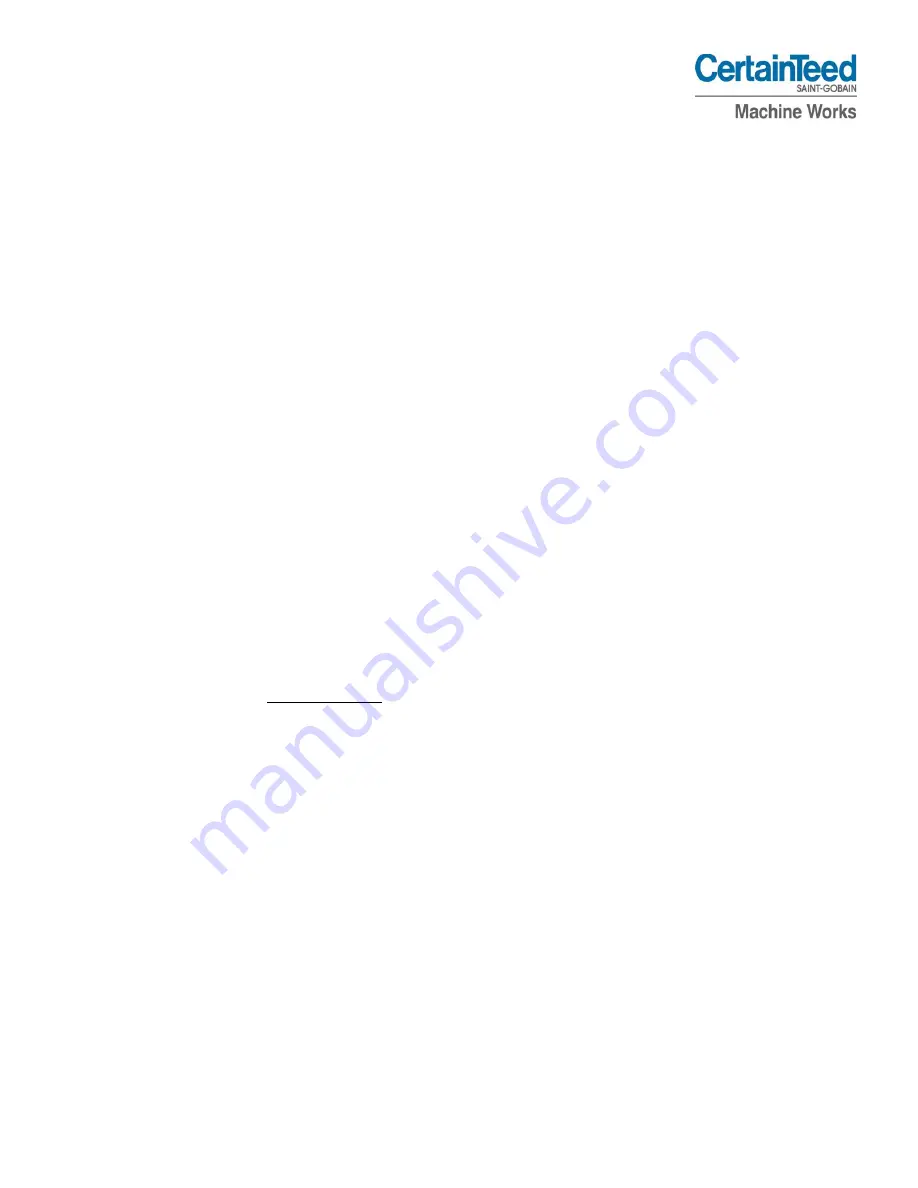
9
5.
Remove blowing hose, empty hopper (if necessary), and store properly
Preventive
Maintenance
Periodic preventative maintenance will keep your
BOLT 3
in good operating condition and
reduce downtime. Keep the machine clean by preventing material from collecting on the vent
holes and install a clean filter in the machine during operation.
Airlock Feeder:
Worn or torn seals can greatly affect the
BOLT 3
performance allowing
insulation and air to escape the feeder, producing a slow feed rate and lower coverage.
CTMW recommends that the seals be changed every 250 hours of operation for optimal
performance. Follow the directions
on ‘Seals Replacement’ section to change seals.
Casters:
Keep the casters clean of debris and dirt.
Filter:
Replace filter when it becomes clogged or dark in color. Having a new filter in the
machine will greatly increase performance and efficiency.
Bearings:
Bearings are self-aligning, pre-lubricated, and double sealed. If the bearings seem
noisy or damaged, replace the bearings.
Chain:
Lubrication is not to be used as this can cause the chain to collect material and wear
the chain and sprockets prematurely. The chains should be taught but not overtightened. A
loose chain should be replaced.
Electric Motor/Speed Reducer:
The electric motor and speed reducer should run smoothly
without interruption. Bad bearings, low voltage, or improper power supply could cause motor
failure. If the motor will not run refer to the troubleshooting section.
Agitators & Auger shaft assemblies:
The auger and steel agitators require no maintenance.
Once extreme wear is noticeable on the metal agitators, auger, or shaft assembly they will
each have to be replaced as a single unit.
Blower Motors:
If the blower produces noises or does not start refer to the troubleshooting
section of this manual.
Summary of Contents for BOLT 3
Page 8: ...6 Figure 1 3 1 9 4 5 6 7 8 10 11 12 ...
Page 17: ...15 Figure 8 ...