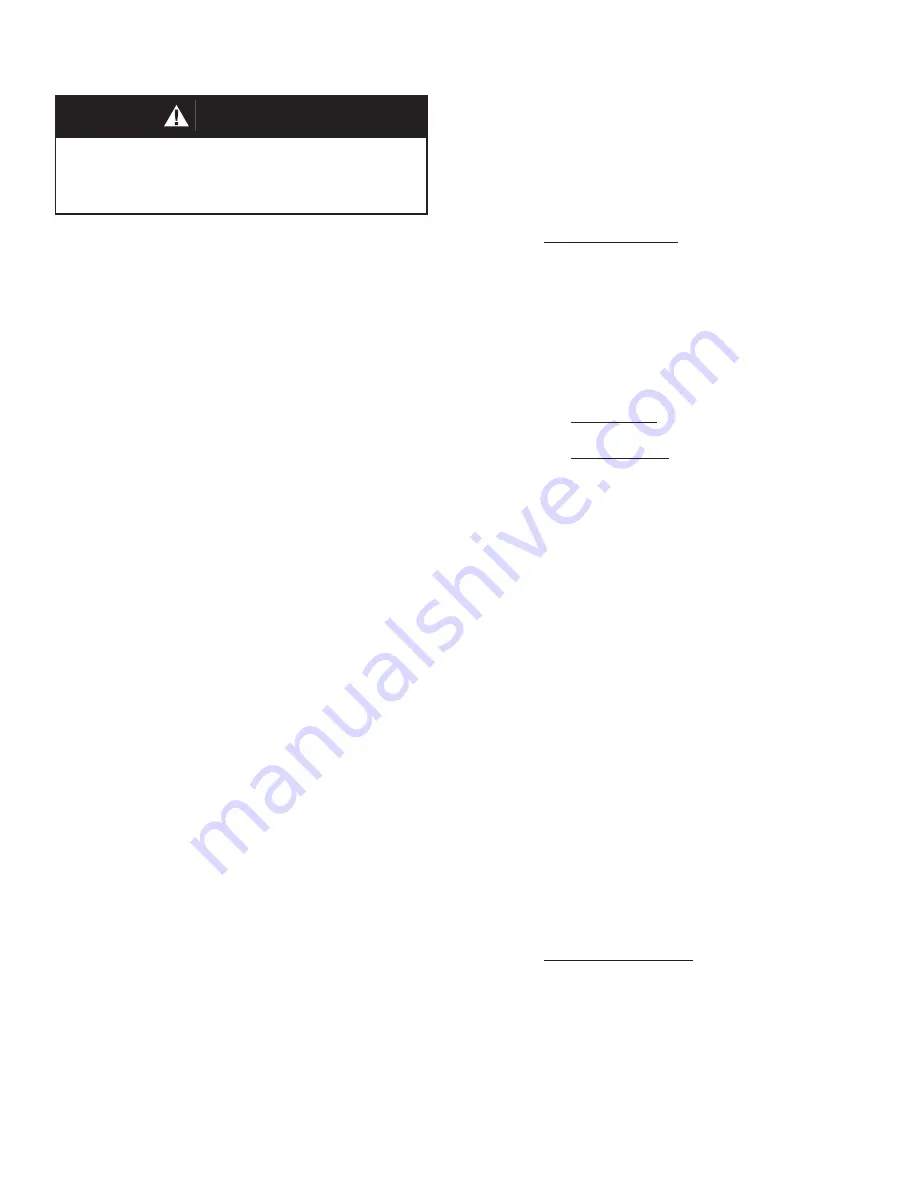
IOM-DA8
6
1. Shut down the system in accordance with
Section
VI.
2. Disconnect the external sensing line, if
in
stalled.
3. The quick change trim allows for the disas-
sembly of the regulator while installed in the
pipeline. Alternatively the maintenance can
be done in a shop area.
NOTE:
It is easier to
repair the regulator when mounted upright in
a horizontal pipe run compared to a vertical
pipe run or a regulator mounted with spring
facing down. The description hereafter will
assume shop disassembly.
4. Place the valve unit in a vise with the spring
chamber (4) upwards.
5. Relax range spring (6) forces by turning ad-
justing screw (1) CCW (viewed from above)
until spring relaxes. The easiest way to check
this, is to carefully loosen the locknut (item
2). If the adjusting screw (item 1) sinks into
the chamber as the locknuts are loosened,
then the spring assembly is still in extension.
Turn the adjusting screw CW to remove the
extension. Fully remove the locknuts.
6. Loosen the diaphragm flange bolts (11) and
nuts (12) uniformly.
7. Place matchmarks on body (23) and spring
chamber (4) flanges. Com plete ly remove bolt-
ing (11,12) Re move the spring cham ber (4).
8. Remove spring follower (5) and spring (6.1).
9. Grasp opposite edges of diaphragm (9) and
withdraw the ITA from within the cage (19).
Set the ITA aside.
10. Evenly loosen the cage cap screws (18) in
single revolution increments until fully loos-
ened; remove cage cap screws (18).
11. Pull cage (19) up and out of body to remove
o-ring (15).
12. Remove lower cage gasket (21).
13. For metal diaphragm constructions, remove
diaphragm gasket (37) from body (23) di a-
phragm flange.
14. Remove body (23) from vise. Solvent clean
all removed metal parts.
C. Disassembly of the ITA:
1. Body Sizes 1/2" – 2". (See Figures 2 through
4):
a. Obtain two pieces of square-section
barstock with a 3/8"-7/16" dimension,
approximately 2 inches long.
b. Place plug (20) into a vise using the bars
of a. above positioned on "flats" located
on plug (20) to prevent vise jaw marks
from direct surface contact with the plug
(20). Orient with diaphragms on topside.
c. Sizes 1/2"-1": Remove diaphragm lock nut
(7) by rotating CCW.
Sizes 1-1/4"-2": Remove diaphragm cap-
screw (7) by rotating CCW.
d. Remove upper diaphragm pressure plate
(8).
e. Remove diaphragm(s) (9, 9.1, 9.2, 9.9).
Examine diaphragm(s) to determine
wheth er failed; determine if op er at ing
conditions are ex ceed ing pressure drop
or temperature lim its.
f. For composition diaphragm con struc tion,
remove upper stem seal (14.1).
g. For metal diaphragm con struc tion, re move
lower pusher plate gasket (14.4).
h. Remove lower diaphragm pusher plate
(10). For 1/2"-1" sizes, remove spacer
(13).
i. Remove middle stem seal (14.2).
j. Remove plug (20) from vise, ro tate end-
for-end, and resecure in vise using same
metal bars above.
k. Loosen seat disc nut (30) CCW (viewed
from above) ap prox i mate ly two (2) rev o lu-
tions.
l. Remove assembly (20, 27, 28, 29, 30)
from vise. Complete re mov al of seat disc
nut (30), seat disc washer (29), and seat
disc (28).
2. Body Sizes 2-1/2" – 4". (See Figure 6):
a. Place seat disc nut (30) into a vise with
the plug (20) oriented ver ti cal ly. Do NOT
over-tighten nut (30) in vise.
b. Place closed-end hex wrench onto di a-
phragm locknut (7). Place sock et wrench
on 3/4" hex upper end of plug (20). Loos en
diaphragm lock nut (7) while holding plug
(20) from ro tat ing by socket wrench.
Re move di a phragm lock nut (7) after fully
CAUTION
SYSTEM UNDER PRESSURE. Prior to per form ing
any maintenance, isolate the reg u la tor from the
sys tem and relieve all pressure. Fail ure to do so
could result in personal injury.
B. Main Valve Disassembly: