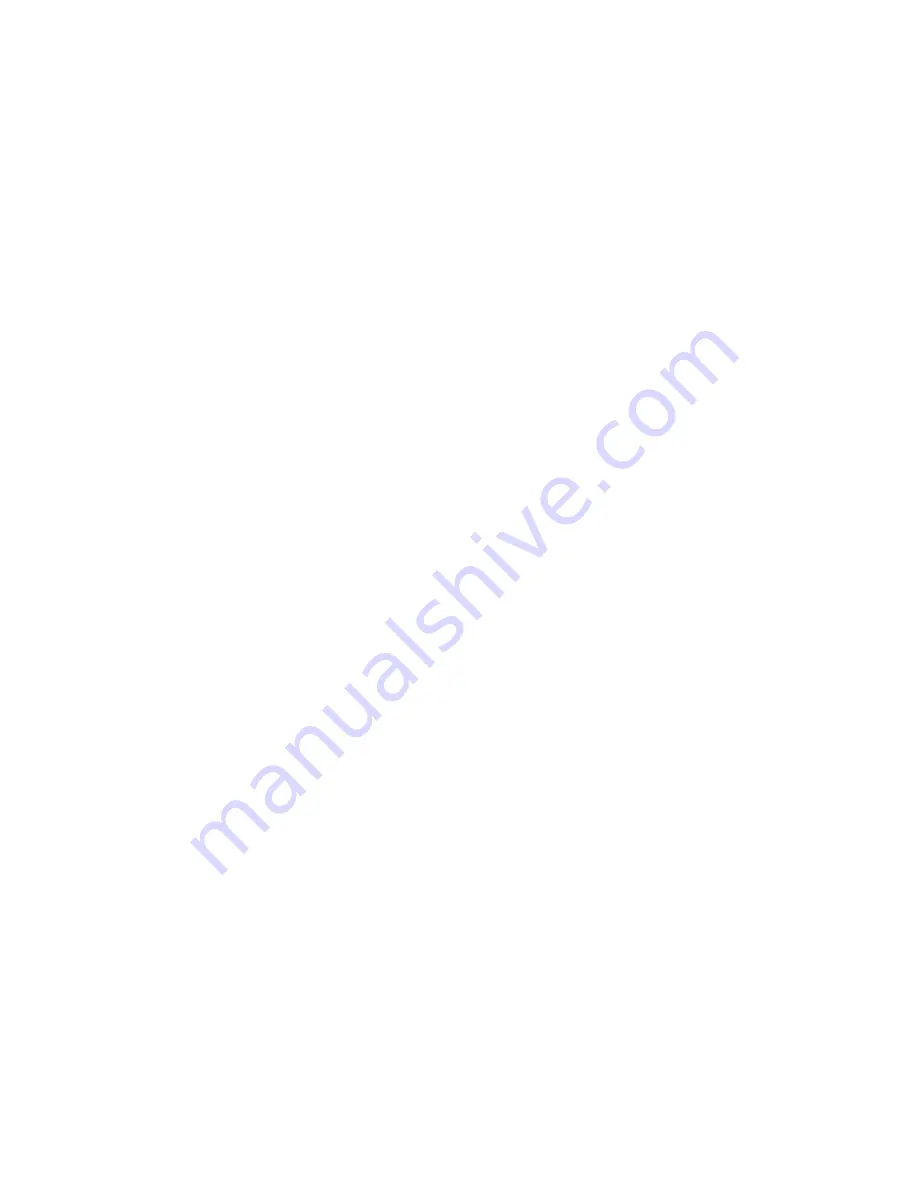
CENTENT COMPANY
•
Position Error Limit
The Position Error Limit Circuit monitors the difference between the command position
and the actual motor position. If this difference exceeds
±
128 counts, the servo lock is
considered broken and the position can not be recovered. The result would be a
runaway motor and possible damage to system components. Before this condition is
reached, the Position Error Limit Circuit sets the Fault Latch, shutting down the drive.
Possible causes of a Position Error Limit trip are many; the most common, and their
remedies are:
1. Unstable Loop
Improperly set Gain and Damping trimpot settings are the causes here. This generally
shows up during the initial setup phase. If the damping setting is too low, the motor
will begin to oscillate. When the oscillation amplitude reaches
±
128 counts, the
CN0182 will shut down. Increase the damping setting and try again. If the gain setting
is to low, the drive will be sluggish in responding and an error approaching
±
128
counts can develop. Increase the gain setting slightly and try again.
2. Broken Loop
The CN0182 is part of a closed-loop system. The CN0182 drives the motor, the motor
turns the encoder and the encoder sends feedback information back to the CN0182,
completing the loop. Any malfunction in this loop will result in a position error and a
protective shutdown. Verify that the encoder connections to the drive are correct and
that there are no breaks in the wiring or terminals.
3. Insufficient Torque At High Speed
DC motor torque is at a maximum at zero speed (stall torque) and linearly decreases to
zero at the motor’s maximum speed (no-load speed). Consequently, the motor’s ability
to provide torque decreases as speed increases. The options here are to increase the
power supply voltage or use a motor with a higher no-load speed.
Another possible cause may be the frequency limit of the encoder. Many encoders
have a maximum frequency of 100 kHz, or 400,000 counts per second. If a high line
count encoder is used at high speed, this limit may be exceeded. For instance, a 2500
line encoder would be at this limit at 2400 RPM (60 x 100,000 / 2500).
4.
Insufficient Torque At Low Speed
Motor torque is directly proportional to motor current. If the motor is unable to carry a
load at low speed, check to see if the Current Trimpot is set too low. If the motor’s
stall current is less than 20 amps, setting the Current Trimpot beyond the stall current
will not help, since it is the motor and not the drive that limits current. The options
here are to get a higher stall current motor (up to 20 amps) or a motor with a higher
torque constant.
9
Summary of Contents for CN0182
Page 4: ......