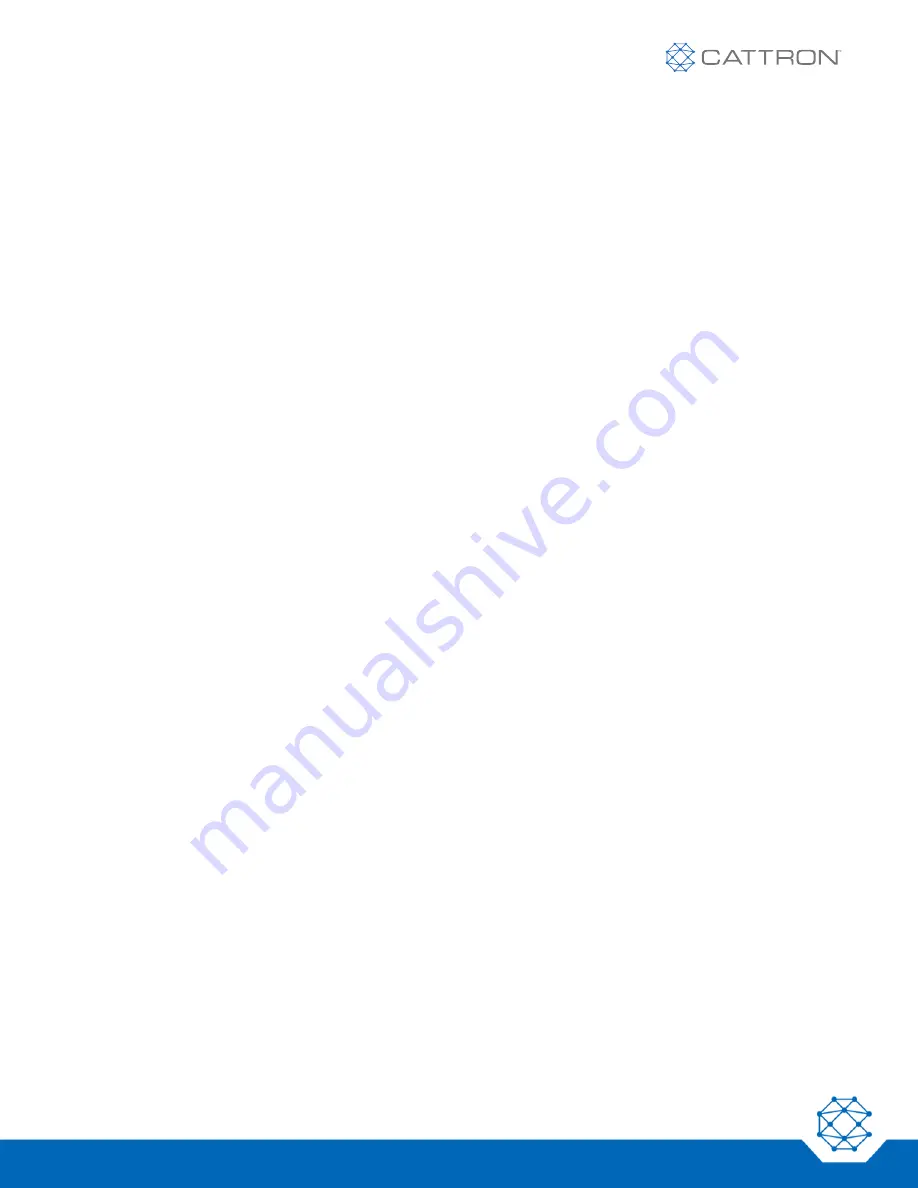
CANplus
TM
CP800
Control Panel Operation Manual
4
9M02-1000-A201-EN
Revision E
Configuring RPM and Time Profile Settings.................................................... 30
CANplus
TM
CP800
Control Panel Operation Manual
4
9M02-1000-A201-EN
Revision E
Configuring RPM and Time Profile Settings.................................................... 30