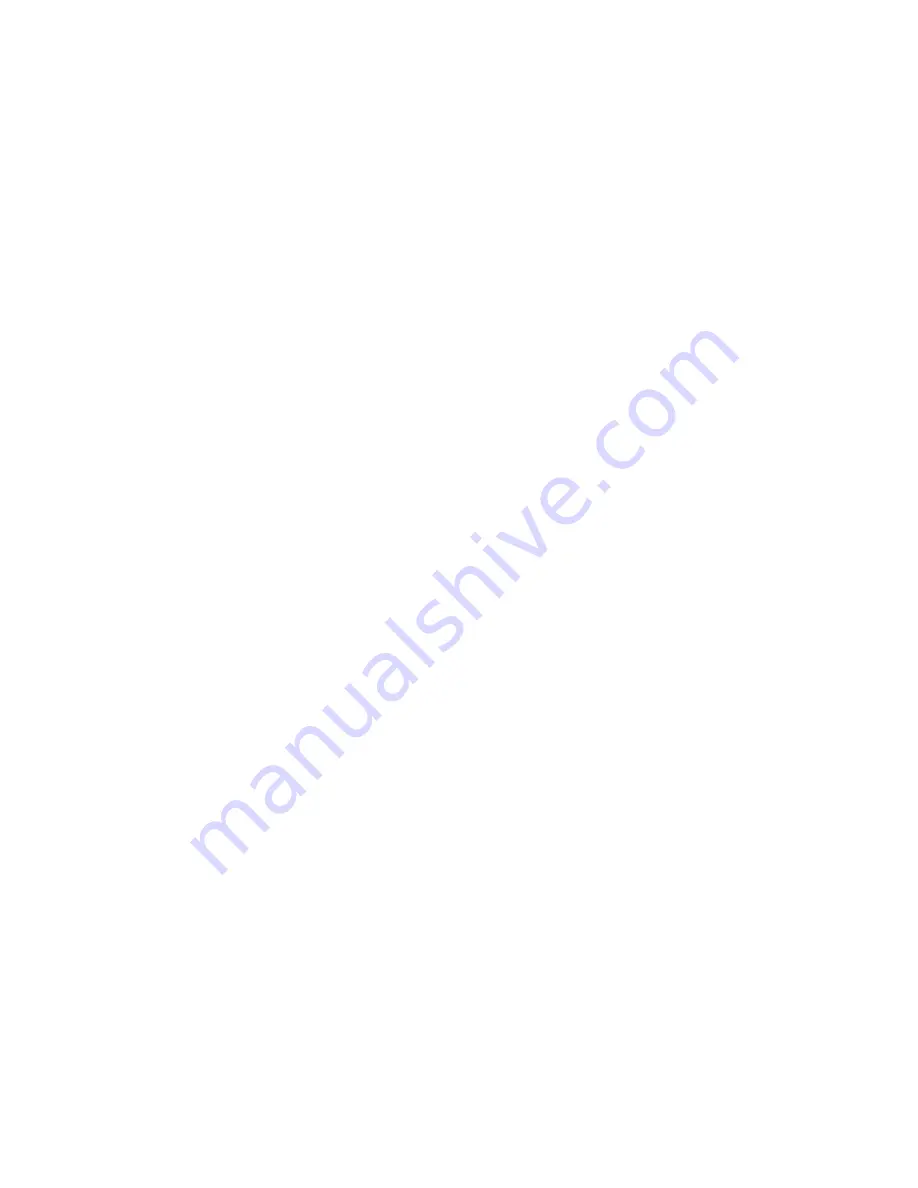
CENTENT COMPANY
use the lowest reasonable gain setting, and then adjust the damping to the lowest setting
possible without ringing or overshoot.
INTEGRAL COEFFICIENT
The third element in a PID compensation loop is the integral gain coefficient. The gain is
fixed for this component and is not adjustable by the user. The purpose of the integral
coefficient is to “take up” or eliminate over time any remaining position error. There is
always a position error that the proportional coefficient cannot remove because it becomes
less effective as the position error decreases.
The integral coefficient works by “integrating” over time any remaining position error. This
means any residual error becomes multiplied over time, restoring the motor to the command
position with zero error. The integral gain coefficient is not settable on the CN0182.
The motor will be perfectly still when not commanded to move if sine-cosine encoders are
used. This is because the integral coefficient reduces any position error to zero.
If TTL encoders are used, the motor will bounce between two adjacent encoder count edges
when not commanded to move. This is because there is not position feedback information
between count edges. Any residual position error, no matter how small, is multiplied over
time to a level sufficient to move the motor. The motor then moves until it reaches an
encoder count edge, where it reverses direction until it hits the other constraining encoder
count edge, repeating the process.
Using the minimum Gain Trimpot setting for TTL encoders helps reduce bounce. The higher
the gain the higher the Damping Trimpot setting, both of which contribute to how strongly
and rapidly the motor will bounce between the adjacent encoder count edges. The stronger
the motor bounces, the more torque is required. This results in unnecessary motor heating,
vibration and audible noise.
SERVO LOOP TUNING
A DC servo drive must be "tuned" to the application to achieve optimum system stability.
This consists of adjusting the Gain and Damping Trimpots to the correct values for the
particular motor and load combination the CN0182 is driving.
The tools needed are:
•
A STEP and DIRECTION pulse source or 2 FUNCTION GENERATORS
•
A 2 channel OSCILLOSCOPE with 10:1 probes
•
A small SCREWDRIVER
Begin by connecting the power supply and the encoder to the CN0182. Do not connect the
motor or pulse source yet. Jumper the Option Header for the type of encoder being used (pins
9, 10) and the expected moment of inertia. The default is Low Inertia (pins 3, 4).
Turn on the power supply. The Fault LED should light momentarily when power is applied.
23
Summary of Contents for CN0182
Page 4: ......