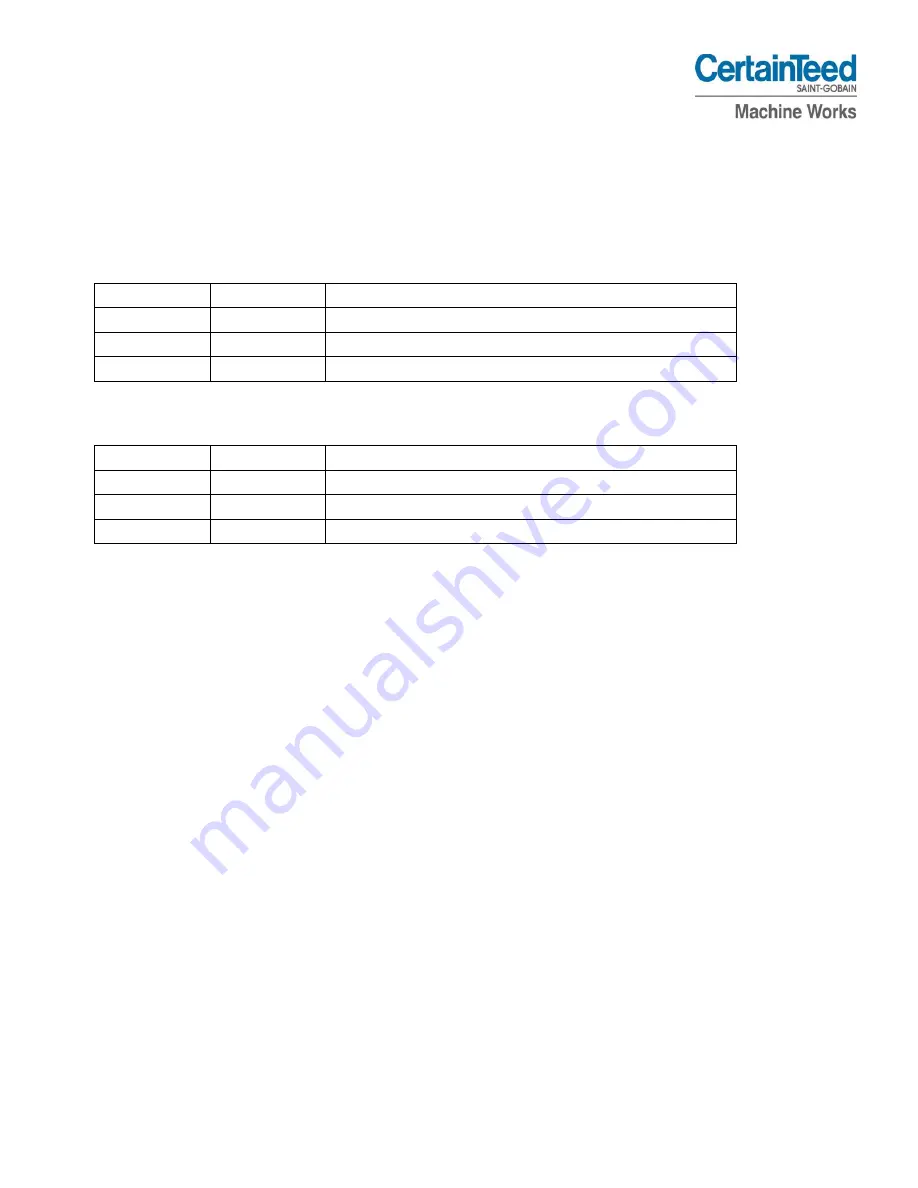
2
Optional Equipment
Wireless Remote (SKU # 163606)
150’ Wired Remote Cord (SKU # 212344)
100’ Hose Package (SKU #212217)
SKU #
Quantity
Description
162885
2
Mark II Clear Hose 3.0" X 50'
210991
1
Hose Sleeve, 3.0"
162483
4
3.0" SS Hose Clamp
150’ Hose Package (SKU #212343)
SKU #
Quantity
Description
162885
3
Mark II Clear Hose 3.0" X 50'
210991
2
Hose Sleeve, 3.0"
162483
5
3.0" SS Hose Clamp
Summary of Contents for BOLT 3
Page 8: ...6 Figure 1 3 1 9 4 5 6 7 8 10 11 12 ...
Page 17: ...15 Figure 8 ...