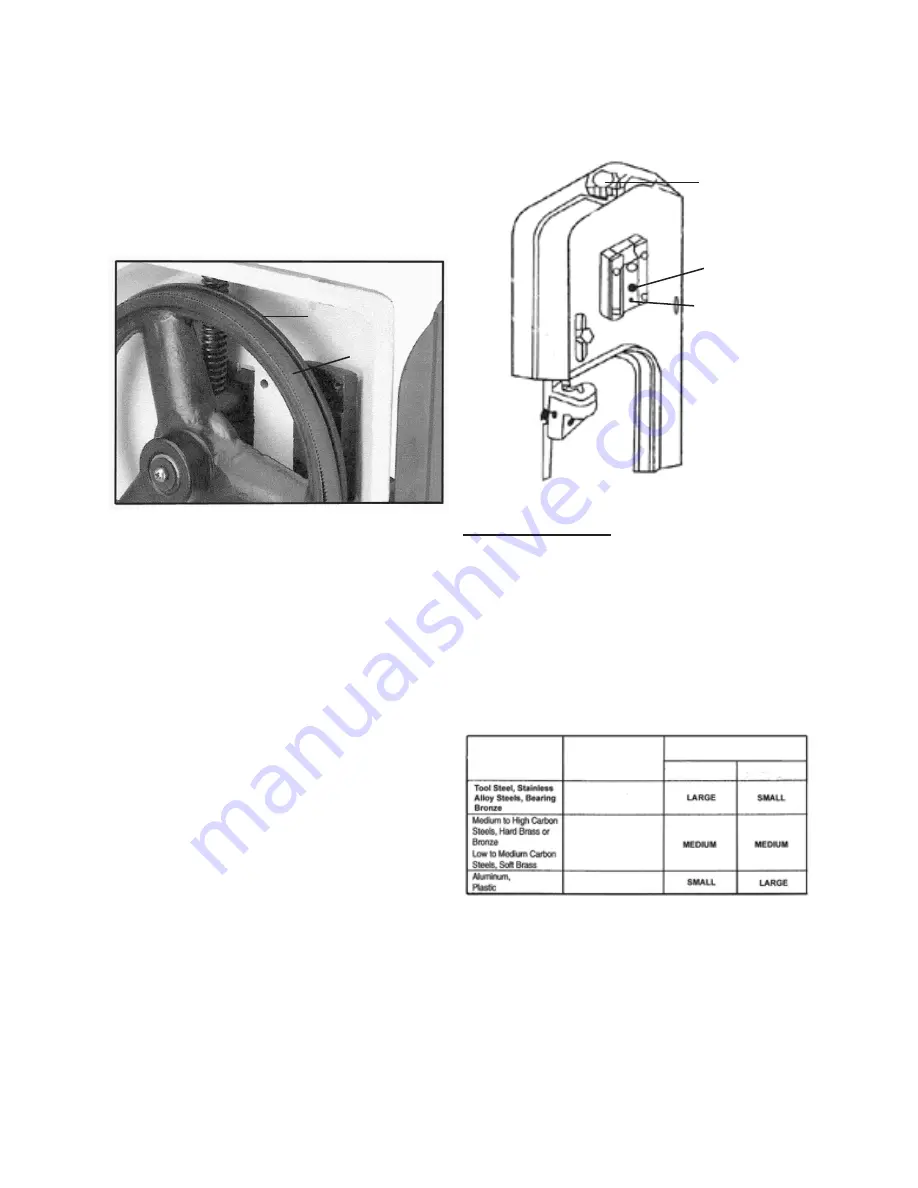
SKU 66435
For technical questions, please call 1-800-444-3353.
Page 14
The Saw Blade (86) is tracking prop-
2.
erly when the back of the Blade is
just touching the edge of the Blade
Wheel (64) flange. The back of the
Blade should not be rubbing against
the flange.
(See Figure j.)
BLADE WHEEL
FLANGE
(64) SAW
BLADE
(86)
FIGUrE j
If adjustment is necessary, loosen the
3.
upper Hex Head Bolt (56) to a point
where it is loose, but snug.
(See Figure K.)
With the Bandsaw running, turn the
4.
lower Hex Head Screw (110) until the
Saw Blade (86) is tracking properly,
making sure Blade tension is main-
tained by turning the Blade Tension
Adjusting Knob (125).
(See Figure K.)
Make sure to retighten the upper Hex
5.
Head Screw (56) when adjustment is
complete.
(See Figure K.)
HEx HEAD
SCrEW
(56)
HEx HEAD
SCrEW
(110)
FIGUrE K
BLADE
TENSION
ADjUSTING
KNOB
(125)
Changing Speed:
When using the Bandsaw, always
1.
change the Saw Blade (86) speed to
best suit the material being cut. Refer
to the Chart to determine the proper
cutting speed for a specific type of
material being cut.
(See Figure L.)
FIGUrE L
MATErIAL
SpEED (FpM)
BELT GrOOVE USED
WOrM GEAr
pULLEY
MOTOr
pULLEY
80 FpM
120 FpM
180 FpM
The cutting speed can be adjusted by
2.
loosening the Screw (102) and mov-
ing the Motor (94) forward. Open the
Upper Pulley Cover (92). Place the V-
Belt (128) around the desired grooves
in the Worm Gear Pulley (115) and