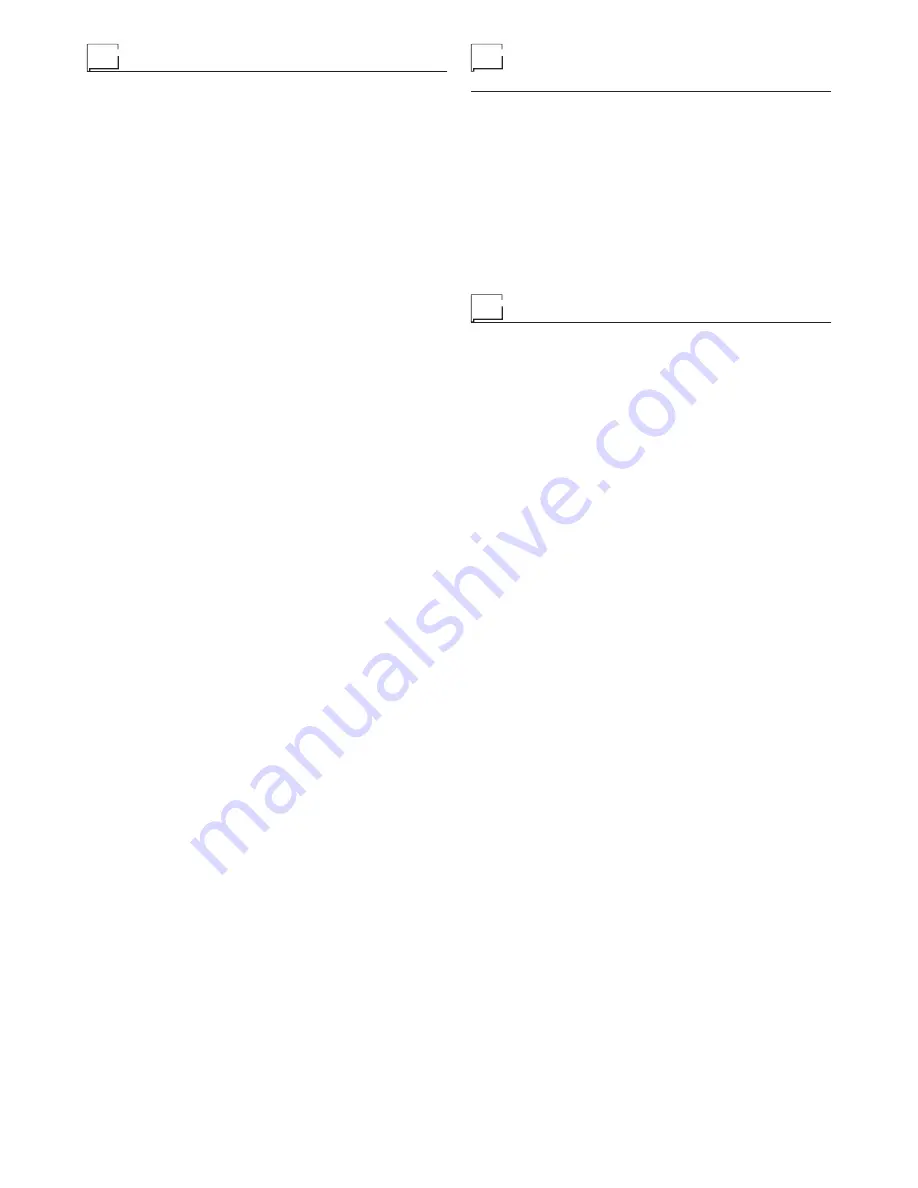
8
Optional
The remote controls can be only used in the 2-STROKE and
4-STROKE welding modes.
MANUAL REMOTE CONTROL
WARNING: When using the machine for TIG welding it is OBLIGA-
TORY to use the kit for simultaneously use – CEA code n° 460056.
Weld current can be measured at a distance by connecting up this
control. The display will show the previous maximum weld current
value set on the welder. The remote control will adjust welding cur-
rent from the minimum to this value (for further information see the
MTA control panel manual). Just turn the adjustment knob on the
welder to change the maximum output value.
FOOT SWITCH
The foot switch replaces the torch button and the welding current
setting knob. The display will show the previous maximum weld
current value set on the welder. The pedal will adjust the welding
current from the minimum to this value (for further information see
the MTA control panel manual). Just turn the adjustment knob on
the welder to change the maximum output value.
NOTE:
•
To use the pedal control correctly, set the “welding mode” to
2-STROKE and then the welding parameters SLOPE UP time
to 0 sec., SLOPE DOWN time to 0 sec.
•
When using the machine for TIG welding the operator can use
the torch button to start the weld and the pedal to regulate the
welding current remotely.
.
AIR AND/OR WATER-COOLED TORCH UP/ DOWN
The up/down torch replaces the current setting knob on the front
of the welder. Press right (+) and left (-) button to adjust the ac-
tive parameter. With this kind of torch, it is also possible to scroll
the saved programmes by pressing the two (+) and (-) buttons.
Turn the knob to scroll the programmes until an empty and unused
programme is found.
NOTE: Programme sequences can be created by placing an emp-
ty programme between saved ones.
NOTE: The value shown on the display during welding represents
the effective current output with all types of control.
The digital control unit of the generator is fitted with a control rec-
ognition device which allows it to identify which device is connect-
ed and take action accordingly. To allow the command recognition
device to work correctly, connect (with the machine switched off)
the required accessory to the relative connector and then switch
on the welding machine with the on/off switch.
NOTE: It is not possible to memorize or open programmes
when the remote controls are connected (except for the torch
with UP/DOWN commands).
If a remote control is connected (followed by self-acknowledge-
ment procedure) the machine will automatically return to the man-
ual-welding phase if it has been pre-set for automatic welding.
The pointing out of any difficulties
and their elimination
The supply line is attributed with the cause of the most common
difficulties. In the case of breakdown, proceed as follows:
1) Check the value of the supply voltage
2) Check that the power cable is perfectly connected to the plug
and the supply switch
3) Check that the power fuses are not burned out or loose
4) Check whether the following are defective:
• The switch that supplies the machine.
• The plug socket in the wall.
• The generator switch.
NOTE: Given the required technical skills necessary for the repair
of the generator, in case of breakdown we advise you to contact
skilled personnel or our technical service department.
Digital interface PCB replacement
• Unscrew the 4 screws fastening the front rack panel.
• Remove the adjustment knob.
• Extract wiring connectors from digital interface PCB.
• Unscrew small supporting columns.
• Remove digital interface PCB by lifting it out of its supports.
• Proceed vice versa to assemble new digital interface PCB.
Summary of Contents for MATRIX 2200 AC/DC
Page 10: ...10 Wiring diagram MATRIX 2200 AC DC...
Page 11: ...11 2101WA31...
Page 12: ...12 Wiring diagram MATRIX 3000 AC DC AC DC R 3000 MTA 30...
Page 13: ...13 2101WB09...