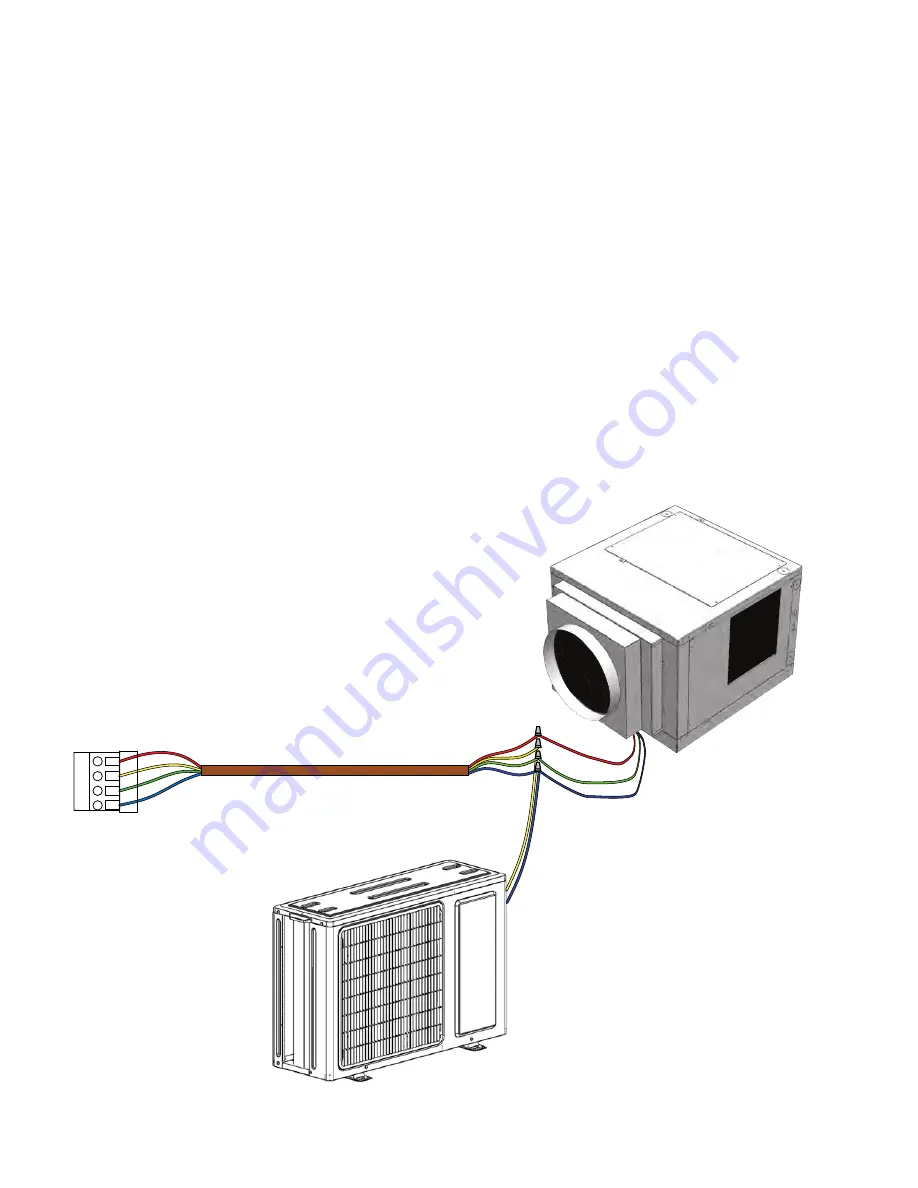
24V THERMOSTAT KIT WIRING INSTRUCTIONS
The 24V thermostat conversion kit requires a standard 18-5 thermostat wire to be run from the evaporator unit to the
thermostat. The white wire will not be used, as there is no heating function. (Some thermostats need a common wire and
some do not; the unit is equipped with a common wire if needed.)18-5 thermostat wire (communication cable) must be run
between the evaporator unit and the condensing unit.
24V Wiring Connections (Evaporator)
1.
Route a standard 18-5 thermostat wire into the evaporator unit.
2.
Locate the wire thermostat connection cable inside of the evaporator unit.
3.
Connect the wires according to color ( red to red, green to green, and blue to blue). Note: The evaporator unit will not
contain a yellow wire. See next step for more information on Yellow wire.
4.
Connect one wire from the 18-5 thermostat wire to the low-voltage yellow wire (1). Then connect the other 18-5 wire to
the blue low-voltage wires (2). The other three wires will not be used.
Thermostat Wiring Connections
Follow the thermostat installation instructions.
NOTE:
The white wire
will not be used, as there is no heating function.
NOTE:
To ensure correct system operation, the 24V thermostat must be
placed inside the wine cellar, preferably in a central location away from
any airflow.
R/RC
Y
G
C
Thermostat
Evaporator Unit
Condensing Unit
Page 22
08/09/21