Genie S Fig 11 0 5 4 SCHEMATIC WIRING ...
Page 39: ...Condensing pool heater 39 Genie S Blank page ...
Page 40: ...Station Lane Industrial Estate Witney Oxon Tel 01993 778855 Fax 01993 703407 June 2020 Rev J ...