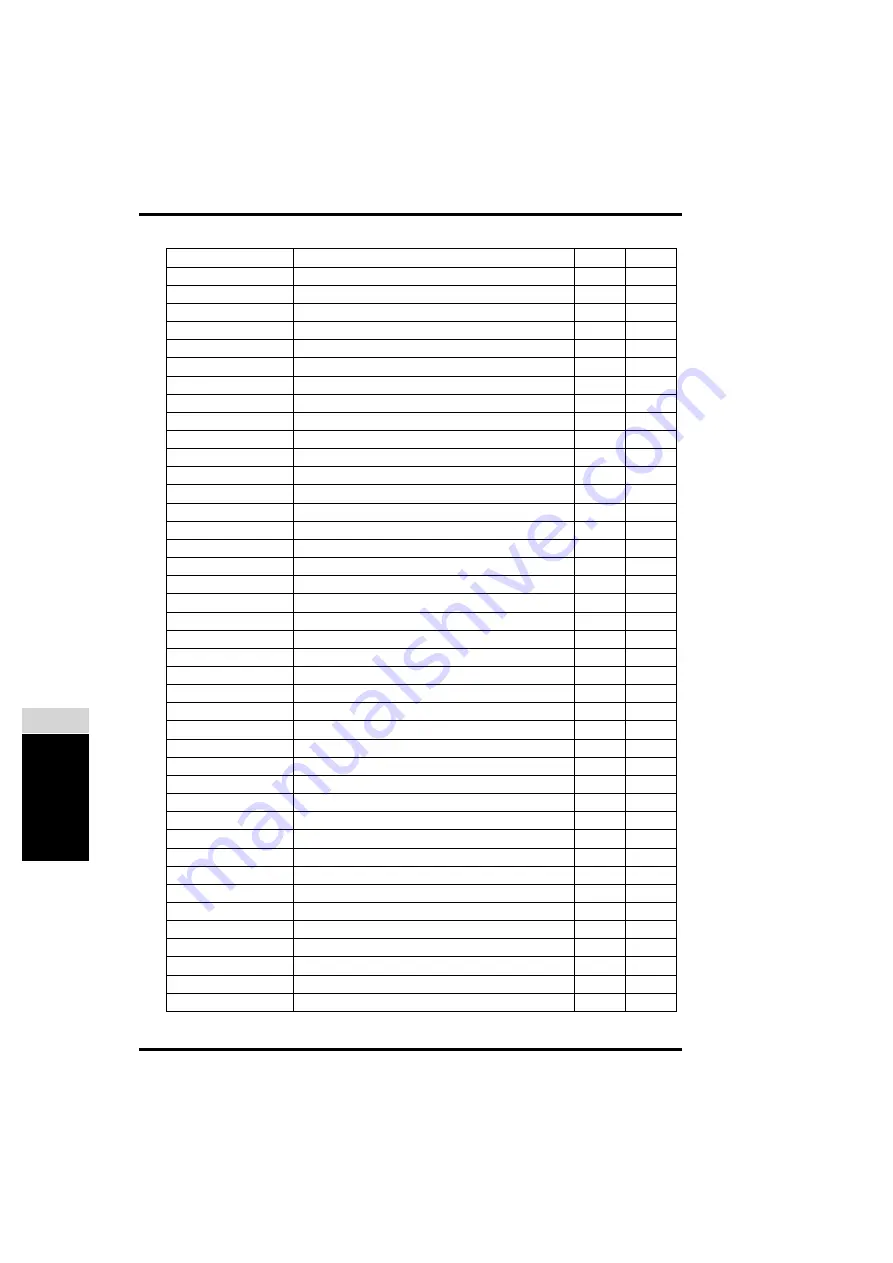
P
a
rt
s Li
st
B
126
1220C GB 19991004
CM+9.9460.2105.0
BEARING
121
10
CM+9.9460.2106.0
BEARING
121
11
CM+9.9460.2258.0
BEARING
99
07
CM+9.9460.2330.1
ROLLER
101
04
CM+9.9460.2330.1
ROLLER
115
06
CM+9.9460.2561.0
COVER
97
13
CM+9.9460.2562.1
SETTING KNOB
97
14
CM+9.9460.2590.0
STEP SWITCH
97
15
CM+9.9462.1017.3
TABLE PLATE
93
13
CM+9.9462.1019.1
MEASURING PIN
93
14
CM+9.9462.1021.0
MOUNTING PLATE
117
01
CM+9.9462.1027.0
SPUR GEAR
103
30
CM+9.9462.1027.0
SPUR GEAR
109
30
CM+9.9462.1027.0
SPUR GEAR
111
29
CM+9.9462.1034.2
SNAP SPRING
93
15
CM+9.9462.1035.0
REDUCING PART
93
16
CM+9.9462.1043.0
RED BOTTLE RECEPTACLE (DEVELOPER)
93
18
CM+9.9462.1044.0
BLUE BOTTLE RECEPTACLE (FIXER)
93
19
CM+9.9462.1045.0
WHITE BOTTLE RECEPTACLE (WATER)
93
20
CM+9.9462.1052.2
PIN
93
21
CM+9.9462.1105.0
PROTECTING CAP
93
23
CM+9.9462.1106.0
HOLDER
93
24
CM+9.9462.1107.0
HOLDER
93
25
CM+9.9462.1111.1
SNAP CASE
93
26
CM+9.9462.1175.0
COVER
93
40
CM+9.9462.1202.3
SHAFT
97
08
CM+9.9462.1203.2
SHAFT
99
09
CM+9.9462.1204.0
HELICAL SPUR GEAR
99
10
CM+9.9462.1205.1
SHAFT
99
11
CM+9.9462.1206.0
HELICAL SPUR GEAR
99
12
CM+9.9462.1207.1
SHAFT
97
18
CM+9.9462.1211.1
SHAFT
99
13
CM+9.9462.1212.0
HELICAL SPUR GEAR
99
14
CM+9.9462.1213.2
SHAFT
99
15
CM+9.9462.1214.0
HELICAL SPUR GEAR
99
16
CM+9.9462.1215.0
PIPE UNION
99
17
CM+9.9462.1218.0
SPUR GEAR
99
18
CM+9.9462.1219.1
TRANSFER GEAR
97
09
CM+9.9462.1221.1
PLATE
99
19
CM+9.9462.1252.3
BUSHING
97
24
CM+9.9462.1253.3
BUSHING
99
21
Part code
Description
Page
Item
Summary of Contents for 2000 IR
Page 5: ...Preface Introducing the Cawomat 2000 IR 1220C Cawomat 2000 IR RM 07 10 99 14 17 Page 1...
Page 6: ...1220C GB 19991004 2 Preface 0 1220C Cawomat 2000 IR RM 07 10 99 14 17 Page 2...
Page 12: ...1220C GB 19991004 8 Installation 1 1220C Cawomat 2000 IR RM 07 10 99 14 17 Page 8...
Page 22: ...1220C GB 19991004 18 Installation 1 1220C Cawomat 2000 IR RM 07 10 99 14 18 Page 18...
Page 24: ...1220C GB 19991004 20 Getting started 2 1220C Cawomat 2000 IR RM 07 10 99 14 18 Page 20...
Page 38: ...1220C GB 19991004 34 Cleaning 3 1220C Cawomat 2000 IR RM 07 10 99 14 18 Page 34...
Page 50: ...1220C GB 19991004 46 Troubleshooting 4 1220C Cawomat 2000 IR RM 07 10 99 14 18 Page 46...
Page 87: ...A Appendix Equipment information sheet 1220C Cawomat 2000 IR RM 07 10 99 14 20 Page 83...
Page 88: ...1220C GB 19991004 84 Specifications A 1220C Cawomat 2000 IR RM 07 10 99 14 20 Page 84...
Page 93: ...B Appendix Parts list and exploded views 1220C Cawomat 2000 IR RM 07 10 99 14 20 Page 89...
Page 94: ...1220C GB 19991004 90 Parts list B 1220C Cawomat 2000 IR RM 07 10 99 14 20 Page 90...
Page 135: ...C Appendix Index 1220C Cawomat 2000 IR RM 07 10 99 14 27 Page I 1...
Page 136: ...1220C GB 19991004 I 2 Index C 1220C Cawomat 2000 IR RM 07 10 99 14 27 Page I 2...
Page 141: ...1220C Cawomat 2000 IR RM 07 10 99 14 27 Page I 7...